Battery testing
The electrification of the transport sector is significantly influenced by lithium-ion batteries. Research and development, along with comprehensive quality assurance, play a key role in the further development of battery cell components, battery cells and battery modules as well as entire high-voltage storage systems for production. Battery testing to characterize the materials used and the generation of intermediate product characteristics are crucial prerequisites for progress.
With our many years of experience in mechanical testing in the field of electromobility, we always offer the right test method along the entire value chain for all available battery variants. From raw materials, cells and cell components to final assembly in the vehicle and recycling—ZwickRoell is your experienced partner for comprehensive battery testing.Interesting customer projects
In close collaboration with leading companies in the industry, scientific institutions and research institutes, we offer a wide range of battery-specific mechanical testing methods...
Tensile tests Fatigue tests Flexure tests Compression tests Peel/adhesion/friction tests Solid-state batteries Consultation and pretests in the battery testing lab Downloads
...as well as function and structural test methods.
How batteries are manufactured? In what instances is mechanical battery testing important?
- The lithium-ion battery value chain begins with the mining of raw materials such as lithium, cobalt, nickel and aluminum.
- After the raw materials have been processed, the cell components, including the anode, cathode and electrolyte, are manufactured via a complex process. In this process, that is cell component manufacturing, tests are important to ensure quality and reliability on the one hand and to generate valuable data for multi-physical simulations by characterizing the intermediate product features on the other.
- The battery cells are then produced and assembled into high-voltage storage units. Mechanical battery testing also plays a decisive role here, as it ensures the functionality and safety of the battery. Data is collected in order to assess the behavior of the battery cells and modules as they are put to daily use.
Mechanical battery testing: foil, electrodes, separators and cell housing
Mechanical battery testing of foils, electrodes, separators and cell housing plays a decisive role not only in guaranteeing and further developing quality and performance, but also in ensuring trouble-free production. Tensile, compression, flexure, fatigue and adhesion tests support the realistic characterization of these battery components. Furthermore, the obtained data serves as the basis for multiphysics simulations. These are used to numerically predict the behavior of the battery, for example in the event of a crash.
Tensile tests on battery foil and coated electrodes
Tensile tests on battery foil and coated electrodes determine the mechanical strength and elongation.
Testing of battery foil puts high demands on the testing technology, especially with low film thicknesses of < 10 µm, depending on the area of application. Ensuring robust, repeatable, reproducible and therefore reliable test results requires precise specimen handling and reliable specimen gripping. A critical role in the precise determination of material properties in the tensile test is therefore played by:
- The vertical alignment of the specimen
- Gentle gripping techniques and
- Non-contact determination of the extension through optical extensometers such as the videoXtens extensometer
Video: Tensile Test on Battery Foil to DIN 50154 / ASTM E345
Standards such as DIN 50154 and ASTM E345 for tensile tests on thin battery foil and film (aluminum and copper foil, polymer separators) can be taken into account in the test sequences, supported by ZwickRoell’s testXpert testing software, which guarantees standard-compliant performance.
Active involvement in the further development of standards, especially for battery materials, ensures that ZwickRoell test methods will continue to meet all future requirements.
Tensile test on lithium metal foil
Particular challenges arise when testing lithium metal foil, as their tensile strength can only be determined in an inert environment. ZwickRoell offers special protective gas chambers, referred to as glove boxes, and specimen preparation and manipulation options for this purpose. These enable precise testing under controlled conditions for accurate results.
Tensile test on separator foil
Separator films in a lithium-ion battery separate the anode and cathode from each other to prevent electrical short circuits. At the same time, the separator allows the flow of ionized charge carriers that are needed to close the circuit in an electrochemical cell. The efficiency, service life and safety of battery cells depend to a large extent on the function of these separators. In terms of testing, the main requirements for separators are covered by tensile tests according to ISO 527-3 and ASTM D882 as well as puncture tests according to EN 14477, ASTM D5748 and ASTM F1306. These tests are also carried out in an electrolyte-wetted state in order to achieve realistic mechanical characteristics.
An additional relevant aspect is the behavior of the separator in relation to the coefficient of friction between electrode coating and separator. These characteristic values are particularly important for setting the production parameters in the winding processes. ZwickRoell enables you to not only run tests at ambient temperature, but also at operating temperatures in a range of -20 °C to +50 °C when adding a ZwickRoell temperature chamber. This ensures comprehensive characterization of the separator film under different conditions.
