バッテリー試験
輸送部門の電化は、リチウムイオン電池によって大きく左右されます。研究開発と包括的な品質保証は、電池セル部品、電池セル、電池モジュール、および生産用の高電圧ストレージシステム全体のさらなる開発において重要な役割を果たします。使用される材料の特性評価と中間製品特性の生成のための電池試験は、進歩のための重要な前提条件です。
電気自動車の分野での機械試験における長年の経験により、当社は利用可能なすべての電池バリアントに対して、バリューチェーン全体にわたって常に適切な試験方法を提供しています。原材料、セル、セル部品から車両への最終組み立てとリサイクルまで、ツビックローエルは包括的な電池試験の経験豊富なパートナーです。顧客プロジェクト例
当社は、業界の大手企業、科学機関、研究機関と緊密に協力し、f電池固有の幅広い機械試験方法を提供しています...
引張試験 疲労試験 曲げ試験 圧縮試験 剥離/接着/摩擦試験 固体電池 バッテリー試験室での相談と事前テスト ダウンロード
...機能および構造のテスト方法も同様です。
バッテリーがどのように製造されているのでしょうか?どのような場合、機械的なバッテリー試験が重要なのでしょうか?
- リチウムイオン電池の価値連鎖は、リチウム、コバルト、ニッケル、アルミニウムなどの原材料の採掘から始まります。
- 原材料が加工された後、陽極、陰極、電解質を含むセルのコンポーネントが複雑なプロセスを経て製造されます。このセルコンポーネントの製造プロセスでは、品質と信頼性を確保するために試験が重要であり、一方で中間製品の特性を特徴づけることにより、多物理量シミュレーション用の貴重なデータを生成します。
- 次に、バッテリーセルが生産され、高電圧蓄電ユニットに組み立てられます。ここでも、機械的なバッテリー試験は機能性と安全性を確保するために重要な役割を果たします。データは、バッテリーセルやモジュールが日常的に使用される際の挙動を評価するために収集されます。
バッテリーフォイルおよびコーティングされた電極の引張試験
バッテリーフォイルおよびコーティングされた電極の引張試験は、機械的な強度と延性を決定します。
バッテリーフォイルの試験は、応用範囲に応じて薄膜厚さが <10 µm の場合、特に試験技術に高い要求をもたらします。堅牢で繰り返し可能かつ再現性があり、したがって信頼性の高い試験結果を確保するには、正確な試験片の取り扱いと信頼性の高い試験片のグリップが必要です。引張り試験における材料特性の正確な決定には、次の要素が重要です:
動画:バッテリーフォイルの引張試験 DIN 50154 / ASTM E345
薄膜バッテリー箔やフィルム(アルミニウム箔、銅箔、ポリマーセパレータ)の引張試験に関するDIN 50154やASTM E345などの規格を、ツビックローエルのtestXpert試験ソフトウェアがサポートし、規格に準拠した性能を保証します。
特にバッテリー材料に関する規格の更なる発展への積極的な関与により、ツビックローエルの試験方法が将来のすべての要件を満たし続けることが保証されます。
リチウム金属箔の引張試験
リチウム金属箔の引張強度は、不活性環境でのみ測定できるため、特定の課題が発生します。ツビックローエルでは、これに特化した特別な保護ガスチャンバーであるグローブボックスや試験片の準備および操作オプションを提供しています。これらにより、制御された条件下での正確な試験が可能となり、精密な結果が得られます。
セパレータ箔の引張試験
