ISO 6892-1 Tensile Test on Metals at Ambient Temperature
The DIN EN ISO 6892-1 standard for tensile tests on metals standardizes tensile testing of metal or steel at ambient temperature and defines the mechanical characteristic values.
Objective & applications ISO 6892 by temperature range Characteristic values Video / running a test Force/extension measurement Test speed Strain rate control Testing software Testing systems
Objective and applications of the ISO 6892-1 standard
The tensile test is the most important and most frequently used mechanical-technological test worldwide, used to determine the strength and strain characteristic values for metals applications that are of crucial importance in the design and construction of components, commodities, machines, vehicles and buildings.
The test task is to determine material characteristic values reliably and reproducibly and achieve international comparability.
The uni-axial tensile test is the method used to determine the characteristic values for yield point or offset yield, tensile strength and strain at break. In addition, lower yield point, yield point extension and extension at maximum force are determined.
Tensile test on metals to ISO 6892 – differentiation based on temperature range
In tensile testing on metals, the standard differentiates among four temperature ranges in which tensile tests are performed: room temperature, elevated temperature, low temperature and the temperature of liquid helium. The different temperature ranges and the liquid helium medium impose very distinct requirements on the testing systems and the test method, including the specimens to be prepared. Therefore, the international ISO standard is divided into four different parts, each of which addresses one of the above-mentioned temperature ranges:
- ISO 6892-1 test method at room temperature
- ISO 6892-2 Test method at elevated temperature
- ISO 6892-3 test method at low temperatures
- ISO 6892-4 test method in liquid helium
In addition to these internationally accepted ISO standards, national standards including the American ASTM standard, the European EN standard, the Japanese JIS standard and the Chinese GB/T standard are also applied internationally. For specialized fields of application, i.e. aerospace, additional specific standards may be important or required.
DIN EN ISO 6892-1: Important characteristic values
The tensile test on metals or metallic materials, is mainly based on the standards DIN EN ISO 6892-1 and ASTM E8. Both standards specify specimen shapes and the respective testing process. The objective of the standards is to define and establish the test method in such a way, that even when different testing systems are used, the characteristic values to be determined remain reproducible and correct. This also means that the standard requirements address important influencing factors and generally formulate requirements in such a way that there is enough leeway for technical realizations and innovation.
Important characteristic values related to tensile testing on metals according to ISO 6892-1 include:
- The yield point; more accurately the upper and lower yield point (ReH and ReL)
- The offset yield; generally determined as replacement yield point at 0.2 % plastic elongation (Rp0.2).
- The yield point extension; more accurately extensometer yield point extension, because it can only be determined with the use of an extensometer (Ae)
- The tensile strength(Rm)
- The uniform extension (Ag)
- The strain at break (A), whereby the normative specifications with regard to the gauge length are of significant importance
Tensile strength with different material hardening
For metallic materials with a pronounced yield point the tensile strength (maximum tensile force) is defined as the highest reached force after the upper yield point. The maximum tensile force after exceeding the yield point can also lie below the yield point for weakly work-hardened materials, therefore the tensile strength in this case is lower than the value for the upper yield point.
The stress-strain curve image shows a curve with a high level of work-hardening (1) and with a very low level of work-hardening (2) after the yield point.
For metals with yield point and subsequent stress, on the other hand, the tensile strength corresponds to the stress at the yield point.
Yield point (ReH and ReL), offset yield (Rp and Rt) and tensile strength (Rm)
For determination of the yield strength and tensile strength, only a precise force measurement is required, while for all other characteristic values a (automatic) strain measurement using an extensometer during the test, or manual strain measurement after removal of the specimen or specimen remains is necessary.
Strain at break A or At
The strain at break A or At is a measurement of the ductility, or the flow properties of a material.
Modern algorithms, which automatically analyze the stress-strain curve, ensure reliable specification of the break point and accurate determination of the strain at break. The break location along the specimen, more specifically along the parallel length of the specimen, is also important for reliable and accurate determination of the strain at break. If the break or point of failure is not within the gauge length of contact-type extensometers, the plastic deformation that occurs during necking and the point of failure cannot be correctly determined. Modern evaluation algorithms estimate the point of failure, or break point, relative to the measuring points of the extensometer and denote an unreliable strain at break value.
With optical, non-contact extensometers, which record the entire parallel length of the specimen, the point of break or failure can be determined. If the point of break is outside of the initial gauge length, according to ISO 6892-1:2017 Appendix I, the strain at break can nevertheless be determined, if an appropriate number of gauge marks were considered and measured during the test. The laserXtens Array as well as the videoXtens Array provide an optional solution for this task. With their use, the strain at break is automatically determined both reliably and accurately on 100% of the specimens.
The JIS Z2241 provides a classification of the break point. This is normally done manually through visual testing or by separate non-contact measurement. Both methods are personnel and time consuming. With modern optical, non-contact extensometers this task is automatically handled for tensile tests: indication of the class (depending on the break point A, B or C) is then part of the determined and recordable results.