Video: Tensile test on separator foil
In addition to ceramic separators and glass fiber nonwovens, polymer membranes are primarily used. Reliable determination of the tensile strength and strain at break provides information about the integrity of the separator film under operational mechanical stress.
While thicker separator film efficiently and safely prevents contact between the anode and cathode, thinner film makes it possible to reduce the weight of the battery and improve the energy density. Tensile tests on separator film are performed according to standardized methods ASTM D882 and ISO 527-3.

Our robotic testing system roboTest F, which was specially designed for tests on non-rigid specimens, is available for automated tensile tests on battery foil and film as well as coated electrodes.
Would you like to learn more about our automation options for battery foil and film testing?
We will be happy to discuss your needs.
Fatigue tests on battery foil
Battery foils made of copper and aluminum act as current collectors in lithium-ion batteries and are exposed to various stresses both during the production process and during battery operation.
- Coating defects such as flaws or uneven distribution can occur during the production process. Although the calendering process can mitigate such defects, they cannot be completely eliminated.
- In battery operation, the foil is subject to thermal and mechanical loads, which can lead to signs of fatigue. In addition, chemical reactions with electrolytes can cause corrosion, which impairs battery performance.
It is imperative to note that specific loads and fatigue phenomena depend on many factors, including battery design and operating conditions. Therefore, battery development and optimization always requires thorough testing and characterization of battery foils and films through fatigue testing.
With the LTM electrodynamic testing machine’s low test forces, fatigue tests can be run on sensitive specimens without problems. The LTM is equipped with oil-free drive technology. The linear motor is extremely quiet and perfectly suited for use in the laboratory.
So that the battery foil is not damaged by the knife edges, the change in elongation is measured with an optical video extensometer, the videoXtens dynamic.
Flexure tests on electrode coatings
Flexure testing for determination of the flexural strength of the active material coating is extremely important for the service life of lithium-ion batteries.
The active material of the electrodes consists of a 50-100 µm thick coating, of which the mechanical properties can vary greatly due to the chemical composition and the production process. This knowledge is important for defining optimal settings of production parameters such as throughput speed, roller angles, and pre-load forces. Determining the flexural strength using a 2-point flexure test kit enables the determination of the maximum permissible bending angle and bending radius at which the coating remains intact and the contact between the arrester foil and the active material is maintained. Here the zwickiLine testing machine with 2-point flexure test kit and integrated high-resolution load cell proves to be the perfect solution.
Compression test for battery foil, active materials and coated electrodes
The pressure with which the electrode and separator layers are stacked is crucial for effective contact within the cell. This pressure significantly influences the service life and performance of the cell.
ZwickRoell offers various types of compression tests for battery foil, active material and coated electrodes to precisely simulate and characterize these dynamic loading conditions.
- The calendering process plays a key role in the manufacturing of electrodes for lithium-ion batteries. A paste of active material, binder and conductive additive is applied to a metal foil (copper for the anode, aluminum for the cathode). The coated film is pressed into a thin, even layer by rollers that work under pressure and temperature conditions.
- The energy density of lithium-ion battery cells, which significantly influences the range of electrically powered vehicles, depends largely on this step in the process. The variation of process variables enables the optimization of system and material parameters.
- Compression deformation measurements are highly relevant, since they help monitor and control the quality and consistency of the electrodes. These measurements provide information on how well the active material is embedded in the electrode and whether detachment could occur during battery operation. They also help to determine the optimum pressure and temperature for the calendering process in order to achieve maximum energy density and battery performance.
Multifunctional analysis of coated electrodes and prototypical cell stacks (jelly rolls)
When testing coated electrodes and prototypical cell stacks, characterization of the materials and components is important to ensure their efficiency, performance and service life for the long term. These characteristic values are of critical importance for research and development as well as quality assurance purposes.
ZwickRoell has therefore developed the Multifunctional Cell Component Analyzer (MCCA). With the use of three high-precision linear displacement transducers and a leveling device, pressure can be applied precisely to a surface of the electrode. This enables measurement of the change in thickness of the electrode under realistic compressive conditions. At the same time, the electrical resistance is measured via gold-plated compression platens, which allows an evaluation to be carried out dependent on the pressure.
During the electrical charging and discharging process, the cell swells and shrinks, known as battery swelling. This leads to changes in pressure on the individual components. The MCCA test fixture allows you to run highly precise battery swelling tests on prototypical primary cells such as coin cells, for example, and helps to accurately characterize the behavior in the charging and discharging cycle of the smallest repeating cell component stack in the jelly roll.