セパレータ箔は、アノードとカソードを電気的に絶縁し、同時にリチウムイオンの流れを可能にすることで、バッテリーセルで重要な役割を果たします。バッテリーセルの効率、耐用年数、安全性は、これらのセパレータの機能に大きく依存します。試験に関しては、セパレータの主な要件は、ISO 527-3 および ASTM D882 に準拠した引張テスト、および EN 14477、ASTM D5748、ASTM F1306 に準拠した穿刺試験によってカバーされます。これらのテストは、現実的な機械的特性を実現するために、電解質で湿潤した状態でも実行されます。
関連するもう 1 つの側面は、電極コーティングとセパレータ間の摩擦係数に関連するセパレータの挙動です。これらの特性値は、巻き取りプロセスでの製造パラメータの設定に特に重要です。ツビックローエルでは、常温で試験を実行するだけでなく、ツビックローエルの恒温槽を追加すると、-20℃から +50℃の範囲の動作温度でもテストを実行できます。これにより、さまざまな条件下でのセパレータ フォイルの包括的な特性評価が保証されます。
バッテリーフォイルの疲労試験
リチウムイオン電池における銅やアルミニウム製のバッテリー箔は、電流集電体としての役割を果たし、製造プロセスやバッテリーの運用中にさまざまな応力にさらされます。
- 製造プロセス中には、欠陥や均一でない分布などのコーティング欠陥が発生する可能性があります。カレンダリングプロセスによってこれらの欠陥を軽減することができますが、完全に除去することはできません。
- バッテリーの運用中、箔は熱的および機械的な負荷にさらされ、疲労の兆候が現れることがあります。さらに、電解液との化学反応により腐食が発生し、バッテリーの性能が低下する可能性があります。
特定の負荷と疲労現象は、バッテリーの設計や運用条件を含む多くの要因に依存することに注意することが重要です。したがって、バッテリーの開発と最適化には、常にバッテリー箔やフィルムのを通じた徹底した試験と特性評価が必要です。
LTM電気式動的試験機の低負荷力を利用することで、感度の高い試料でも疲労試験を問題なく実施することができます。LTMはオイルフリー駆動技術を搭載しています。直線モーターは非常に静かで、ラボでの使用に完璧に適しています。
バッテリー箔がナイフエッジによって損傷されないようにするために、延性の変化を光学的なビデオ伸び計である動的ビデオ伸び計で測定します。
電極コーティングの曲げ試験
電極の活性材料コーティングの曲げ強度を測定する曲げ試験は、リチウムイオンバッテリーの寿命に極めて重要です。
電極の活物質は厚さ 50 ~ 100 μm のコーティングで構成されており、その機械的特性は化学組成や製造プロセスによって大きく異なります。この知識は、スループット速度、ローラー角度、予負荷力などの生産パラメーターの最適な設定を定義するために重要です。2点曲げ試験治具を使用して曲げ強度を測定すると、コーティングが損傷せず、避雷箔と活物質間の接触が維持される最大許容曲げ角度と曲げ半径を決定できます。ここでは、2点曲げ試験治具と統合された高分解能ロードセルを備えたzwickiLine試験機が完璧なソリューションであることが証明されています。
バッテリーフォイル、活物質およびコーティングされた電極の圧縮試験
電極層とセパレータ層を積層する際の圧力は、セル内で効果的に接触するために重要です。この圧力は、セルの耐用年数と性能に大きな影響を与えます。
ツビックローエルは、これらの動的負荷条件を正確にシミュレートして特性評価するために、バッテリーフォイル、活物質、およびコーティングされた電極に対するさまざまなタイプの圧縮試験を提供しています。
- カレンダー加工プロセスは、リチウムイオン電池の電極の製造において重要な役割を果たします。活物質、バインダー、導電性添加剤のペーストを金属箔 (アノードには銅、カソードにはアルミニウム) に塗布します。コーティングされたフィルムは、圧力と温度条件下で作動するローラーによって薄く均一な層に押し付けられます。