Video: Running a test, tensile test on metal to ISO 6892-1
Running a tensile test according to ISO 6892-1 Method A1 and A2 with a tensile testing machine and makroXtens extensometer
Test or test equipment requirements
When determining the characteristic values defined in ISO 6892-1, precise force measurement and measurement of the specimen extension under force application (strain measurement) play a key role. Equally important is the test speed that is specified in the standard in two different methods. A differentiation is made between Method B (via an increase in stress application) and Method A (via the strain rates). Method A - and here Method A1 via automated strain rate control using the extensometer signal (closed loop) is the easiest and most precise method. ZwickRoell test equipment is designed and specialized for this purpose.
Requirement for force measurement and measurement of extension
The most important and clearly describable requirements also relate to force measurement and the measurement of extension of the specimen under force application.
- For the force measurement the ISO 6892 standard series refer to ISO 7500-1, Calibration and verification of the force measuring system for tension and compression testing machines, and require Class 1 at a minimum.
- For measurement of the extension, the ISO 6892 standard series refer to ISO 9513, Calibration of extensometer systems used in uniaxial testing, and require Class 1 at a minimum for determination of the offset yield; for measurement of other characteristic values (with extensions larger than 5%) Class 2 may be applied.
The calibration processes, and especially the results and definitions of the classifications, are described in the standards for force measurement and extension measurement. The latter is crucial for application in the testing practice. Maximum permitted deviations and resolutions can be derived through the class affiliation for the calibrated measuring system, which have to be used for the determination of the measurement uncertainty of the measuring system.
- ASTM E8 refers to ASTM E4 for force measurement,
- and for the measurement of extension to ASTM E83.
- The internationally applied standards are sometimes different in the structure of their content, however in their definition and requirements they are in accordance so that the relevant characteristic values derived from tensile testing do not significantly deviate from each other.
One exception to be noted is the evaluation, and with that the classification of the extensometers. While ISO 9513 refers to the set value to be reached for the deviation, ASTM E83 also considers the ratio to the initial gauge length. An extensometer that is intended for small initial gauge lengths must meet higher measuring requirements than one for bigger initial gauge lengths.
Characteristic values, for which use of an extensometer of at least Class 1 to ISO 9513 for tensile testing of metal is required, are:
- Initial gradient of the stress-strain curve mE
- Offset yields Rp and Rt
Characteristic values, for which use of an extensometer of at least Class 2 to ISO 9513 for tensile testing of metal is required, are:
- Yield point extension Ae
- Uniform extension Ag and Agt, as well as
- Plateau range e around the tensile strength Rm or maximum tensile force Fm
- Strain at break A and At
Influence of the test speed on the yield points (ReH and ReL) and offset yields (Rp and Rt)
For correct determination of yield points (ReH and ReL) and offset yields (Rp and Rt), besides accurate force and strain measurement, the test speeds are also of significant importance. The standard differentiates between two methods to set the test speed: in method B, it is controlled by the stress increase, in method A by the strain rate. Method A, where the strain rates or the strain speed are taken into account, is recommended for the following reasons:
- Metallic materials change their characteristic values when the strain rates at which the tests are performed change.
- As a general rule, higher strain rates result in higher strength values.
- Depending on the alloy and product quality of the metallic material, the dependence on the strain rate can be very significant, and outside of the specification limits for corresponding qualities.
Test speeds in ISO 6892-1 |
---|
Method A1: Closed loop strain rate control | Method A2: Open loop strain rate control | Method B: stress speed |
No pre-testing/setup required (adaptive controller) | Pre-testing & setup required (determination of the testing system and specimen stiffness) | Pre-testing & setup required (determination of the testing system and specimen stiffness) |
Closed loop strain rate control is the easiest and most precise method
Strain rate control significantly improves the reliability of test results when determining the yield strength and offset yield values of a material. ISO 6892-1 presents two methods for the implementation of control via strain rates:
- Method A1 - automatic strain rate control through the use of the extensometer signal (closed loop)
- Method A2 - manual adjustment through preselection of a crosshead speed, at which the correct strain rate for determination of the characteristic value is then achieved (open loop)
The first method uses the modern technical features provided by drive controllers—preferably an adaptive controller—to automatically maintain the crosshead speed in the tolerance range for the strain rates specified by the standard. This method requires a control-technology-equipped testing system, however it significantly simplifies the test operation and eliminates errors in setting the crosshead speed. This control method is therefore recommended.
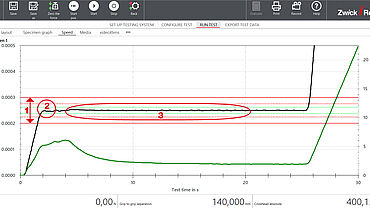
With testXpert, the strain rate is always traceable. The red line (1) shows the ISO 6892-1-defined tolerance range (20% of the set speed). The green dashed line represents the narrower tolerance range of 5%, which is the benchmark used by ZwickRoell testing systems to be on the safe side in the event of unforeseen events.
