Stabilité opérationnelle
La stabilité opérationnelle est un terme issu de la science des matériaux et décrit la durée de vie calculée d’un composant. La stabilité opérationnelle décrit la capacité des matériaux et composants à supporter sans dommage des charges statiques, quasi-statiques et dynamiques (récurrentes ou brutales) tout en tenant compte de conditions environnementales pertinentes.
Les méthodes de résistance à la fatigue peuvent être à la fois des méthodes mathématiques et des résultats d’essais. La stabilité opérationnelle relève ainsi de l'interaction de la charge (mécanique et environnementale), du matériau, de la fabrication et de la conception.
Des charges dynamiques sont toujours ou presque à l’origine de la défaillance des composants. La défaillance se produit fréquemment toutefois avec des charges nettement inférieures à la charge de rupture de l'essai de traction statique. Dans le cadre de la stabilité opérationnelle, la résistance à la fatigue décrit la déformation et le comportement de rupture des matériaux sous charge cyclique.
La courbe de Wöhler permet alors de prédire, avec une précision statistique, le nombre de cycles d'oscillation qu'un composant pourra supporter jusqu'à sa défaillance sous charge de fonctionnement.
Stabilité opérationnelle d’un composant Détermination expérimentale Essais de suivi Séquences de charge normalisées Machines d’essais

La stabilité opérationnelle d’un composant
Bien souvent, le département développement ne conçoit pas un composant pour ses caractéristiques de résistance à la fatigue, mais pour sa stabilité (au plan opérationnel).
Afin de déterminer la résistance à la fatigue d'un composant, tous les types de chargement devront être pris en compte, de la contrainte de fluage statique à la sollicitation par choc en passant par la contrainte de vibration à amplitude constante ou variable.Les conditions ambiantes et environnementales telles que la température, les précipitations, la pression, ainsi que les modifications du matériau liées à la corrosion ou vieillissement seront également prises en compte.Le défi consiste alors à déterminer les valeurs caractéristiques au moyen d’essais les plus simples possibles, sur la base desquels le concepteur pourra concevoir un composant sûr et fiable.
Le processus d’endommagement est cependant très complexe et ne peut être décrit par un seul paramètre.La formation de micro-fissures, à partir de défauts internes ou encoches (liés à la construction ou à la fabrication) entraînant des déformations plastiques cycliques, se trouve toujours à l’origine des défaillances.Ce processus est décrit par l’essai LCF.Il s'ensuit alors une croissance des fissures jusqu'à la défaillance, pour laquelle des méthodes de mécanique de la rupture seront utilisées.
L’essai de fatigue (ou essai Wöhler), en revanche, ne fait pas la distinction entre l'amorce de fissure et la croissance de fissure.Grâce aux méthodes d'accumulation des dommages (par exemple Plamgren/Miner), la ligne de Wöhler permet de prédire assez aisément la durée de vie à des amplitudes de charge variables.
Des essais de composants, requérant cependant un effort moindre grâce aux méthodes modernes de caractérisation des matériaux, sont toutefois encore nécessaires en fin de processus.
La stabilité opérationnelle est aujourd'hui testée dans la plupart des domaines de la technologie.Dans le secteur des constructions légères notamment, l’utilisation de la résistance à la fatigue offre cependant des avantages certains.Les composants conçus pour garantir une stabilité opérationnelle nécessitent en effet moins de matériaux et ont une masse moindre.Dans le secteur de l'industrie automobile, par exemple, un véhicule plus léger permet d'économiser du carburant, mais sa structure plus légère permettra également une charge utile plus élevée.Une conception basée sur la résistance à la fatigue remplirait, partiellement seulement, la fonction: des avions conçus pour résister à la fatigue ne pourraient pas voler car ils seraient tout simplement trop lourds.