- 電動車両の航続距離に大きな影響を与えるリチウムイオン電池セルのエネルギー密度は、プロセスのこのステップに大きく依存します。プロセス変数の変化により、システムおよび材料パラメータの最適化が可能になります。
- 圧縮変形測定は、電極の品質と一貫性を監視および制御するのに役立つため、非常に重要です。これらの測定により、活物質が電極にどの程度うまく埋め込まれているか、および電池の動作中に剥離が発生する可能性があるかどうかに関する情報が得られます。また、最大のエネルギー密度とバッテリー性能を達成するために、カレンダー加工プロセスに最適な圧力と温度を決定するのにも役立ちます。
被覆電極とプロトタイプのセルスタック(ゼリーロール)の多機能解析
コーティングされた電極やプロトタイプのセルスタックを試験する場合、長期にわたる効率、性能、耐用年数を確保するには、材料とコンポーネントの特性評価が重要です。これらの特性値は、研究開発および品質保証の目的にとって非常に重要です。
そこで、ツビックローエルは多機能細胞成分分析装置 (MCCA) を開発しました。3台の高精度直線変位計とレベリング装置の採用により、電極面に正確な圧力を加えることができます。これにより、現実的な圧力条件下での電極の厚さの変化の測定が可能になります。同時に、金メッキの圧縮プラテンを介して電気抵抗が測定されるため、圧力に応じて評価を行うことができます。
充電および放電のプロセス中に、セルは膨張および収縮します。これはバッテリー膨張として知られています。これにより、個々のコンポーネントにかかる圧力が変化します。MCCA試験治具を使用すると、たとえば、コイン電池などのプロトタイプの一次電池に対して高精度の電池膨張試験を実行でき、ゼリーロール内の最小の繰り返しセルコンポーネントスタックの充電および放電サイクルにおける動作を正確に特徴付けるのに役立ちます。
多機能細胞成分分析装置の利点:
- 圧力下での被覆電極の応力-ひずみ挙動の高精度測定
- 圧力の関数としての電気抵抗の測定
- プロトタイプの一次電池(コイン電池)の電池膨張挙動の測定
電極塗布工程での高精度圧縮試験
電池製造の最大のチャレンジは電極のコーティングプロセスにあります。バッテリーの安全な動作のための重要な基準が確保されています。優れた機械的安定性、優れた電気伝導性、および活性物質の予測可能な経年変化挙動です。電極のコーティング技術は継続的に改善されており、ドライコーティングの有望な開発により、非常に高い省エネの可能性に加えて、同等またはより優れた機能的な電極特性が確保されるはずです。
- したがって、圧縮時のバッテリー箔とコーティング電極の挙動を詳細に分析することが重要です。計装された圧縮率測定ヘッドは、正確な力-変位曲線を生成します。この曲線は、極薄層の圧縮試験における弾性変形挙動の判定に使用できます。このプロセスは、材料開発、品質保証、バッテリーシミュレーションに不可欠なデータを提供します。
- 活物質と電極基板間の確実な接続は、バッテリーセルの品質と性能にとって重要です。活物質の最適な機械的安定性を確保するには、さまざまな動作圧力下でその多孔性と導電性を維持する必要があります。
Z方向接着試験
Z方向の接着試験は、接着強度を決定し、破損の種類を評価するための、より信頼性が高く再現性のある方法です。引張結合Z方向固定具では5つの試験片を同時に準備できます。また、試験機は、接触圧力と持続時間の定義されたパラメーターを各試験片に対して同じように自動的に実行します。この試験治具は、剥離試験と比較して、測定結果に対するオペレータの影響を軽減するのに役立ちます。