Good strain rate control is characterized by (2) low inlet fluctuations and (3) stable speed control. An important requirement for this is an adaptive controller.
How does closed loop strain rate control work in the testing system?
For precise adjustment of the strain rates, our testControl II electronics system controls the speed of the testing machine through direct use of the measured values of the extensometer. The testing machine control parameters are automatically calculated and adaptively adjusted in real time. This process is called closed loop with adaptive control and runs on ZwickRoell testing machines at 1 kHz. This easily meets the standard requirements for compliance with the strain rate.
Everything is automatic, very uncomplicated, and saves the operator a lot of time in producing reliable results with low scatter.
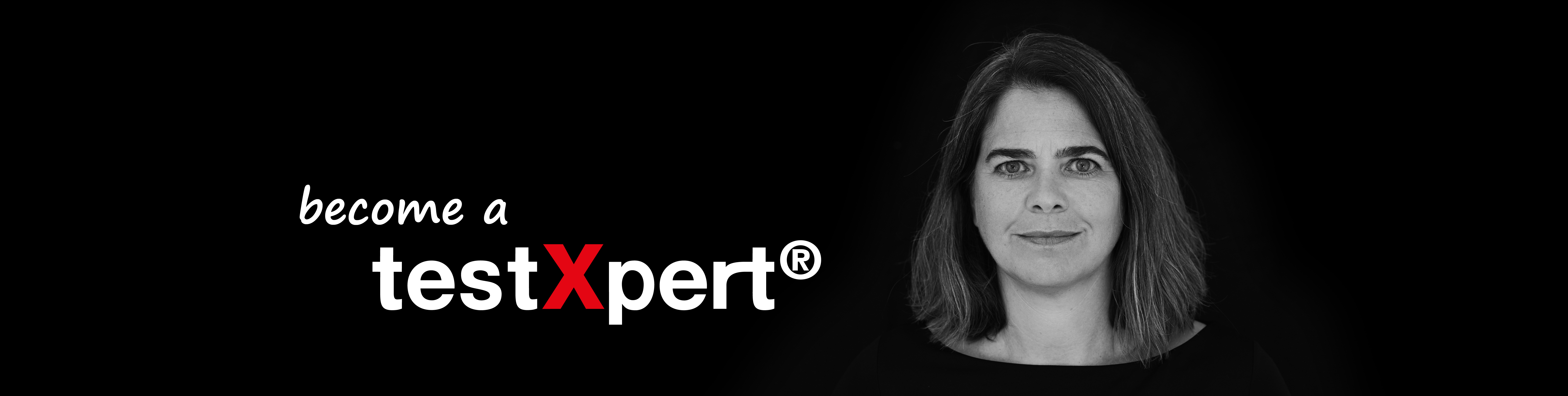
ISO 6892-1 with testXpert testing software – efficient and reliable testing
With testXpert, you increase efficiency for tests to ISO 6892-1. And testXpert delivers reliable test results, the foundation for decisions you can count on.
- Regardless of the method you select, all the parameters specified by ISO 6892-1 are included in test program with 100% standard-compliance. In a preconfigured layout, you see the true achieved strain rate within the tolerances specified by the standard.
- Don’t spend unnecessary time on pre-tests and manual calculations for the strain rates according to ISO 6892-1. testXpert takes on automatic setting of all control parameters. Target positions and strain values are approached with pinpoint accuracy. Changes in specimen properties are compensated on line.
- testXpert ensures repeatable test results through identical test conditions via a predefined machine configuration.
- For reproducible test results, operator influence is reduced to a minimum, for example through our user management feature.
TENSTAND software validation
100% reliable test results with validation to ISO 6892-1/TENSTAND.
The test results that are determined with the software to standard ISO 6892-1 can be verified and validated with an internationally coordinated data set and internationally coordinated test results. In a European research project with the acronym TENSTAND, raw data from tests on metals was generated and qualified. This data was used to determine and qualify test results and ranges of results. With the TENSTAND sets of data and sets of results the testing software can be quickly and reliably verified through comparison of results. The National Physical Laboratory (NPL) in London has these sets of data and sets of results available.
- The National Physical Laboratory (NPL) is the British counterpart to the German national metrology institute Physikalisch-Technische Bundesanstalt (PTB). It defines the national standards applicable in the field of physics and technology.
- Its responsibilities include the determination of fundamental and natural constants, representation, preservation and transfer of legal units of the International System of Units (SI), supplemented by services such as UKAS (United Kingdom Accreditation Service) calibration services for the legally regulated sector.
Reliably reproducible test results with TENSTAND and testXpert
Verify your test results with TENSTAND software validation.
- Upload TENSTAND ASCII raw data sets from NPL to the testXpert III testing software
- Determine test results from these raw data sets with testXpert
- Compare results with TENSTAND results