Benefits of the Multifunctional Cell Component Analyzer:
- High-precision measurement of the stress-strain behavior of coated electrodes under pressure
- Measurement of the electrical resistance as a function of pressure
- Measurement of the battery swelling behavior of prototypical primary cells (coin cells)
High-precision compression tests in the electrode coating process
A major challenge in battery production is the coating process of the electrodes. Important criteria for safe battery operation are ensured: outstanding mechanical stability, excellent electrical conductivity and predictable aging behavior of the active material. Coating technologies for electrodes are continuously being improved and the promising development of dry coating must ensure similar or better functional electrode properties in addition to the very high energy-saving potential.
- Therefore, it is important to run a detailed analysis of the behavior of battery foil and coated electrodes under compression. The instrumented compressibility measuring head generates precise force-displacement curves, which can be used to determine the elastic deformation behavior in compression tests for extremely thin layers. This process provides essential data for material development, quality assurance and battery simulation.
- The secure connection between the active material and the electrode substrate is crucial for the quality and performance of a battery cell. To ensure optimum mechanical stability of the active material, its porosity and conductivity must be maintained under varying operating pressure.
Determination of the setting behavior of separator foil
The materials used for separator foil can exhibit setting behavior under cyclic pressure loads. This setting behavior, which leads to a change in the foil thickness, sometimes impairs the performance and service life of the battery. With universal tensile-compression machines, and special test stands for compression tests, MCCA and nanoindenter, ZwickRoell supports a wide range of test methods for the characterization of the setting behavior of separator foil.
Peel and adhesion tests for batteries
In addition to the mechanical characteristic values, the bond strength of the single- or double-sided coatings on the arrester foil is of great importance, since this connection is significant for internal conductivity of the battery. Since the bond strength can also change as the battery ages, it is important to ensure that the connection is guaranteed for the long term. This can be achieved through the implementation of peel and adhesion tests. Detachment of the active material, carried in the electrolyte significantly impairs cell safety. Therefore, testing the adhesion strength of the electrode coating on both the anode and cathode is important for production monitoring directly at the cell production line.
The mechanical bond strength between active material and substrate can be determined in different ways:
90° and 180° peel tests
The most common method used to determine the mechanical bond strength between the active material and substrate is the peel test with a peel angle of 90° or 180°.
- For both variations, the coated film is applied to a carrier material (substrate) and is then pulled off by the testing machine at the specified peel angle.
- The methods are not standardized and are therefore very difficult to compare.
- The important qualitative assessment of the type of failure (cohesion or adhesion failure) is only possible to a limited extent with this method.
- Other disadvantages of this test are the large quantity of material use and time-consuming specimen preparation.
Video: Peel, Puncture and Flexure Test on Battery Film
- 90° / 180° peel tests for determination of the mechanical adhesive strength between active material and substrate for QA as well as R&D.
- Puncture tests on separator film to determine the puncture resistance in order to avoid safety issues, as the film must withstand a defined resistance to mechanical influences.
- 2-point flexure tests to characterize the flexural strength of various materials in order to detect deviations from specified parameters that can lead to production breaks and safety issues.
Z-direction adhesion test
The Z-direction adhesion test is a more reliable and reproducible way of determining the bond strength and assessing the type of failure. Five specimens can be prepared simultaneously in the tensile bond Z-direction fixture. The testing machine also automatically performs the defined parameters of contact pressure and duration identically for each specimen. This test fixture helps reduce operator influence on the measurement result when compared to peel tests.
Each individual specimen is then pulled off in the Z direction and a clear maximum bond strength value is determined. In addition to very efficient specimen preparation and high repeat accuracy, this method also allows you to determine the cohesion and adhesion components of the fracture pattern. The good comparability of the results achieved with this test procedure also enables reliable monitoring of the coating quality in the production process.
