ASTM D695 Compression Test on Composites and Plastics
The ASTM D695 standard describes the compression test for determination of mechanical characteristics such as the Young's modulus and strength for unreinforced and reinforced plastics according to the end loading compression principle. The force is applied solely via the end faces of the test specimen. ASTM D695 can be used for fiber composites with a stiffness of up to 41 GPa, which includes glass fiber reinforced fabric composites.
The following text is limited to the ASTM D695 test setup with support jig for high-modulus and reinforced plastics with a laminate thickness of < 3.2 mm. The end loading compression tests to DIN EN 2850 Method B, Boeing BSS 7260 Type III & IV (modified ASTM D695) and SACMA SRM-1R-94, which have been further developed from ASTM D695, are also described. The latter also enable compression tests on unidirectional (UD) carbon fiber-reinforced laminates with correspondingly high stiffness and strength.
Other standardized compression tests frequently used for continuous fiber-reinforced composites without restrictions regarding laminate stiffness are ISO 14126 Method 1 and ASTM D3410 (shear loading compression) as well as ISO 14126 Method 2 and ASTM D6641 (combined loading compression).
Characteristic values Running a test and test equipment Specimens Downloads FAQs Request a consultation
ASTM D695: objective & characteristic values
The following characteristic results and values for fiber-reinforced plastics can be determined with the compression test according to ASTM D695 with compression support and in particular with the variants developed from ASTM D695 (EN 2850 Method B, SACMA SRM-1R-94, Boeing BSS 7260 Type III & IV):
- Compressive stress: compressive force related to the initial cross section of the specimen
- Compressive strain: change in gauge length in relation to the initial gauge-length in the load direction (only when using a suitable measurement system, see below)
- Compressive modulus: slope of the stress-strain diagram in a specified strain interval in the elastic range. Also called modulus of elasticity or Young’s modulus
- Compressive strength: maximum compressive stress carried by a specimen during a compression test
Important information on determining results
ASTM D695 provides a waisted specimen geometry for unreinforced and reinforced plastics with a thickness of < 3.2 mm, with which the compressive modulus (when using a suitable strain measurement system) and compressive strength can be determined in a test. An additional support jig must be used for this.
However, waisted specimens are not suitable for UD composites. The variants developed from ASTM D695 (EN 2850 Method B, SACMA SRM-1R-94, Boeing BSS 7260 Type III & IV) therefore always use two different specimens of uniform rectangular cross section:
- A specimen without tabs for determination of the compressive modulus. This specimen must not be used to determine the compressive strength, as premature failure always occurs at the end faces at a lower compressive stress than the compressive strength of the material to be tested.
- A specimen with adhesively bonded tabs to determine the compressive strength. The test is valid if the specimen fails within the free specimen length. This specimen is not suitable for determining the compressive modulus, as the application of strain gauges in the free specimen length (approx. 5 mm) would be very difficult.
Since the force is always applied exclusively via the end faces of the specimen, very precise machining of the end faces is absolutely critical in every case.
End loading compression test fixture
ASTM D695 requires a support jig for the specimen when testing materials with a thickness < 3.2 mm. The supported specimen is then placed in a suitable compression fixture (also referred to as a subpress or compression tool in ASTM D695).
In the variants for advanced composites from ASTM D695 (EN 2850 Method B, SACMA SRM-1R-94, Boeing BSS 7260), this support jig is firmly connected to a corresponding compression fixture, so that tilting or buckling of the specimen with the support jig is impossible.
- This advanced end loading compression fixture is also referred to as modified ASTM D695 device in the Boeing BSS 7260 standard.
- The test standards DIN EN 2850 Method B and SACMA SRM-1R-94 also use this principle, with minor differences in the dimensions of the support jig and the specimens.
- It should be noted that the length of the support jig according to DIN EN 2850 Method B is defined as 70 mm, while the support jig in all other test standards (ASTM D695, Boeing BSS 7260 Type III & IV, SACMA SRM-1R-94) has a length of 73 mm. A separate test fixture must therefore be used fro DIN EN 2850 Method B.
In any case, the support device does not contribute to the force transmission into the specimen. Friction between the specimen and the support jig is minimized by an appropriate design of the contact surfaces. In ASTM D695, a hand-tight attachment of the support jig to the specimen is sufficient. For all other advanced end loading test methods, a low tightening torque or contact force is defined for the retaining bolts.
