Durabilità
Nell’ingegneria dei materiali la durabilità è la capacità di un componente di mantenere nel tempo (vita di servizio) le sue proprietà. La durabilità descrive la capacità dei materiali e dei componenti di resistere a carichi statici, quasi statici e dinamici (ricorrenti o d'impatto) senza danni, entro la vita di servizio calcolata e tenendo conto delle condizioni ambientali rilevanti.
I metodi per la determinazione della durabilità possono essere sia metodi matematici che risultati di prova. Pertanto, la durabilità è una scienza trasversale che consiste nell'interazione di carico (meccanico e ambientale), materiale, produzione e costruzione.
I carichi dinamici sono sempre, o quasi sempre, la causa del cedimento dei componenti. Spesso si verifica con carichi significativamente al di sotto del carico di rottura osservato nelle prove di trazione statiche. La vita a fatica, nel campo della durabilità, definisce il comportamento di deformazione e cedimento dei materiali sotto sollecitazione ciclica.
La curva S-N può essere utilizzata per prevedere, con precisione statistica, il numero di cicli che un componente sarà in grado di sopportare fino al cedimento sotto carico operativo.

Durabilità di un componente
Molte volte gli ingegneri non progettano un componente per essere resistente alla fatica, ma piuttosto per garantire un'elevata durabilità.
Per la determinazione della durabilità di un componente, si devono considerare tutti i tipi di carico: dal carico di creep statico al carico di impatto, fino al carico ciclico, ad ampiezza costante o variabile. Si tiene conto anche delle condizioni ambientali come la temperatura, le precipitazioni, la pressione, così come le variazioni del materiale dovute alla corrosione o all'invecchiamento. La sfida è quindi quella di individuare i valori caratteristici attraverso le prove più semplici possibili, sulla base delle quali gli ingegneri saranno in grado di progettare un componente sicuro e affidabile.
Tuttavia, il problema in questo caso è che il processo di danneggiamento è molto complesso e non può essere descritto da un singolo parametro. Inizia sempre con la formazione di micro-cricche che si formano a causa di imperfezioni interne o intagli, in corrispondenza dei quali si verificano deformazioni plastiche cicliche. Per descrivere questo processo si eseguono i test LCF. Successivamente, si verifica la crescita della cricca fino a rottura, in questo caso vengono utilizzati i metodi della meccanica della frattura.
La prova di fatica ad alto numero di cicli (anche test S-N), invece, non fa distinzione tra l’innesco della cricca e la crescita della cricca. Utilizzando la curva S-N, è relativamente facile prevedere la vita di servizio ad ampiezze di carico variabili mediante metodi di cumulo del danno (ad esempio Plamgren/Miner).
Tuttavia, sono comunque ancora necessarie le prove sui componenti, che richiedono meno sforzo grazie ai moderni metodi di caratterizzazione dei materiali.
Oggi la durabilità viene testata in quasi tutti i campi tecnologici. I componenti, quando sono progettati per essere durevoli piuttosto che resistenti alla fatica, richiedono meno materiale e quindi hanno una massa inferiore. Nell'industria automobilistica, ad esempio, un veicolo più leggero richiede meno carburante, ma allo stesso tempo la struttura più leggera permette anche una maggiore capacità di carico. La progettazione durevole soddisfa in parte anche un requisito funzionale, si pensi per esempio agli aerei: se fossero progettati per essere resistenti alla fatica non sarebbero in grado di volare semplicemente perché troppo pesanti.
Sviluppo di un componente
Quasi tutti i componenti di macchine, sistemi o veicoli sono esposti, durante il loro funzionamento, a carichi meccanici che causano cambiamenti nel tempo. Il compito dei progettisti è quello di creare un prodotto che svolga la sua funzione per tutta la sua durata di servizio. A ciò si contrappongono spesso tempi di sviluppo molto stretti, richieste di costruzioni leggere e di una produzione a basso costo. L'applicazione della stima della vita di servizio calcolata nelle prove di fatica sostiene la progettazione affidabile ed economica dei componenti. La meccanica della frattura a fatica aiuta anche a descrive crescita delle cricche. I numeri caratteristici dei test non distruttivi possono essere integrati anche nello sviluppo del prodotto.
L'obiettivo di un componente durevole è
- Il raggiungimento della vita di servizio richiesta
- L'affidabilità dei componenti che andranno a costituire una struttura o un intero sistema
- La sicurezza contro i guasti o i tempi di fermo prima di raggiungere la durata di vita nominale (probabilità di guasto).
Determinazione sperimentale della durabilità
La vita di servizio di un componente non dipende solo dal livello del carico, ma anche dalla relativa sequenza. Nel caso di progettazione di componenti durevoli, le sequenze di carico-tempo di simulazione del funzionamento (sequenze di carico con ampiezza variabile) forniscono informazioni più affidabili sulla vita di servizio rispetto alle prove con carico monotono.
Test di simulazione
Per testare la durabilità, vengono eseguite prove di simulazione in cui un segnale di carico temporale registrato deve essere riprodotto il più accuratamente possibile sul banco di prova. Il comportamento del banco di prova e del componente porta ad una mancata corrispondenza tra il segnale effettivo, nonostante un controller impostato in modo ottimale, e il segnale di valore impostato desiderato. Per migliorare il comportamento della simulazione (corrispondenza tra i due segnali), il segnale di valore impostato viene modificato in un processo iterativo fino a quando non coincide con il segnale nominale originale.
Prove con sequenze di carico standardizzate
Per le tipiche applicazioni di progettazione sono state definite sequenze di carico standardizzate, basate su un gran numero di misurazioni rappresentative dei carichi operativi. Sono utilizzate a livello internazionale come base per la progettazione di componenti sottoposti a sollecitazioni dinamiche.
Prodotti correlati alla determinazione della durabilità
Materiali e componenti diversi richiedono l'implementazione di tecnologie di prova diverse. Negli ultimi anni, ZwickRoell ha quindi investito molto nello sviluppo di macchine per prove dinamiche e tecnologie di azionamento, oggi offre il concetto di azionamento giusto per qualsiasi applicazione di prova:
- Gli attuatori elettromeccanici di prova forniscono un concetto modulare per basse frequenze fino a 1Hz e 50 kN
- Le macchine di prova lineari LTM fanno parte di una serie di macchine di prova elettrodinamiche con un azionamento basato sulla tecnologia dei motori lineari. L'azionamento è stato sviluppato appositamente per la tecnologia di prova ed è brevettato da ZwickRoell.
- Le macchine di prova a risonanza della serie Vibrophore gestiscono frequenze di prova molto elevate a costi operativi molto bassi. È possibile raggiungere frequenze di prova fino a 285 Hz.
- Le macchine di prova servoidrauliche con struttura standard offrono la massima flessibilità per qualsiasi applicazione.
Con questa ampia gamma di tecnologie di azionamento, ZwickRoell è l'unico produttore di macchine di prova in grado di fornire una consulenza imparziale sul concetto di azionamento migliore per le tue applicazioni. Tutte le macchine utilizzano lo stesso software di prova e la stessa tecnologia di controllo. Questo riduce al minimo il lavoro di formazione e addestramento per le attività di laboratorio quotidiane.
Le macchine sopra citate possono essere utilizzate sia come macchine per prove statiche che dinamiche, il che è reso possibile dall'uso combinato della nostra elettronica testControl II e del software di prova testXpert.
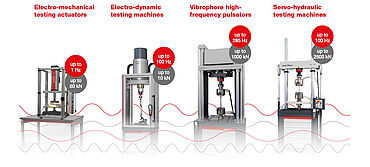