Le développement d’un composant
Chaque composant ou presque d'une machine, d'une installation ou d'un véhicule est exposé à des contraintes mécaniques variables dans le temps pendant leur fonctionnement.La tâche du développement consiste à fabriquer un produit qui remplit sa fonction pendant toute sa période d’utilisation.Des objectifs de développement court, des exigences de construction légère et des contraintes économiques rendent toutefois cette tâche considérable.L'estimation de la durée de vie dans les essais de fatigue contribue à garantir une conception sûre et économique des composants.La mécanique de la rupture permet également de décrire la propagation des fissures.Les chiffres clés des essais non-destructifs peuvent également être intégrés dans le développement des produits.
Dans un tel contexte, l'objectif d'un composant stable est
- la réalisation de la durée de vie demandée
- la fiabilité des composants d'une construction ou de l'ensemble du système
- la sécurité contre les défaillances avant réalisation la durée de vie nominale (probabilité de défaillance)
la détermination expérimentale de la résistance à la fatigue
La durée de vie d'un composant dépend non seulement du niveau de charge, mais aussi de la séquence de charge. Lorsque le composant conçu offre une conception stable sur le plan opérationnel, les courbes de charge-temps (séquences de charge avec des amplitudes variables) similaires au fonctionnement fournissent ainsi des informations plus fiables sur la durée de vie que les études réalisées avec une charge monotone.
Essais de suivi
Des essais dits de suivi (à l’intérieur desquels un signal de charge-temps enregistré devra être reproduit aussi précisément que possible sur le banc d'essai) sont réalisés dans le cadre de la stabilité opérationnelle. En dépit de régulateurs réglés de manière optimale, le comportement du banc d'essai (et du composant) induit une absence de correspondance entre le signal effectif et le signal prescrit souhaité. Afin d'améliorer le comportement de suivi (correspondance entre le signal prescrit et le signal effectif), le signal prescrit sera modifié dans un processus d'itération jusqu'à ce que le signal effectif corresponde au signal initialement prescrit.
Essais avec séquences de charge standardisées
Des séquences de charge normalisées ont été définies, pour des applications de conception typiques, à partir d'un grand nombre de mesures représentatives des charges opérationnelles; elles servent, au niveau international, de base de conception pour composants soumis aux contraintes dynamiques.
Produits adaptés à la détermination de la stabilité opérationnelle
Pour répondre à ces demandes d’essais les plus diverses, ZwickRoell a beaucoup investi dans le développement de machines d'essais dynamiques et propose un concept d’entraînement adapté à chaque application d’essais:
- Concept modulaire pour basses fréquences jusqu'à 1Hz et 50 kN des servo-vérins électromécaniques
- Machines d'essais électrodynamiques Linear Testing Maschine LTM avec technologie d'entraînement, basée sur un moteur linéaire. L'entraînement, spécialement développé pour la technologie d'essais, est une technologie brevetée par ZwickRoell
- Les machines d’essais à résonance de la série Vibrophore, qui offrent des fréquences d'essai très élevées pour des coûts d'exploitation très faibles. Des fréquences d'essais jusqu’à 285 Hz sont possibles.
- Grande souplesse d'usage des machines d’essais servohydrauliques avec concept de bâti de charge standardisé
Grâce à ce large choix de technologies d'entraînement, ZwickRoell est le seul fabricant de machines d'essais capable de vous conseiller tout en adoptant une position neutre sur le concept d'entraînement. Toutes les machines d'essais utilisent le même logiciel d'essais et la même technologie de régulation. Ceci permet de réduire les coûts de formation dans le laboratoire au quotidien.
Toutes les machines d’essais mentionnées peuvent être utilisées aussi bien comme machine d’essais statique que comme machine d’essais dynamique. Cela est rendu possible par l'utilisation conjointe de l'électronique testControl II et du logiciel d'essai testXpert.
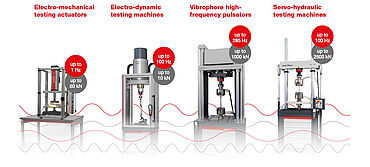