Betriebsfestigkeit
Die Betriebsfestigkeit ist ein Begriff aus der Werkstoffkunde und bezeichnet die rechnerische Lebensdauer eines Bauteils. Die Betriebsfestigkeit beschreibt die Fähigkeit von Materialien und Bauteilen, statische, quasistatische und dynamische (wiederkehrend oder schlagartig) Belastungen im Rahmen der kalkulierten Lebensdauer und unter Berücksichtigung relevanter Umgebungsbedingungen schadensfrei zu ertragen.
Methoden der Betriebsfestigkeit können sowohl rechnerische Methoden als auch Versuchsergebnisse sein. Die Betriebsfestigkeit ist somit eine Querschnittswissenschaft aus dem Zusammenspiel von Belastung (mechanisch und Umwelt), Werkstoff, Fertigung und Konstruktion.
Fast immer sind dynamische Beanspruchungen ursächlich für das Bauteilversagen. Oftmals tritt das Versagen bei Lasten auf, die deutlich unterhalb der Bruchlast aus dem statischen Zugversuch liegen. Die Schwingfestigkeit, als Teil der Betriebsfestigkeit, bezeichnet das Verformungs- und Versagensverhalten von Werkstoffen bei zyklischer Beanspruchung.
Die Zahl der Schwingspiele, die ein Bauteil unter Betriebsbelastung bis zum Ausfall ertragen kann, kann im Rahmen statistischer Genauigkeit mit Hilfe der Wöhlerkurve vorausgesagt werden.
Betriebsfestigkeit eines Bauteils Experimentelle Ermittlung Nachfahrversuche Standardisierte Lastfolgen Prüfmaschinen

Die Betriebsfestigkeit eines Bauteils
Häufig legt die Entwicklung ein Bauteil nicht dauerfest sondern betriebsfest aus.
Für die Ermittlung der Betriebsfestigkeit eines Bauteils müssen alle Belastungsarten berücksichtigt werden, von der statischen Kriechbeanspruchung über schlagartige Belastung bis hin zur schwingenden Beanspruchung unter konstanter oder variabler Amplitude. Auch Umgebungs- und Umweltbedingungen wie Temperatur, Niederschlag, Druck, sowie Veränderung des Materials durch Korrosion oder Alterung fließen in die Betrachtung mit ein. Die Herausforderung ist, mittels möglichst einfacher Versuche Kennwerte zu ermitteln, an Hand derer der Konstrukteur das Bauteil betriebssicher auslegenkann.
Das Problem dabei ist, dass der Prozess der Schädigung sehr komplex ist und eigentlich nicht durch einen einzigen Parameter beschrieben werden kann. Am Anfang steht immer die Mikrorissbildung, ausgehend von inneren Fehlstellen oder Kerben, konstruktiv- oder fertigungsbedingt, an denen es zu zyklischen plastischen Verformungen kommt. Diesen Vorgang versucht man mit dem LCF-Versuch zu beschreiben. Daran schließt sich das Risswachstum an bis hin zum Versagen, für das die Methoden der Bruchmechanik verwendet werden.
Der Dauerschwingversuch (auch Wöhlerversuch) hingegen unterscheidet nicht zwischen Rissinitiierung und Risswachstum. Mit Hilfe der Wöhlerlinie kann relativ einfach mit Methoden der Schadensakkumulation (z.B. Plamgren/Miner) die Lebensdauer bei variablen Belastungsamplituden vorhergesagt werden.
Am Ende steht aber dennoch immer noch der Bauteilversuch zur Verifizierung, allerdings mit wesentlich geringerem Aufwand dank der modernen Verfahren zur Werkstoffcharakterisierung.
Die Betriebsfestigkeit wird heute in fast allen Bereichen der Technik geprüft. Besonders im Leichtbau bietet der Einsatz der Betriebsfestigkeit gewisse Vorteile. Bauteile benötigen weniger Material und haben daher eine geringere Masse wenn sie nicht dauerfest, sondern betriebsfest ausgelegt sind. In der Automobilbranche spart ein leichteres Fahrzeug beispielsweise Treibstoff, aber die leichtere Struktur erlaubt auch eine höhere Nutzlast. Die betriebsfeste Auslegung erfüllt teilweise auch eine Funktion: dauerfest ausgelegte Flugzeuge könnten nicht fliegen, da sie einfach zu schwer wären.