次に、個々の試験片をZ方向に引き剥がし、明確な最大接着強度値を決定します。効率的な試験片準備と高精度な繰返し性に加え、この試験法では破断パターンの凝集および接着コンポーネントも決定する事ができます。この試験手順で得られた結果は比較しやすいため、製造プロセスにおけるコーティング品質の信頼性の高い監視も可能になります。
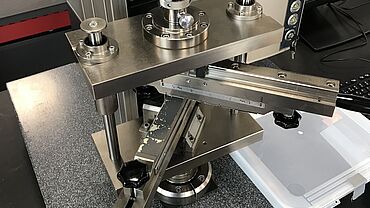
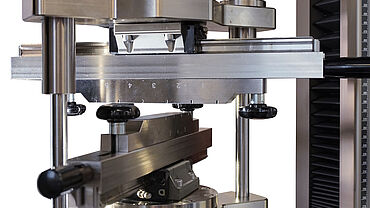
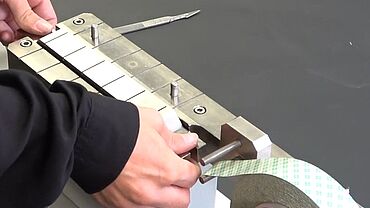
電極コーティング、アレスタ箔、セパレータの摩擦試験
リチウムイオン電池の製造における電極コーティング、避雷箔、セパレータの摩擦係数の測定は、製造プロセス中に問題を特定し、電池の品質と性能を確保する上で非常に重要です。
考えられる摩擦試験には次のものがあります:
- コーティング接着試験: バッテリーセル内の異なる層間の結合が試験されます。指定した力または荷重を適用すると、層が分離するか結合する傾向を評価できます。結果として生じる層分離力は、摩擦係数についての結論を引き出すのに役立ちます。
- 接触力と変位試験: これらの試験では、さまざまなコーティングや表面を持つ材料を移動または分離するのに必要な力を測定します。これにより、圧力下での材料の挙動を理解し、摩擦係数を定量化することができます。
全固体電池コンポーネントの特性評価
全固体電池で液体電解質が不要になると、境界層の接触、熱膨張、耐老化性などの新たな課題が生じます。ツビックローエルは、固体電池コンポーネントの特性評価のために、固体電池の特殊な要件に対応する幅広い試験方法のソリューションを提供しています。
- リチウム金属アノードの機械的特性評価は困難な場合があります。劣化が激しいため、試験片の作成と引張強さの測定は不活性ガス環境で行う必要があります。さらに、繊細で延性のある材料は、特別な試験片クランプでの非常に慎重な取り扱いと、光学式伸び計を使用した軸方向のひずみの信頼性の高い測定を必要とします。ツビックローエルは、 特別な保護ガス室 (グローブ ボックス)、試験片の準備と操作のオプション、試験片の非接触測定に適応した光学伸び計を提供しています。
- もう1つの課題は、複合カソードや固体電解質セパレーターなどの他のコンポーネントの機械的特性を決定することです。これらのコンポーネントの強みは、生産プロセスの設計と信頼性の高いバッテリー機能に大きな影響を与えます。 ZHNナノインデンターを使用すると、ヤング率、硬度、曲げ強度、破壊靱性を調査するために、さまざまな機械的特性を持つポリマー、酸化物、または硫化物で作られた固体電解質の特性を評価できます。
バッテリー膨張試験:充電および放電サイクルにおけるセルの動作の特性評価
充放電プロセス中のバッテリーセルの動作、特にバッテリー膨張またはバッテリー呼吸と呼ばれるセルの膨張は、性能と耐用年数に影響を与えます。この現象は、全固体電池だけでなく、角形セルやパウチセルでも特に顕著です。しかし、新しい世代の電池の開発においては、円筒形電池の膨張を理解することもますます重要になってきています。
同時焼き戻し時のこの挙動を正確に特徴付けることが重要です。モジュール内のセルの膨張によりセルにかかる圧力が変化するため、モジュール内での組み立てではセルの呼吸を考慮する必要があります。この圧力と温度は、セルの耐用年数と性能に大きな影響を与えます。したがって、細胞の呼吸と膨張を正確に特徴付けることが非常に重要です。ツビックローエルは、電気サイクル化、高精度変形測定、長期試験手順、温度制御など、充放電サイクルにおける電池の挙動を特性評価するためのさまざまなアプローチを提供しています。