ZwickRoell test fixture for the end loading compression test to ASTM D695 and variants:
- The ZwickRoell test arrangement for the end loading compression test consists of a compression fixture placed between two compression platens. Guide elements on the compression fixture ensure that the specimen is consistently centered in the load axis. Due to the high compressive strength of well over 1000 MPa in some cases, especially in compression tests for UD carbon fiber-reinforced composites in the fiber direction, appropriately hardened compression platens must be used.
- ZwickRoell test fixtures for end loading compression can be used in a temperature range of -80 °C to +300 °C.
Testing machines for ASTM D695
- Using the nominal specimen geometry, maximum forces of up to approx. 50 kN can now be achieved for UD carbon fiber-reinforced composites in the end-loading compression test thanks to the continuous further development and improvement of the mechanical properties of fibers and matrix. As tensile tests are usually carried out in addition to compression tests, where the maximum forces are even higher, the use of a static testing machine with a capacity of up to 100 kN or 250 kN is recommended.
- However, if only glass fiber-reinforced composites are tested, a 50 kN testing machine is sufficient.
Modular testing system for composites
Larger testing laboratories with correspondingly high test volume use different testing machines for the very diverse composite testing methods, and can thereby minimize conversion efforts. The individual testing machines can be adjusted to the force range required for the various types of tests. If throughput rates are not high or consistent enough that an investment in multiple testing machines makes sense, an alternative option is to equip a single testing machine so that you can perform as many test methods as possible with the least amount of machine conversion effort.
ZwickRoell developed a modular design, which is available as a 100 kN or 250 kN testing machine covering 21 test methods and approximately 120 test standards (ISO, EN, ASTM, as well as Airbus AITM and Boeing BSS), and which allows for comprehensive characterization of fiber-reinforced composite materials at ambient temperature or for tests at low or high temperatures ranging from -80 °C to +360 °C.
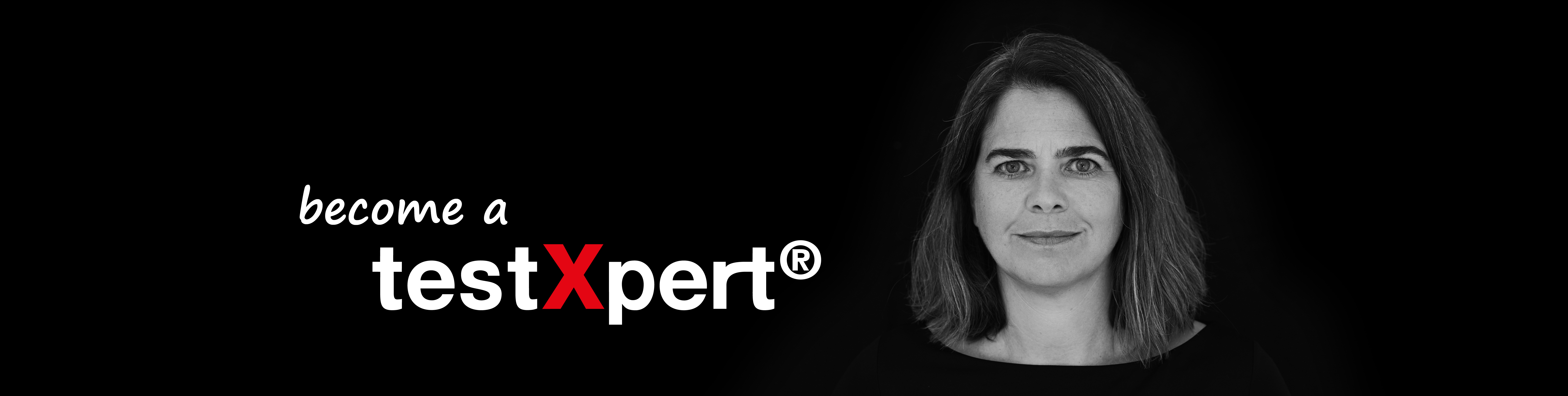
Reliable end loading compression tests thanks to our testXpert testing software
Our testXpert testing software supports efficient testing and reliable test results in accordance with ASTM D695 and the variants of the end loading compression test developed from ASTM D695.