Die Entwicklung eines Bauteils
Fast jedes Bauteil einer Maschine, einer Anlage oder eines Fahrzeuges ist im Betrieb zeitlich veränderlichen mechanischen Beanspruchungen ausgesetzt. Die Aufgabe der Entwicklung ist es, ein Produkt herzustellen, welches seine Funktion über die gesamte Einsatzdauer erfüllt. Dem gegenüber stehen oftmals kurze Entwicklungszeiten, Forderungen nach Leichtbau und wirtschaftliche Fertigung. Die Anwendung der rechnerischen Lebensdauerabschätzung im Ermüdungsversuch hilft der sicheren und wirtschaftlichen Auslegung von Bauteilen. Die Ermüdungsbruchmechanik ermöglicht zusätzlich die Beschreibung des Risswachstums. Auch Kennzahlen der zerstörungsfreien Prüfung können in die Produktentwicklung einfließen.
Das Ziel für ein betriebsfestes Bauteil ist
- das Erreichen der geforderten Lebensdauer
- die Zuverlässigkeit der Komponenten einer Konstruktion bzw. des ganzen Systems
- die Sicherheit vor Ausfall vor Erreichen der Bemessungslebensdauer (Ausfallwahrscheinlichkeit)
Experimentelle Betriebsfestigkeitsermittlung
Die Lebensdauer eines Bauteils ist nicht nur abhängig von der Höhe der Belastung, sondern auch von der Belastungsfolge. Bei einer betriebsfesten Bauteilauslegung liefern betriebsähnliche Belastungs-Zeitverläufe (Belastungsfolgen mit variablen Amplituden) zuverlässiger Aussagen über die Lebensdauer als Untersuchungen mit monotoner Belastung.
Nachfahrversuche
In der Betriebsfestigkeit werden sogenannte Nachfahrversuche durchgeführt, bei denen ein aufgezeichnetes Last-Zeit-Signal möglichst genau am Prüfstand reproduziert werden soll. Das Verhalten von Prüfstand und Bauteil führt dazu, dass das Istsignal, trotz optimal eingestellter Regler, nicht mit dem gewünschten Sollsignal übereinstimmt. Um das Nachfahrverhalten (Übereinstimmung zwischen Soll- und Istsignal) zu verbessern, wird in einem Iterationsprozess das Sollsignal solange verändert, bis das Istsignal mit dem ursprünglichen Sollsignal übereinstimmt.
Versuche mit standardisierten Lastfolgen
Standardisierte Lastfolgen wurden für konstruktionstypische Anwendungsfälle aus einer größeren Zahl repräsentativer Messungen der Betriebsbeanspruchungen abgeleitet und dienen international als Bemessungsgrundlage für dynamisch beanspruchte Bauteile.
Passende Produkte für die Ermittlung der Betriebsfestigkeit
Unterschiedliche Materialien und Bauteile setzen unterschiedliche Prüftechnologien voraus. ZwickRoell hat dazu in den letzten Jahren enorm in die Entwicklung von dynamischen Prüfmaschinen und Antriebstechnologien investiert und bietet für jede Prüfanwendung das passende Antriebskonzept:
- Elektromechanische Servo-Prüfzylinder bieten ein modulares Konzept für niedere Frequenzen bis zu 1Hz und 50 kN
- Die Linear Testing Maschine LTM ist eine elektrodynamische Prüfmaschinenreihe, deren Antrieb auf der Linearmotortechnologie basiert. Der Antrieb wurde dabei speziell für die Prüftechnik entwickelt und ist durch ZwickRoell patentiert
- Die Resonanzprüfmaschinen der Baureihe Vibrophore, die sehr hohe Prüffrequenzen bei sehr niedrigen Betriebskosten bieten. Es sind Prüffrequenzen bis 285 Hz möglich.
- Die servohydraulischen Prüfmaschinen mit einem standardisierten Lastrahmenkonzept bieten die größte Flexibilität für jede Anwendung
Aufgrund dieser Vielfalt an Antriebstechnologien kann ZwickRoell als einziger Prüfmaschinenhersteller neutral vom Antriebskonzept beraten. Bei allen Prüfmaschinen kommt dabei dieselbe Prüfsoftware und Reglertechnologie zum Einsatz. Dies bedeutet einen geringen Schulungsaufwand im Laboralltag.
Dabei können alle oben genannten Prüfmaschinen sowohl als statische als auch als dynamische Prüfmaschine eingesetzt werden. Ermöglicht wird dies durch den gemeinsamen Einsatz der testControl II Elektronik und der bewährten Prüfsoftware testXpert.
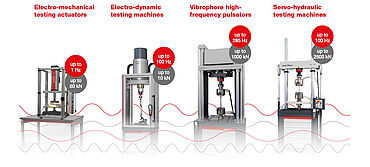