- バッテリーセル全体の温度制御
バッテリーセルは恒温槽を使用して所望の動作温度まで加熱され、試験中はチャンバー内で温度が一定に保たれます。制御は恒温槽内の周囲温度に基づいて行われます。リスクに応じて、適切な危険レベルを備えた恒温槽またはプロアクティブチャンバーを介して試験中の安全が確保されます。 - バッテリーセル全体の正確かつ均一な温度制御
圧縮プレートを積極的に加熱および冷却することにより、バッテリーセルの表面温度が均一に調整され、上下から正確に制御されます。一方、バッテリーセル内の局所的な温度変動も補償できます。したがって、たとえば、高い放電電流での臨界温度が回避され、信頼性の高い試験が保証されます。
このタイプの試験はMBTSと共同で開発されました。記事では、自動車用途向けの標準化されたリチウムイオン電池セルの電気特性に対するさまざまな温度、圧力、放電速度の影響を調査しました。
記事へのリンク
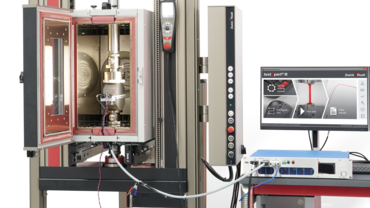
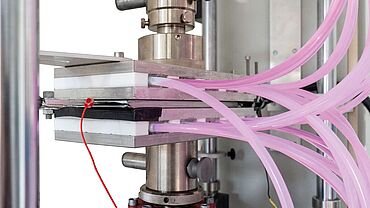
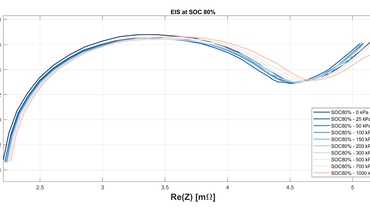
バッテリーの圧壊試験
バッテリーの圧壊試験は、リチウムイオンバッテリーの破壊信頼性試験です。これらの試験は、市場へのリリースと自動車用途でのバッテリーの使用に必要です。試験中、バッテリーは安全性と信頼性を確保するために極端な条件にさらされます。熱試験と電気試験に加えて、一般的な圧壊試験には機械的試験も含まれます。
機械的試験中、バッテリーは物体が貫通するか機械的負荷が加えられることで物理的にストレスを受け、バッテリーの完全性が試験されます。たとえば、内部短絡を引き起こす釘刺し(釘打ち)や潰れが、バッテリーの機能や安全関連の動作にどのような影響を与えるかを調査することが含まれます。
これらのバッテリーの圧壊試験は、通常、熱暴走につながり、火災や爆発につながる可能性があります。環境規制と労働安全意識により、再現可能な環境条件を確保するために、これらの試験は、オープンな環境や排気ガス処理のない古い建物では実行してはなりません。
ツビックローエルの万能試験機 AllroundLine Z100 と Weiss Technik の極限環境シミュレーション システムを使用すると、最大 100 kN の力でバッテリー試験を実行できます。機械的なモジュール性により、試験治具を簡単かつ安全に交換でき、1 台のマシンでさまざまな機械的圧壊試験を安全に実行できます。試験結果は、testXpert試験ソフトウェアで評価されます。
エクストリームイベントチャンバーを使用したバッテリー圧壊試験の詳細
異なるタイプのバッテリーセルには、さまざまな特性を持つ多様な種類があります。最もよく知られているのは、リチウムイオン電池です。これらは多くの電子機器や電気自動車(EVバッテリー、電気自動車バッテリー)で使用されています。また、常に進化しているさまざまなセル化学式も存在します。セルの化学式により異質なバッテリー特性が生じるため、精密な特性評価が機械的にも重要です。円筒型、角柱型、袋状セルなどのセル形式は、エネルギー密度、スペース要件、性能などにおいてさまざまな利点と欠点を提供します。したがって、適切なバッテリータイプとセル形式の選択は、常にそれぞれのアプリケーションの特定の要件に依存します。要するに、バッテリーの開発と生産にはさまざまなアプローチがあります。そのため、幅広い試験方法の提供も必要です。