- Eliminate the need to study the standards: guaranteed standard compliance through standard test programs - all characteristic values and parameters specified by ASTM D695 and DIN EN 2850 are pre-configured.
- Maximum testing efficiency is achieved through the connection of peripheral devices: when the specimen dimensions from the micrometer are sent directly to the testing software, you save time and avoid input errors.
- Additionally, verify and control the temperature in the chamber via the software. Set temperature ramps and see the values that have been maintained retrospectively, with traceability.
Strain measurement to ASTM D695 and respective variants
Suitable methods for strain measurement for the end loading compression test according to ASTM D695 are strain gauges placed centrally on the specimen surface or mechanical extensometers, which measure the compression at the edge of the specimen. When using strain gauges, the elements of the support device must have a suitable recess in the middle so that they do not come into contact with the strain gauge measuring grid or the strain gauge cables.
Due to the precisely centered positioning of the specimen in the load axis and recesses in the body of the ZwickRoell end loading compression test fixture, it is also possible to use the makroXtens automatic sensor arm extensometer, which measures both sides of the specimen edges.
In the variants of the end loading compression test developed from ASTM D695, strain is only measured for the specimen intended for the compressive modulus measurement. The corresponding test standards sometimes use different specifications for the maximum compression in the test and for the range in which the Young’s modulus is to be determined.
- DIN EN 2850 Method B: Compressive load up to at least 0.5 % (5000 µe) compression; Young’s modulus determination between 0.1 % and 0.5 % (preferred method, unless otherwise specified)
- Boeing BSS 7260: Compressive load up to at least 3000 µe compression; Young’s modulus determination between 1000 and 3000 µe.
- SACMA SRM-1R-94: Compressive load up to 5000 µe; Young's modulus determination between 1000 and 3000 µe; use of strain gauges applied on both sides to monitor a superimposed bending load is recommended; if the deviation between the two strain gauge signals is greater than 10 %, the test is invalid and should be repeated.
As described above, the strain measurement for the specimen with adhesively bonded tabs to determine the compressive strength is not provided for these test standards due to the very short free measuring length.
A mechanical extensometer measuring at the specimen edges is also suitable for the waisted specimen used in ASTM D695 for specimen thicknesses of less than 3.2 mm, which is used for determining both the Young's modulus and compressive strength.
Standard | Specimen type | Schematic diagram (not to scale) | Use and instructions |
---|---|---|---|
ASTM D695 | Waisted, for specimen thicknesses less than 3.2 mm | ![]() | Unreinforced and reinforced plastics with a stiffness up to 41 Gpa (e.g., also GFRP fabric composites) |
DIN EN 2850 Method B Boeing BSS 7260 SACMA SRM-1R-94 | B1 Type III Compression strength specimen | ![]() | UD* and fabric composites (GFRP, CFRP)
|
DIN EN 2850 Method B Boeing BSS 7260 SACMA SRM-1R-94 | B2 Type IV Compression modulus specimen | ![]() |
Frequently asked questions regarding the ASTM D695 compression test
ASTM D695 describes the compression test for determining mechanical properties such as the Young's modulus and strength of rigid plastics according to the end loading compression principle, in which the force is applied solely via the end faces of the test specimen. ASTM D695 can be used for composites with a stiffness of up to 41 Gpa, which includes glass fiber reinforced fabric composites. A support device is required for high-modulus and reinforced plastics with a laminate thickness of < 3.2 mm.
The ASTM D695 standard describes the compression test for determination of mechanical characteristic values such as the Young's modulus and stiffness of rigid plastics. ASTM D695-15 refers to the publication year 2015, but has since been updated and replaced by ASTM D695-23 or ASTM D695:2023.
ASTM D695 specifies a waisted specimen geometry with a length of L=79.4 mm and a width of B=19 mm for unreinforced and reinforced plastics with a thickness of < 3.2 mm, with which the compressive modulus (when using a suitable strain measurement system) and compressive strength can be determined in a test. However, waisted specimens are not suitable for UD composites. The variants developed from ASTM D695 therefore always use two different rectangular straight specimens: a specimen without tabs for determination of the compressive modulus and a specimen with adhesively bonded tabs to determine the compressive strength.