Adhezijska trdnost elektrodnih premazov
Ne glede na to, ali gre za električni avtomobil, pametni telefon ali sončno baterijo v kleti – baterije so postale sestavni del našega vsakdanjega življenja. Kako pa zagotovite, da so te naprave za shranjevanje energije zanesljive, trpežne in varne? Adhezivna trdnost elektrodnih premazov igra pogosto podcenjeno, a ključno vlogo.
Zakaj je adhezivna trdnost tako pomembna?
V litij-ionskih baterijah – trenutno prevladujoči vrsti baterij – so elektrode sestavljene iz aktivnih materialov, ki so naneseni na kovinske folije (baker za anodo, aluminij za katodo). Te plasti se morajo trajno in trdno oprijeti, saj med polnjenjem in praznjenjem prihaja do mehanskih obremenitev: Materiali se raztezajo, krčijo in so izpostavljeni toplotnim obremenitvam.
Če oprijem ni zadosten, obstaja nevarnost, da se premaz zrahlja, kar ima za posledico izguba moči, padec zmogljivosti ali v najslabšem primeru kratek stik. Preskus adhezije torej ne pomagajo le zagotoviti kakovost, temveč tudi preprečiti morebitna varnostna tveganja.
Kako se preverja trdnost adhezije?
V praksi sta se uveljavili dve metodi:
1. Preskus odlepljanja :
Na premaz se namesti lepilni trak, ki se odlepi pod določenim kotom (običajno 90 ali 180 stopinj). Sila, potrebna za odlepljanje , kaže, kako močno se premaz oprime. Ta metoda je preprosta in hitra, vendar je tudi dovzetna za vpliv operaterja.
2.Natezni preizkus v smeri Z:
Lepilni trak se odstrani pravokotno na površino, kar imenujemo smer Z. Ta metoda je bolj obnovljiva, manj odvisna od kota in je še posebej primerna za raziskave in nadzor kakovosti. Sodobne naprave omogočajo celo preskušanje več vzorcev hkrati.
Obe metodi imata svoje prednosti – proizvajalci pogosto uporabljajo kombinacijo, da dobijo popolnejšo sliko o kakovosti oprijema.
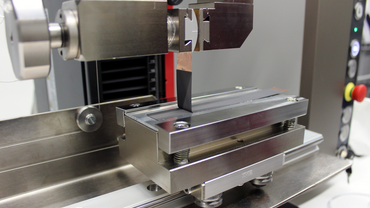
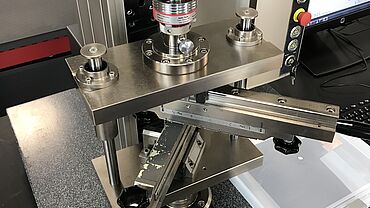
Kaj vpliva na rezultate preskusov?
Kot se pogosto zgodi, se hudič skriva v podrobnostih. Že majhna odstopanja pri pripravi vzorca lahko ponaredijo rezultate:
- Čistoča in poravnava: Ostanki ali neenakomerno lepljenje vplivata na oprijem.
- Kakovost traku: Razlike v debelini, sestavi ali trdnosti oprijema lahko spremenijo vrednosti.
- Okoljski pogoji: Vpliv imata tudi temperatura in vlažnost. Zato je treba preskušanje, kjer koli je to mogoče, izvajati v stalnih pogojih – v nekaterih primerih celo v zaščitni atmosferi.
Praktični izzivi
Osrednje vprašanje: Še vedno ni enotnih standardov za preskus adhezije na baterijah. Medtem ko se drugi sektorji, kot je industrija lepil, lahko opirajo na uveljavljene standarde, tehnologije baterij pogosto nimajo zavezujočih smernic. Različni proizvajalci uporabljajo različne metode, kar otežuje primerljivost.
Prav tako je potrebna optimizacija pri pripravi vzorcev. Avtomatizirana orodja, ki standardizirajo poravnavo, lahko na primer pomagajo povečati ponovljivost, zlasti pri velikih količinah v serijski proizvodnji.
Nove tehnologije, nove zahteve
Z napredkom tehnologije baterij se povečujejo tudi zahteve glede adhezije:
- Polprevodniške baterije: Ne uporabljajo tekočih elektrolitov, kar spremeni ravnovesje sil v celici. Zahtevana je še posebej stabilna povezava med plastmi.
- Silikonske anode: Te se lahko med polnjenjem razširijo do 300 % – pravi preskus obremenitve za kateri koli premaz. Brez zadostne adhezije obstaja nevarnost delaminacije in s tem izgube funkcije celice.
Zgodnji preskusi adhezije v fazi razvoja omogočajo prepoznavanje in reševanje takšnih težav, še preden se pojavijo na terenu.
Pot do standardov in najboljših praks
Dokler ni globalnih standardov, je od proizvajalcev odvisno, ali bodo vzpostavili interne standarde in poskrbeli za čiste procese. To vključuje:
- Enotna priprava vzorcev
- Uporaba enakih lepilnih materialov
- Preskušanje v stabilnih okoljskih pogojih
Hkrati številna podjetja in proizvajalci preskusne opreme sodelujejo pri razvoju zanesljivih protokolov preskušanja – korak k primerljivosti in zagotavljanju kakovosti na ravni industrije.
Zaključek: Majhen preskus, velik vpliv
Merjenje adhezijske trdnosti premazov elektrod se na prvi pogled morda zdi manjša podrobnost, vendar ima v resnici velik vpliv na varnost, učinkovitost in življenjsko dobo sodobnih baterij.
Z vse večjo uporabo novih kemijskih sestavov celic in metod izdelave postaja ta preskus še pomembnejši. Napredek v tehnologiji preskušanja, od nateznega preskusa v smeri Z do integracije mehanskih, toplotnih in električnih meritev, pomaga zagotoviti celovitejšo sliko o obnašanju elektrod v realnih pogojih.
Sporočilo je jasno: Če imate oprijem pod nadzorom, imate baterijo pod nadzorom – danes in v prihodnosti.

O AVTORJU:
Vodja razvoja poslovanja za avtomobilsko industrijo in elektrifikacijo
Če imate kakršna koli vprašanja,
Aleksander Koprivc je pri podjetju ZwickRoell že več kot 20 let opravljal različne mednarodne vodstvene funkcije. Po diplomi iz strojništva v Karlsruheju, diplomi iz mehatronike in magistrskem študiju poslovne administracije (MBA) iz mednarodnega managementa je svoje prve poklicne izkušnje pridobil kot aplikacijski inženir v Nemčiji in Franciji. V podjetju ZwickRoell je bil odgovoren za vodenje prodaje v Franciji in Španiji, poleg tega pa je bil tudi generalni direktor obeh hčerinskih družb. Danes je vodja razvoja poslovanja v diviziji za avtomobilsko elektrifikacijo. Pred tem je več let delal kot vodja industrije v avtomobilskem sektorju.