Forza di adesione sui rivestimenti degli elettrodi
Che si tratti di auto elettriche, smartphone o batterie di accumulo in garage, le batterie sono diventate parte integrante della nostra vita di tutti i giorni. Ma come garantire che questi dispositivi di accumulo di energia siano affidabili, duraturi e sicuri? La forza di adesione sui rivestimenti degli elettrodi gioca un ruolo spesso sottostimato ma cruciale.
Perché la forza di adesione è così importante?
Nelle batterie agli ioni di litio, attualmente le più diffuse, gli elettrodi sono composti da materiali attivi che sono applicati a pellicole in metallo (rame per gli anodi, alluminio per i catodi). Questi strati devono aderire costantemente e saldamente poiché durante il processo di carica e scarica si verificano sollecitazioni meccaniche: i materiali si espandono, si contraggono e sono soggetti a sollecitazione termica.
Se l’adesione è insufficiente, il rivestimento è a rischio distacco con conseguenze come la perdita di potenza, la diminuzione della capacità o, nei casi peggiori, il cortocircuito. Pertanto le prove di adesione non aiutano solo a garantire la qualità, ma consentono anche di prevenire potenziali rischi per la sicurezza.
Come viene testata la forza di adesione?
Dal punto di vista pratico sono stati stabiliti due metodi:
1. Prova di peel:
Un nastro adesivo viene applicato al rivestimento e staccato con una determinata inclinazione (solitamente 90 o 180 gradi). La forza necessaria alla rimozione indica la forza di adesione del rivestimento. Questo metodo è semplice e rapido, ma è anche soggetto all’influenza dell’operatore.
2.Prova di trazione in direzione Z:
Il nastro adesivo viene rimosso in perpendicolare alla superficie, che viene indicata come direzione Z. Questo metodo è maggiormente riproducibile, meno influenzato dall’angolo ed è particolarmente adatto a scopi di ricerca e controllo qualità. Con i moderni dispositivi è anche possibile testare diversi provini allo stesso tempo.
Entrambi i metodi presentano dei vantaggi, i produttori spesso li usano insieme per ottenere un quadro più completo della qualità dell’adesione.
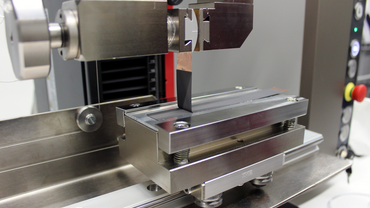
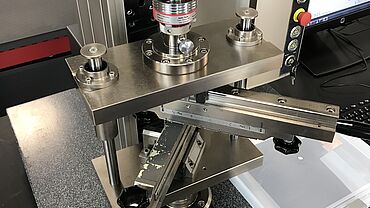
Cosa influisce sui risultati di prova?
Come spesso accade, il diavolo si nasconde nei dettagli. Anche piccole deviazioni nella preparazione dei provini possono falsificare i risultati:
- Pulizia e allineamento: I residui o un incollaggio non uniforme possono influire sull’adesione.
- Qualità del nastro: Differenze di spessore, composizione o forza di adesione possono modificare i valori.
- Condizioni ambientali: Anche temperatura e umidità possono influire. Le prove dovranno essere quindi eseguite in condizioni costanti laddove possibile, in alcuni casi addirittura in atmosfera protetta.
Sfide pratiche
Una questione fondamentale è che tuttora non vi sono normative uniformi per le prove di adesione sulle batterie. Mentre altri settori come l’industria degli adesivi possono basarsi su normative consolidate, la tecnologia delle batterie spesso è carente di linee guida vincolanti. Produttori diversi utilizzano metodi diversi, rendendo difficile la comparazione.
Vi è anche la necessità di ottimizzare la preparazione dei provini. I dispositivi automatizzati che unificano l’allineamento, ad esempio, aiutano ad aumentare la ripetibilità in questo campo, in particolare per le quantità elevate nella produzione in serie.
Nuove tecnologie, nuovi requisiti
Con i progressi della tecnologia delle batterie, avanzano anche i requisiti della forza di adesione:
- Batterie allo stato solido: Non utilizzano elettroliti liquidi, il che modifica l’equilibrio delle forze nella cella. È necessario un collegamento particolarmente stabile tra gli strati.
- Anodi di silicio: Si possono espandere fino al 300% durante la ricarica, un vero “stress test” per qualsiasi rivestimento. Senza un’adesione sufficiente vi è il rischio di delaminazione e pertanto il malfunzionamento della cella.
Prove di adesione preventive durante la fase di sviluppo consentono l’identificazione di tali problemi e la loro risoluzione prima che si verifichino sul campo.
Il percorso verso le normative e le best practice
Finché non esisteranno delle normative a livello globale, sarà compito dei produttori stabilire normative interne e processi definiti, fra cui
- Preparazione uniforme dei provini
- Utilizzo degli stessi materiali adesivi
- Prove in condizioni ambientali stabili
Allo stesso tempo, molte aziende e produttori di attrezzature di prova stanno collaborando per sviluppare protocolli di prova affidabili, un passo verso la comparabilità e la garanzia di qualità a livello industriale.
In conclusione: Prove piccole, impatto grande
La misurazione della forza di adesione sui rivestimenti degli elettrodi può sembrare un dettaglio minore, ma di fatto ha un forte impatto su sicurezza, efficienza e durata di vita delle batterie moderne.
Con il sempre maggior utilizzo di composizioni chimiche e metodi di costruzione nuovi delle celle, questa prova acquisisce sempre maggiore importanza. I progressi nella tecnologia di prova, dalle prove di trazione in direzione Z all’integrazione di misurazioni meccaniche, termiche ed elettriche, aiutano a fornire un quadro più completo del comportamento degli elettrodi in condizioni reali.
Il messaggio è chiaro: Se avete sotto controllo l’adesione, avete sotto controllo anche la batteria, oggi e in futuro.

SULL’AUTORE:
Business Development Manager per l'industria automobilistica ed elettrotecnica
Aleksander Koprivc ha occupato varie posizioni di management internazionali in ZwickRoell per oltre 20 anni. Dopo aver conseguito una laurea in ingegneria meccanica a Karlsruhe nonché una laurea in ingegneria meccatronica e un MBA in International Management, ha avuto la sua prima esperienza professionale come ingegnere delle applicazioni in Germania e in Francia. Per ZwickRoell, ha svolto la mansione di direttore commerciale in Francia e Spagna, nonché di managing director per entrambe le affiliate. Oggi è business development manager per la divisione elettrotecnica nel settore dell’automotive. In precedenza ha lavorato diversi anni come direttore industriale per il settore dell’automotive.