ISO 179-1 ve ISO 179-2 Plastiklerin Charpy darbe ve çentikli darbe dayanımı
ISO 179-1 (enstrümansız darbe testi) ve ISO 179-2 (enstrümanlı darbe testi) standartları, plastiklerin darbe özelliklerini (darbe dayanımı ve çentikli darbe dayanımı) belirlemek için Charpy darbe testini tanımlamaktadır. Charpy darbe testleri ayrıca ASTM D6110'da açıklanmıştır.
Bir plastiği yüksek genleşme oranlarında karakterize etmek için Charpy yöntemini kullanan darbe testleri kullanılır. Gerilme aniden ve 3 noktalı bir bükülme yapısında meydana gelir. Klasik yöntemde sonuç, numunenin enerji alımı olarak sunulur. Ek olarak, aletli ölçüm yöntemleri, kuvvet-yer değiştirme diyagramlarının görüntülenmesini sağlar, ek malzeme bilgisi sağlar ve kırılma tipinin otomatik olarak atanmasını sağlar.
Tek nokta parametreleri standardı çerçevesinde, ISO 10350-1, Charpy, ISO 179-1'e göre darbe dayanımını ölçmek için tercih edilen test yöntemidir. Test, tercihen, dar taraflı darbe (1eU) içindeki çentikli numunelerde test edilir. Numune bu konfigürasyonda kırılmazsa, test çentikli numuneler ile gerçekleştirilir. Test sonuçları doğrudan karşılaştırılabilir değildir. Numune, çentikli numunelerle bile kırılamazsa, ISO 8256 'ya göre çekme darbesi yöntemi kullanılır.
Amaç ve uygulama alanları Test için gereksinimler / Test ekipmanı Video Test sistemi Plastik broşürü
Charpy darbe testinin amacı
ISO 179-1 ve ISO 179-2'ye göre Charpy darbe ve çentik darbe bükme testleri, yüksek uzama oranlarında darbe dayanımı için alanla ilgili bir enerji değeri şeklinde karakteristik değerler sağlar. Testler genellikle normal bir ısı ortamında veya düşük sıcaklıklarda gerçekleştirilir.
Uygulama alanları şunlardır:
- Farklı şekillerin karşılaştırılması
- Örneğin ISO 10350-1’ e göre malzeme kartlarının imalatı
- Gelen mal kontrolü ve kalite güvencesi çerçevesinde tolerans denetimi
- Hazırlanmış test numuneleri bazında bitmiş parçaların test edilmesi
- Eskime etkilerinin ölçümü
- Kırılma mekaniği incelemeleri
Charpy testi, Izod'dan daha geniş bir uygulama alanına sahiptir ve interlaminar kesme kopması veya yüzey efektleri gösteren materyallerin test edilmesi için daha uygundur.
Aletsiz Charpy darbe testi ISO 179-1
- ISO 179-1'e göre geleneksel, aletsiz Charpy darbe dayanımı testi için, ISO 13802'de ayrıntılı olarak belirtilen sarkaç darbe test cihazları kullanılır. Bu, farklı test ekipmanı, laboratuvarlar, operatörler ve konumlar arasında testlerin iyi bir şekilde karşılaştırılabilir olmasını sağlar.
- Ölçüm prensibi, test numunesine çarptığında kinetik enerjisinin bir kısmını serbest bırakan, sabit bir çalışma kapasitesine ve düşme yüksekliğine sahip bir sarkaç çekicine dayanmaktadır. Sonuç olarak, sarkaç çekici, çarpmadan sonra artık orijinal düşme yüksekliğine yükselmez. Düşme yüksekliği ile yükselme yüksekliği arasında ölçülen yükseklik farkı, emilen enerjinin bir ölçüsü olur. Düşme yüksekliğini belirleyerek, darbe hızı da belirlenir, böylece testler karşılaştırılabilir uzama oranlarında gerçekleşir.
