5 Tips: How to Extend the Service Life of Your Testing Machine
A testing machine that lasts a lifetime. Something any material tester or laboratory manager hopes for. When you invest in a testing machine, you think longterm. Ideally a machine lasts forever. However, many different factors affect the service life of a testing machine. This includes:
- The number of tests performed
- The material to be tested
- Remaining service life
- Environmental conditions
- External factors, such as the availability of components
All of these factors directly or indirectly influence the durability and service life of your testing system and its components. With a few simple tricks you can extend the service life of your testing machine for many years.
Tip 1: 10 years guaranteed spare parts availability - double the benefits
The new service life of your testing machine begins upon commissioning. Throughout the life cycle of your testing machine, there are a number of factors that can affect and in some instances shorten this cycle. For one, every machine has components that age over time. To ensure hassle-free operation, regular replacement of wear parts is essential. Only by replacing these components, are you able to increase the service life and reliability of your machine and ensure its full potential.
On the other hand, there are situations where replacement is necessary, regardless of the condition of machine wear parts. But this does not mean that the complete testing system has to be replaced. In this case, we turn to spare parts, which provide an excellent opportunity to extend the service life of your testing machine. Spare parts not only ensure higher quality and reliability of the system, they also extend warranties. At ZwickRoell, we offer 10 years of spare parts availability. And, if at all possible, we try to extend this promise beyond the 10 years. With the right level of care and the right spare parts availability, you can significantly increase the life cycle of your testing machine.
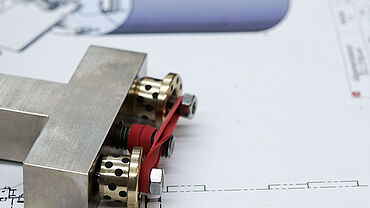
Tip 2: implement updates and upgrades
External factors can always affect the service life of a materials testing machine. For example, end-of-support for the operating system. This can sometimes lead to increased security and compatibility issues and longer downtimes. But there is a simple and easy solution: updates. Only by regularly updating you software versions, can you minimize the risk of downtimes and maintain a state of the art technological status.
Additionally, upgrades further increase flexibility for future technical developments. These are available for both your software programs and hardware. Software upgrades not only involve moving up to the next version, they are a switch to the latest generation of software. That is, an upgrade to testXpert III. This step, of course, also involves a number of additional benefits including the use of new test programs, the latest software technology and new testing possibilities.
Hardware can also be upgraded. Here too, there are external factors that we ourselves cannot control or influence. On the one hand, it may based on the availability of materials on the market, which has significantly worsened in the last few years, especially when it comes to electronic assemblies. In addition, due to technical innovations, older components may no longer be available as development and production is designed to incorporate the latest technology. In order to counteract these factors, it makes sense to upgrade the measurement and control electronics hardware, and we definitely advise it. The motor and drive are retained and new powerful machine electronics are integrated. Since we use the latest electronics that are also installed in new machines, limited material availability no longer plays a role. Furthermore, a hardware upgrade also extends spare parts availability for another 10 years.
Our tip: don’t let external circumstances slow you down—invest in the future of your testing machine.
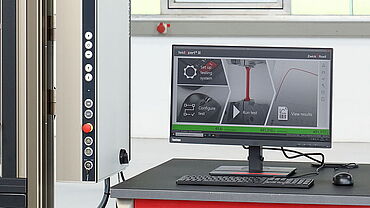
Tip 3: retrofit your machine and meet every test requirement – today and tomorrow
Have your test requirements changed? Are you being challenged with a new standard or test type? There is no reason to by a new testing system.
All ZwickRoell testing machines are based on a modular connection concept with standardized interfaces. This modular design makes it possible to retrofit additional accessories to existing testing machines as needed—quickly and conveniently. Regardless of whether you need new specimen grips, jaw inserts, test tools, extensometers, temperature or environmental chambers, load cells, electronics accessories or safety devices—every ZwickRoell accessory can be retrofitted into an existing testing system. This saves you both money and time with minimal expended effort.
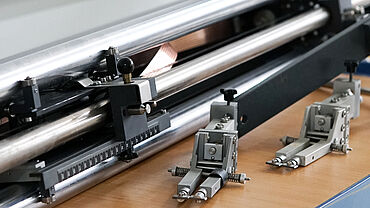
Tip 4: hardware and software modernization: always up-to-date on the latest technology
The best alternative to extend the lifetime of your testing machine—for many years—is through modernization. A modernization consolidates all of the previously mentioned tips: an overhaul of the load frame, replacement of the measurement and control electronics, replacement of the drive technology and a software upgrade. And best of all: a modernized testing machine is in no way inferior to a new machine. Another advantage: you can continue using the accessories you currently have.
A modernization not only extends the service life of the machine, it also significantly contributes to the protection of our environment: a modernization reduces CO2 emissions. The load frame is made of steel or aluminum. If necessary, it is reconditioned and can then continue to be used. All other elements are technically upgraded so that your modernized machine is equivalent to a new machine.
A modernization not only significantly extends the lifetime of your testing machine, it also prepares you for any circumstance and requirement that may arise in the future—regardless of the situation. Don't wait any longer. Invest in the modernization of your machine!
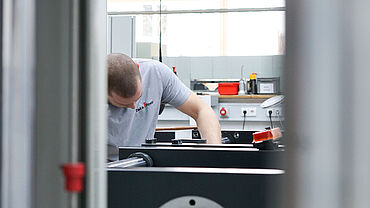
Tip 5: Regular maintenance extends the service life of your testing machines!
Calibration , maintenance and inspection are essential to ensure the accuracy and service life of your testing machines. Regular calibration ensures that measurement results are reliable and conform to standards, while maintenance and inspection prevent wear and tear and avoid unplanned downtime. With a worldwide service network and recognized accreditations, ZwickRoell is your reliable partner for the highest testing quality.
Are you already familiar with our service agreements? Take advantage of the benefits not only from a professional inspection and calibration, but also from numerous other advantages.