ISO 179-1 | ISO 179-2 Шарпи, ударная вязкость пластмассовых образцов (в т.ч. с надрезом)
В стандартах ISO 179-1 (неинструментированное испытание на ударную вязкость) и ISO 179-2 (инструментированное испытание на ударную вязкость) приводится описание ударного испытания по Шарпи для определения свойств при ударе (ударной вязкости (в т.ч. образцов с надрезом)) у пластмасс. Описание ударных испытаний по Шарпи приводится также в стандарте ASTM D6110.
Ударные испытания по методу Шарпи предназначены для определения характеристик пластмасс при высоких скоростях деформации. Нагружение прикладывается в виде удара в конструкции для 3-точечного изгиба. В классической процедуре результат отображается как поглощение энергии образцом. Инструментированные методики измерения, кроме того, позволяют строить диаграммы усилия/перемещения, выдают дополнительную информацию о материале, а также автоматически присваивают тип разрушения.
В рамках стандарта для одноточечных характеристик ISO 10350-1 испытание по Шарпи (ISO 179-1) является предпочтительной методикой для измерения ударной вязкости. При этом предпочтительно проводятся испытания образцов без надреза, удар проводится по узкой стороне (1eU). Если образец в такой конфигурации не разрушается, то испытывают образцы с надрезом. При этом результаты испытаний нельзя сравнивать напрямую. Если образец не разрушается даже при наличии надреза, то применяется метод ударного растяжения по ISO 8256.
Цель и области применения Требование к испытанию / оборудованию Видео Испытательные системы Брошюра «Пластмассы»
Цели ударных испытаний по Шарпи
Испытания по Шарпи на ударный изгиб и ударный изгиб образца с надрезом по ISO 179-1 и ISO 179-2 позволяют получать характеристики ударной вязкости при высокой скорости деформации в форме значения энергии в зависимости от площади. Обычно испытания проводят в нормальных климатических условиях или при низких температурах.
Диапазоны применения:
- Сравнение различных формовочных масс
- Составление карт материалов (например, по ISO 10350-1)
- Контроль допусков в рамках контроля поступления товаров и контроля качества
- Испытания готовых изделий посредством извлечения из них образцов
- Измерение эффектов старения
- Исследования механики разрушения
В отличие от Изод, испытание по Шарпи обладает широким диапазоном применения и лучше всего подходит для испытаний материалов, проявляющих междуслойное разрушение среза или поверхностные эффекты.
Кроме того, методика Шарпи предлагает преимущества при проведении низкотемпературных испытаний. Т.к. опоры образца расположены дальше от надреза, предотвращается быстрая передача тепла на критические зоны образца, что упрощает охлаждение во внешнем охладителе и последующую подачу образца в испытательный прибор.
Неинструментированное определение ударной вязкости по Шарпи, ISO 179-1
- Для проведения традиционных неинструментированных испытаний по Шарпи для определения ударной вязкости по ISO 179-1 применяют маятниковые копры, которые подробно описаны в стандарте ISO 13802. Это обеспечивает хорошую сопоставимость испытаний, проводимых на разном оборудовании, в разных лабораториях, разными операторами и в разных городах.
- Принцип измерения базируется на четком определении энергоресурса и высоты сброса молота маятника, который при пробивании образца отдает часть своей кинетической энергии. Вследствие этого молот маятника после удара не может вернуться на исходную высоту сброса. Измеренная разница между высотой сброса и высотой подъема после удара преобразуется в меру поглощенной энергии. Путем определения высоты сброса также определяется скорость удара, так что испытания проводятся при сопоставимых скоростях деформации.
- Каждый маятник разрешено использовать в диапазоне от 10 % до 80 % от своего энергоресурса. Если это условие для испытания одного материала выполняют несколько маятников, что обычно происходит из-за перекрытия рабочих областей различных маятников, то используется маятник с наибольшим энергоресурсом. Это также обеспечивает сведение к минимуму падение скорости в процессе удара.
- Тип измерения подразумевает, что все потери энергии связаны с образцом. По этой причине очень важно свести к минимуму, откорректировать или полностью исключить все внешние источники погрешностей. В стандарте ISO 13802 есть строгие спецификации, а также средства контроля в рамках регулярной калибровки для потерь на трение, которые неизбежно возникают из-за трения о воздух и в опорных точках маятника. Корректировочные значения измеряют и присваивают соответствующему маятнику. Существенным фактором для качества измерения является достаточная масса и виброустойчивая установка маятникового копра на очень прочном лабораторном столе, на прикрученной к стене столешнице или на постаменте из кирпичной кладки. Внутренние вибрации в приборе конструктивно сведены к минимуму. Так, например, на фирме ZwickRoell используются маятники с двойными штангами из однонаправленных углеродных материалов, обладающие небольшой массой и одновременно оптимальной жесткостью.
Инструментированное определение ударной вязкости по Шарпи, ISO 179-2
Благодаря регистрации кривой усилия/времени, можно посредством двойной интеграции при качественно высокоценной измерительной технике получать диаграмму усилия/перемещения с превосходной точностью. Полученные таким образом данные можно использовать по-разному.
- Дополнительные характеристики, позволяющие лучше понять свойства материала
- Характеристики механики разрушения
- Автоматическое, не зависимое от оператора определение типа разрушения на основе прохождения кривой на диаграмме усилия/перемещения
На измеренных кривых всегда показаны характерные колебания. При этом речь идет о колебаниях образца, частота которых находится в определенной функциональной связи с геометрией и размерами образца, а также значением модуля полимера.