- Her bir sarkaç çekiç, iş gücünün %10 ila %80 ’i arasında bir aralıkta kullanılabilir. Bir malzemeyi test etmek için birkaç sarkaç çekici bu koşulu sağlıyorsa, bu genellikle çeşitli sarkaçların çalışma alanlarının örtüşmesinden kaynaklanır, en büyük çalışma kapasitesine sahip sarkaçlı çekici kullanılır. Bu, darbe işlemindeki hız düşüşünün en aza indirilmesini sağlar.
- Ölçüm yöntemi, tüm enerji kayıplarının numuneye atfedilmesi gerektiğini ima eder. Bu nedenle, tüm harici hata kaynaklarını en aza indirmek, düzeltmek veya tamamen hariç tutmak önemlidir. ISO 13802'de, hava sürtünmesi ve sarkaç çekicinin yatak noktalarındaki sürtünme nedeniyle kaçınılmaz olarak ortaya çıkan sürtünme kayıpları için düzenli kalibrasyonun bir parçası olarak kontrollerin yanı sıra katı özellikler vardır. Düzeltme değerleri ölçülür ve ilgili sarkaç çekicine atanır. Sarkaçlı darbe test cihazının çok sağlam bir laboratuvar masasına, sağlam bir duvara vidalanmış bir tezgah üzerine veya bir duvar kaidesi üzerine yeterli kütle ve titreşimsiz kurulumu, ölçümün kalitesi için çok önemlidir. Cihazdaki iç titreşimler yapıcı bir şekilde minimize edilir. ZwickRoell, çok düşük kütleye sahip ve aynı zamanda sarkaç çubuklarına optimum sağlamlık sunan tek yönlü karbon malzemelerden yapılmış çift çubuklu sarkaçlı çekiçler kullanır.
Aletli Charpy Darbe Testi ISO 179-2
Kuvvet zaman eğrisi kaydedildiğinde, yüksek kaliteli ölçüm teknolojisi ile çift entegrasyon ile kuvvet yer değiştirme diyagramı elde edilebilir. Bu şekilde elde edilen veriler farklı şekillerde kullanılabilinir:
- Malzeme davranışını daha iyi anlamak için ek özellikler
- Kopma mekanik özellikleri
- Kuvvet diyagramında eğriye dayalı kopmanın tipinin operatöre bağımlı olmayan otomatik olarak belirlenmesi
Ölçülen değer eğrileri her zaman karakteristik titreşimleri gösterir. Bunlar, frekansı, numune geometrisi, polimerin boyutları ve modülü ile tanımlanmış bir fonksiyonel ilişkide olan numunenin titreşimleridir.
ISO 179-2'ye göre aletli Charpy darbe testinin bir diğer önemli avantajı da geniş ölçüm aralığıdır. Geleneksel sarkaç darbe test cihazının aksine, enerjiden başka bir şey ölçülmez. Ölçüm elektroniği nominal kuvvetin 1/100'ünden kesin ölçümlere izin verdiğinden, ölçülebilir darbe enerjisinin alt ucu genelde test süresine ve ölçüm elemanlarının doğal frekansına göre belirlenir. Bu nedenle, ISO 179-2'de tanımlanan tüm ölçüm aralığını iki sarmal çekiç ile örtmek mümkündür: 2,9 m/s'lik çarpma hızları ve 3,5 m/s darbe hızı için 50 J'lik sarkaç için 5 J'lik sarkaç. Bu prosedürü takiben, İzod yöntemine ve darbe çekme testlerine göre de testler yapılır.
Video: Plastik testler için sarkaç darbe test cihazları
HIT serisi sarkaç darbe test cihazları ile ZwickRoell, plastik testleri için özellikle hassas ve ekonomik bir çözüm sunar. Sarkaç darbe test cihazları 5 ila 50 joule arasında mevcuttur ve sadece ISO 179-1 / ISO 197-2 ve ASTM D6110'a göre standartlaştırılmış Charpy darbe testlerini değil, aynı zamanda ASTM, ISO ve DIN'e göre Izod, Dynstat ve darbe çekme testlerini de sağlar.