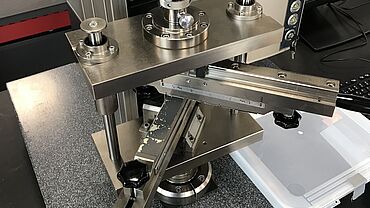
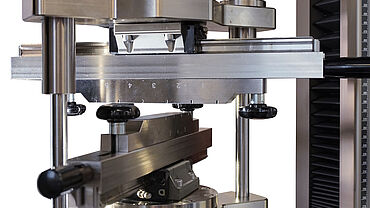
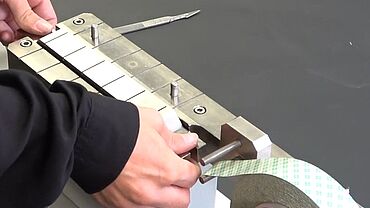
Video: Adhesion Test on Electrode Coatings
The adhesion test in Z-Direction is a more reliable and reproducible method for determining the adhesion strength between active material coatings and electrodes (Al or Cu foil) on lithium-ion batteries and for assessing the type of failure.
- In the field of quality assurance, peel tests are an important indicator of process reliability when it comes to the adhesive strength of the coating. The better the adhesive strength, the better the performance and durability of the battery.
- If you work in research and development, our peel tests help you optimize the possible combinations of different materials and thus increase battery performance.
Friction tests on electrode coatings, arrester foils and separators
Determination of the coefficient of friction of electrode coatings, arrester foils and separators in the production of lithium-ion batteries is of great significance in identifying problems during the production process and ensuring the quality and performance of the batteries.
Possible friction tests include:
- Coating adhesion test: the bond between the different layers in the battery cell is tested. Application of a specified force or load allows you to evaluate the tendency of the layers to either separate or bond. The resulting layer separating forces then help you draw conclusions about the friction coefficients.
- Contact force and displacement test: These tests measure the force required to move or separate materials with different coatings or surfaces. This allows the behavior of the materials under pressure to be understood and the coefficient of friction to be quantified.
Since there are still few special test standards for EV batteries in general and also for this application, ASTM D1894 and ISO 8295 can be used as substitute standards for characterizing their friction properties. These tests are also carried out in an electrolyte-wetted state in order to achieve realistic mechanical characteristics.
Characterization of solid-state battery components
With the elimination of the liquid electrolyte in solid-state batteries, new challenges arise such as boundary layer contact, thermal expansion and resistance to aging. For the characterization of solid-state battery components, ZwickRoell offers solutions for a wide range of test methods that address special solid-state battery requirements.
- The mechanical characterization of a lithium metal anode can be challenging. Specimen preparation and determination of the tensile strength must be carried out in an inert gas environment due to the strong degradation. In addition, the sensitive, ductile material requires extremely careful handling in special specimen clamps and reliable determination of the axial strain using an optical extensometer. ZwickRoell offers special protective gas chambers (glove boxes), specimen preparation and manipulation options, and adapted optical extensometers for non-contact measurement of the specimen.
- Another challenge is determining the mechanical properties of other components such as the composite cathode or the solid-state electrolyte separator. The strengths of these components greatly influence the design of the production processes and reliable battery functionality. A ZHN nanoindenter can be used to characterize solid-state electrolytes made of polymers, oxides or sulfides with different mechanical properties in order to investigate the Young's modulus, hardness, flexural strength and fracture toughness.
Functional and structural battery testing: Battery components, cells and cell connections
Functional and structural testing of cells and cell connections plays an important part in assembling cells into modules and packs as well as for reliability in battery operation. Battery swelling during the charging and discharging process, is determined by high-precision swelling tests, so that it can be taken into account in subsequent steps. The prevailing pressure in the cell is tested in crush and bend tests, including abuse tests such as the nail puncture test.
Battery swelling test: Characterization of the cell behavior in the charge and discharge cycle
The behavior of the battery cells during the charge and discharge process, especially the expansion of the cell, referred to as battery swelling or battery respiration, influences the performance and service life. This phenomenon is particularly evident in prismatic cells and pouch cells, as well as solid-state batteries. However, understanding the expansion of cylindrical cells is also becoming increasingly important in the development of new battery generations.
The precise characterization of this behavior under simultaneous tempering is critical. Respiration of the cell must be taken into account for the assembly in the module, as the expansion of the cells in the module leads to a change in the pressure on the cell. This pressure and the temperature significantly influence the service life and performance of the cells. Therefore, accurate characterization of the cell respiration and swelling are very important. ZwickRoell offers various approaches for characterization of the cell behavior in the charge and discharge cycle, including electrical cyclization, high-precision deformation measurement, long-term test procedures and controlled temperature.
