轮胎部件试验
由于轮胎的材料成分复杂,轮胎试验面临着诸多挑战。轮胎包含橡胶化合物(由天然橡胶或合成橡胶、炭黑和各种添加剂制成)和嵌入织物插件(由钢丝或纺织帘线制成的增强材料)。这些材料进行组合后会产生各向异性的行为,尤其是在机械应力作用下。
受不同材料及其相互作用的影响,测试时需要通过特定的试验方法来确定产品性能,例如拉伸强度、分层行为和流变性能。以下试验及其他相关试验都在室温以及常规环境温度下(-70 到 +250 °C)进行:
- 针对不同形状的弹性体试样,按照 ISO 37 和 ASTM D412 标准进行拉伸试验,按照 ISO 34 和 ASTM D624 标准进行撕裂扩展试验
- 对于弹性体进行的硬度、回弹以及磨损试验
- 对于钢帘线以及弹性体制成的编织帘线进行的磨损试验
- 对于钢帘线或编织帘线进行的拉伸试验 - 由于在研发新材料时试样量大,一般采用全自动上样装置
- 测定粘弹性的试验
不同胎压下的汽车轮胎刚度
为确定汽车轮胎刚度,需要测量轮胎在不同胎压下承受垂直和水平载荷时的力值比。
为此,我们将使用一台 50 kN AllroundLine 材料试验机,该试验机配备水平线性装置以及安装在下方底部横梁上的多分量测力平台。testXpert 测试软件中的相应试验程序也支持在不同胎压下对轮胎施加垂直和水平载荷,并评估结果。
轻量化轮毂全表面变形试验
在确定轻量化轮毂的全表面变形时,由电子-机械试验作动缸施加轴向、径向载荷;轮毂的变形行为则由光学 3D 形变测量系统进行测定。测量得到的应变分布结果可以用于确定部件的薄弱点。
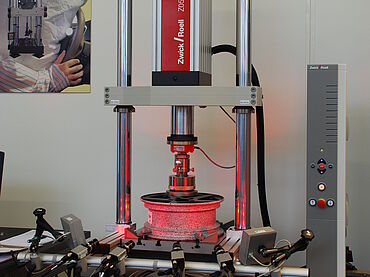
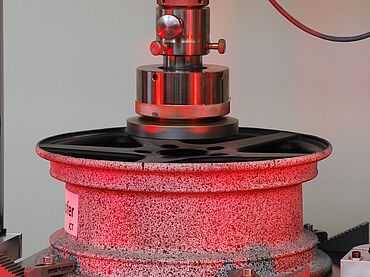
铝制轮毂硬度试验
汽车行驶过程中,轮辋会承受很高的机械和热载荷,这就要求材料具有高强度及出色的抗疲劳性能。合金成分、制造工艺(例如低压铸造、锻造)和热机械后处理都会对铝制轮辋的材料性能造成很大影响。
硬度试验作为一种非破坏性试验方法,可用于进行材料性能表征。该类试验能够确保不同批次和生产批量的材料保持一致的机械性能。实践中主要使用符合 ISO 6506 或 ASTM E10 标准(例如 HBW 2.5/62.5)的布氏硬度试验方法,对于轮辋鞍边、轮辐结构、轮芯或车轮安装法兰等高应力区域的试验而言尤其如此。
符合 ISO 6507 标准的维氏法也可用于检查热处理的均匀性和压痕深度,并确定硬度曲线。根据具体试验环境,用户可以选择在生产监测期间手动进行操作,或使用在线试验系统自动开展试验。
就车轮综合硬度试验而言,ZwickRoell 的万能硬度计 VisionLine 可谓理想之选。
刹车盘试验
刹车盘是车轮上刹车系统最重要的部件之一,为了评估刹车盘的质量,需要对刹车盘摩擦面施加法向压力,并测定其变形量。
ZwickRoell 材料试验机可以安装集成了测量系统的压缩试验工装,用以进行该项试验。试验装置采用三个互成 120° 的测量传感器来测量变形量,并通过压头对试样上圆周形区域施加均匀试验力。该压头为万向压头,能与刹车盘面完全平行贴合,确保施加的压缩载荷均匀一致。试验中,压缩模具对刹车盘中轴及附近区域进行压缩,试验装置对单体和分体刹车盘都能进行试验。
刹车盘硬度试验
底盘系统中的刹车盘对于保证安全性至关重要,在使用过程中需要承受非常高的热载荷与机械载荷。为了确保刹车盘摩擦性能稳定、开裂敏感性低且足够耐磨,批量生产时主要使用铸造合金 (GJL) 或复合材料(例如铸造铝基复合材料或 CMC)。
硬度试验作为一种非破坏性试验方法,可用于检测刹车盘的材料质量:
- ISO 6506 标准所规定的布氏硬度法是铸造刹车盘试验的既定标准程序。试验主要在刹车盘的摩擦环和轮毂区域进行。常规载荷范围为 HBW 2.5/187.5 到 HBW 10/3000,具体取决于材料厚度、材料结构及规格。此外,符合 ISO 6507 标准的维氏法可用于评估层片状珠光体结构,以生成关于刹车盘耐磨性的结论。
- 就高碳铸铁或激光硬化刹车盘等带有涂层或经过热处理的刹车盘而言,符合 ISO 6507 的维氏法也可用于评估层片状珠光体结构,以生成关于材料耐磨性的结论。
- OEM 规范及特定行业标准(例如用于灰铸铁的 SAE J431 标准)或企业内部标准规定了允许的硬度范围和实施方法。批量生产时,试验通常以手动或半自动方式进行,但就产量非常高的情况而言,更多企业开始采用在线数字流程控制系统来开展试验。
就刹车盘综合硬度试验而言,ZwickRoell 的万能硬度计 VisionLine 可谓理想之选。