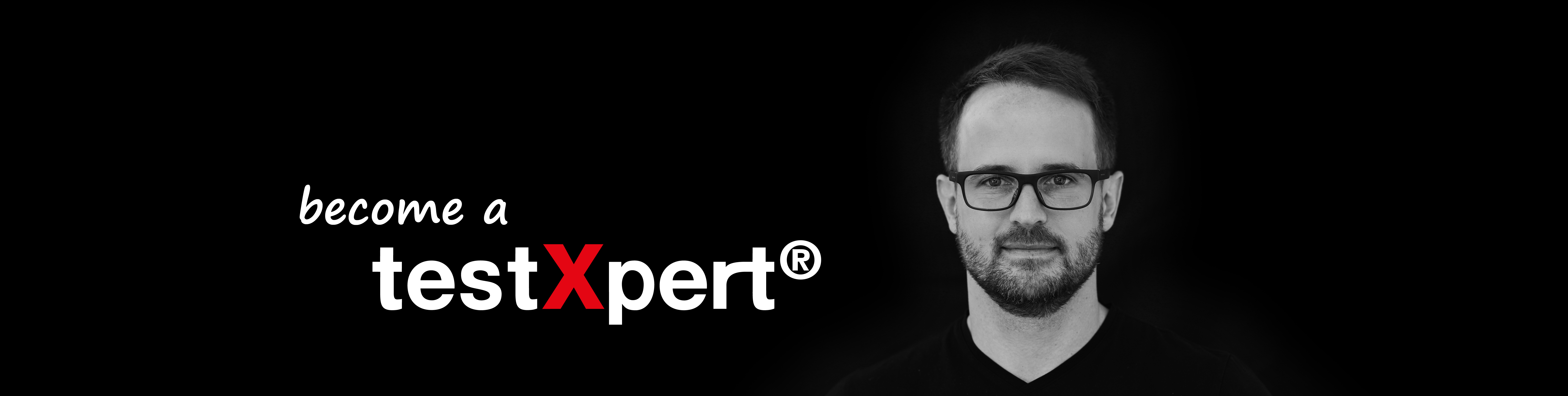
testXpert test yazılımı kullanılarak ISO 179'a göre testlerin optimum entegrasyonu
Her şey için tek bir test yazılımı: ISO 179'a göre darbe dayanımı testi, çekme testi, bükme testi, akış testi. Ve tüm veriler bir arada değerlendirilebilmektedir.
- Çok sayıda içe ve dışa aktarma seçeneği, testXpert ve ISO 179 darbe dayanımı testinin süreçlerinize ideal şekilde entegre edilmesini sağlar. Test yazılımı, diğer sistemlerden, örneğin şirketinizin ERP veya LIM sisteminden verileri otomatik olarak içe ve dışa aktarır.
- Numune boyutlarının ISO 179'a göre ölçümü entegre edilmiştir: Numunenin kalan genişliği, yüksekliği ve genişliği bir düğmeye basılarak ölçüm cihazından testXpert'e aktarılır.
- ISO 179'a göre darbe dayanımı testi, çekme testi, bükme testi ve akma testinden elde edilen tüm karakteristik değerler bir veri tabanına birlikte kaydedilir. Tüm uygulamalarda test verilerini bulmak, değerlendirmek ve karşılaştırmak kolaydır. Web tarayıcısı aracılığıyla istediğiniz yerden erişim kolaydır.
- Eğilim analizi, kalite spesifikasyonlarından sapmaları erken bir aşamada tespit edebilmeniz için basit bir kalite kontrol kartı (SPC) sunar.
Otomatik darbe testleri
Plastikler üzerinde otomatik çentikli çubuk darbe testleriesas olarak daha büyük numune miktarları için kullanılır.
Robot tek bir numune alır ve ısı kabinine yerleştirir. Gerekli sıcaklığa ulaşıldığında, numuneler robot tarafından sarkaç darbe test cihazına sıkıştırılır ve otomatik çentikli çubuk darbe testi gerçekleştirilir.
ISO 180 (Izod), ASTM D256 (Izod) ve ISO 179 (Charpy) standartlarını karşılamak için üç sarkaç darbe test cihazı mevcuttur.