- Temperature control of the entire battery cell
The battery cell is heated to a desired operating temperature using a temperature chamber, which is kept constant in the chamber for the duration of the test. Control is based on the ambient temperature in the temperature chamber. Depending on the risk, safety during the test is ensured via the temperature chamber or a proactive chamber with a suitable hazard level. - Precise and homogeneous temperature control of the complete battery cell
By actively heating and cooling the compression platens, the surface temperature of the battery cell is homogeneously tempered and precisely controlled from above and below. On the other hand, local temperature fluctuations within the battery cell can also be compensated. Critical temperatures at high discharge currents, for example, are therefore counteracted and reliable testing is ensured.
This type of testing was developed in collaboration with MBTS. An article has now examined the influence of different temperatures, pressures and discharge rates on the electrical properties of a standardized lithium-ion battery cell for automotive applications.
Link to article
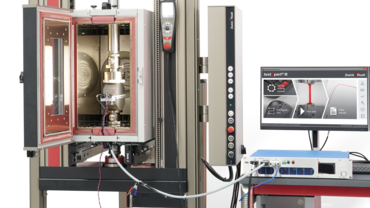
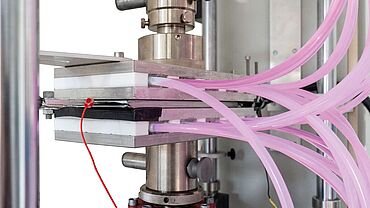
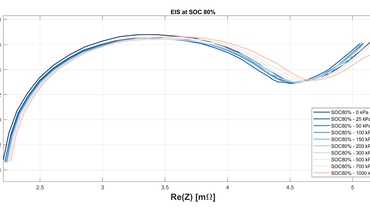
Battery abuse testing
Battery abuse tests are destructive reliability tests for lithium-ion batteries. These tests are required for market release and use of batteries in automotive applications. During the tests, the battery is exposed to extreme conditions to ensure its safety and reliability. In addition to thermal and electrical tests, typical abuse tests also include mechanical tests.
During mechanical tests, the battery is physically stressed by an object penetrating it or by applying a mechanical load to it in order to test its integrity. For example, this involves investigating how nail penetration (nailing), which causes an internal short circuit, or crushing affects the functionality and safety-related behavior of the battery.
These battery abuse tests typically lead to thermal runaway, which can result in fire or explosion. Due to environmental regulations and occupational safety awareness, these tests must not be carried out in open environments or old buildings without exhaust gas treatment, to ensure reproducible environmental conditions.
With the universal testing machine AllroundLine Z100 from ZwickRoell and the Weiss Technik extreme event environmental simulation system, battery tests can be performed with a maximum force of 100 kN. Thanks to the mechanical modularity, test tools can be changed easily and safely and various mechanical abuse tests can be carried out safely on one machine. The test results are evaluated with the testXpert testing software.

Comprehensive know-how and experience in materials testing, access to all high-precision testing machines and the complete accessories portfolio in our ZwickRoell Battery Test Center are available for your application technology consultation.
Are you interested in free pretesting in our Battery Test Center? We're happy to assist you in the selection of the right test equipment for your needs.
Mechanical testing plays a critical role in both the ongoing development of battery technology and quality assurance in battery production. Major material-related challenges as well as multi-physical requirements (mechanics, temperature, electricity) require close cooperation between the battery customer and the testing machine manufacturer. We have made it our mission to develop the best possible testing concepts with and for our customers.
Our new battery testing laboratory is equipped with the state-of-the-art testing technology that covers different mechanical battery tests for cell characterization both in the field of research and development and in battery production. Two application experts are available to our customers for both onsite and remote testing. In this way, we want to ensure that we find the best possible testing concept for the respective requirements of our customers.
Take a virtual look around our laboratory or contact us today—we will be happy to advise you!
Depending on the application, there are different types of batteries with a wide range of properties. The best known: Lithium-ion batteries. They are used in many electronic devices and electric vehicles (EV battery, electric vehicle battery). There are also a large number of different cell chemistries that are constantly evolving. Cell chemistries lead to heterogeneous battery properties, which is why precise characterization is also mechanically important. Cell formats, such as cylindrical, prismatic and pouch cells, offer a variety of advantages and disadvantages in terms of energy density, space requirements and performance. Selection of the right battery type and cell format therefore always depends on the specific requirements of the respective application. In summary, it can be said that there is a wide variety of different approaches in the field of battery development and production. Therefore, the availability of a wide range of test methods is also necessary.