Другим большим преимуществом инструментированного испытания по Шарпи на ударную вязкость по ISO 179-2 является большой диапазон измерения. В отличие от традиционных маятниковых копров, измеряется не энергия, а усилие. Т.к. электроника обеспечивает точные измерения уже при 1/100 номинального усилия, то нижний конец измеряемой энергии удара определяется, как правило, по длительности испытания и по собственной частоте измерительных элементов. По этой причине весь указанный в стандарте ISO 179-2 диапазон измерения можно покрыть двумя инструментированными маятниками: инструментированным маятником на 5 Дж для скорости удара 2,9 м/с и маятником на 50 Дж для скорости удара 3,5 м/с. Следуя этой методике, также проводится инструментирование испытаний по Изод и испытаний на ударное растяжение.
Видео: Маятниковые копры для испытаний пластмасс
В качестве особенно точного и одновременно экономичного решения фирма ZwickRoell предлагает маятниковые копры серии «HIT» для испытаний пластмасс. Маятниковые копры предлагаются номиналом от 5 до 50 Джоулей, с их помощью можно нормативно проводить ударные испытания не только по Шарпи согласно стандартам ISO 179-1 / ISO 197-2 и ASTM D6110, но также по Изод, Dynstat и на ударное растяжение согласно ASTM, ISO и DIN.
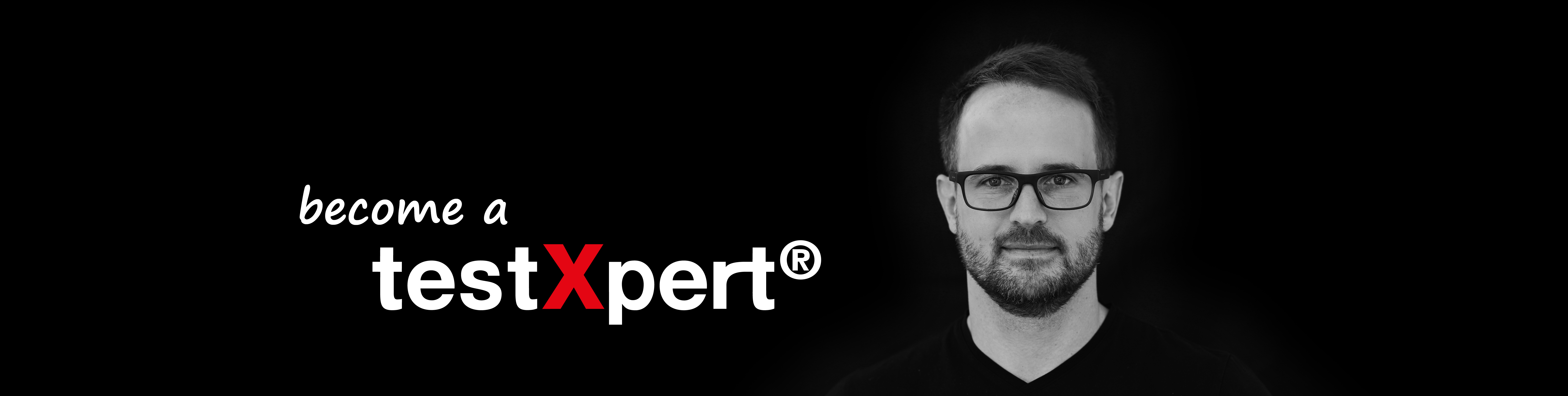
Оптимальная интеграция испытания по ISO 179 благодаря программному обеспечению testXpert
Одно программное обеспечение для всего: испытание на ударную вязкость по ISO 179, испытание на растяжение, испытание на изгиб, испытание на текучесть. И все данные можно анализировать вместе.
- Многочисленные возможности импорта и экспорта обеспечивают идеальную адаптацию ПО testXpert и испытания на ударную вязкость по ISO 179 к Вашим процессам. Программное обеспечение автоматически считывает и вводит данные из других систем (например, из системы ERP или LIM Вашего предприятия).
- Снятие размеров образцов по ISO 179 интегрировано: остаточная ширина, высота и ширина образца одним нажатием на кнопку передаются из измерительного прибора в testXpert.
- Все характеристики, полученные в процессе испытания на ударную вязкость по ISO 179, испытания на растяжение, испытания на текучесть, сохраняются совместно в одном банке данных. Данные легко найти, проанализировать и сравнить - по всем испытаниям. Доступ осуществляется через веб-браузер - откуда хотите.
- Функция Trend Analysis предлагает простую карту контроля качества (SPC) для раннего выявления отклонений от Ваших требований к качеству.

Вас интересуют автоматизированные испытания пластмасс?
Наши роботизированные испытательные системы предназначены для полностью автоматического проведения испытаний образцов на растяжение, сжатие, изгиб или ударных испытаний.
К автоматизированным испытательным системам Связаться сейчас
Автоматизированные испытания образцов с надрезом на ударный изгиб
Автоматизированные испытания пластмассовых образцов с надрезом на ударный изгиб применяются, прежде всего, при увеличенных объемах образцов.
Робот-манипулятор извлекает отдельный образец и укладывает его в термокамеру. После достижения необходимой температуры робот фиксирует образцы с надрезом в маятниковом копре, и проводится автоматизированное испытание на ударный изгиб.
Для соответствия стандартам ISO 180 (Изод), ASTM D256 (Изод) и ISO 179 (Шарпи) доступны три маятниковых копра.