ISO 14126 | ASTM D3410: Shear Loading Compression
The ISO 14126 and ASTM D3410 standards describe the shear loading compression test on composites. The objective of this standard test method is the determination of compressive properties in laminate planes.
For this method, the compression force is transmitted via shear forces to the specimen, which is secured in the test fixture and usually includes cap strips. Homogeneous stress distribution is achieved if there is sufficient grip-to-grip separation in the unsupported center area of the specimen.
One of the benefits provided is axial guidance of the specimen during the test, as well as the elimination of force application via the end faces. This eliminates the need for high-precision preparation of the specimen end faces.
The DIN EN 2850 standard also describes the shear loading compression test on composites (Type A).
Shear loading compression test to ISO 14126, ASTM D3410
The shear loading compression method was standardized in the 1980s in ASTM D3410 as the Celanese test fixture with conical clamping elements. However, with this original Celanese device, variations in specimen thicknesses lead to unwanted linear supports of the conical clamping elements. This problem was solved in standards DIN 65375 and DIN EN 2850 (Type A) through modified Celanese test fixtures with flat wedges.
IITRI in the US developed a similar device with column guides, which replaces the old Celanese compression fixture in the current ASTM D3410. Here, the compression specimen is also clamped in guided flat wedges of the modified Celanese test fixture.
The compression specimen is first inserted in the wedge jaws, for which a separate tool is often helpful. The wedge jaws with installed specimen are then inserted in the guided compression test kit.
During the compression test, the gripping pressure is generated with wedge action created by the axial force. This can, however, lead to movement of the wedges and thereby uneven load application on the specimen.
To determine the validity of the compression test by quantifying superimposed bending deformations (percent bending), a strain measurement is carried out with separately measuring strain gauges applied centrally on both sides. The signals of the strain gauges are then averaged for determination of the compressive strain.
With the patented hydraulic compression fixture HCCF, originally developed by IMA Dresden and available through ZwickRoell, composite compression tests can be carried out according to common shear loading compression test methods.
The HCCF offers excellent accessibility, simple handling, and fixed jaws, which remain precisely aligned with one another without slipping, even during the test .
The shear loading compression method is ideal for unidirectional composite materials with lower strengths in the direction of the fiber, and for compression tests on fabrics and multidirectional composite laminates.
For high-strength carbon-fiber-reinforced composite materials and compression tests with unidirectional laminates in the direction of the fiber (UD0°), sole shear force application is often not sufficient. It either leads to invalid failure modes (end crushing, cap strip failure) or to lower compressive strength due to non-uniform stress distribution in the free specimen area. In this case it is better to apply the combined loading compression method.
Compression test kit (shear loading), IITRI version
- Applications: The compression test kit is used for testing fiber composites to ASTM D3410.
- Function description: The compression test kit is based on the wedge clamping principle. The kit consists of the following components: upper holder, specimen grip bodies, 3 sets of wedge jaws, setting gauge with centering spigot.
A centering aid allows for exact alignment of the specimen with the wedge jaws. The clamped specimen plus wedge jaws are inserted into the lower specimen grip body. The upper specimen grip body is inserted into the upper holder. The parts of the device are moved together and engage with each other. Centering bolts ensure alignment of the upper grip to the lower grip.
- Advantages:
- Centering aid for alignment of the specimen
- For compression forces up to 220 kN
- Wide temperature range of -70 to 300 °C
- No machining of the test specimen face necessary
Hydraulic composites compression fixture (HCCF)
- Applications:
- Test to ISO 14126, prEN2850, Airbus AITM 1-0008, ASTM D3410, ASTM D6641, JIS K 7076, RAE TR 88012 CRAG methods 400 and 401, QVA-Z10-46-38, ASTM C1358, Airbus document X88SP1105735: “Plain compression test according to AITM 1.0008 A1 and A2 with ZwickRoell HCCF”
- 'Plain', 'open hole and 'filled hole' compression tests with force application via clamping (shear loading) or with combined force application with end support and simultaneous clamping (combined loading)
- Function description: The hydraulic compression fixture for composites (HCCF = Hydraulic Composites Compression Fixture) is used for determining the compression properties of long-fiber-reinforced composites. Strain is measured using strain gages on both sides as standard (grid length > 3 mm).
The compression fixture has a connection hole at the top. The bottom is mounted on a compression platen. In the case of specimens for which the distance between the tabs and the grip-to-grip separation are at least 2 mm greater than the initial gauge-length, a clip-on extensometer measuring on both sides can be used (with a clamping fixture) on a customer-specific basis.
Advantages:
- Can be used for tests in an extended temperature range from -60°C to +150°C.
- Open design form (C-shaped) allows convenient specimen changing and simplifies use of extension measurement systems.
- Design ensures extremely accurate specimen alignment.
- Parallel-closing hydraulic clamping principle ensures slip-stick-free, flexure-free force application with largely constant deformation rate.
- Precision guide-columns for extremely precise alignment of specimen grips with each other.
- Low-friction ball-guides prevent distortion of test results.
- The magnetic support of the movable jaws facilitates changing of specimens and cleaning of the clamping surfaces
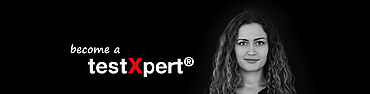
Take advantage of the leading testing software in materials testing
ZwickRoell’s testXpert testing software offers:
- Simple operation: start testing right away and be a testXpert while maintaining maximum safety.
- Reliable and efficient testing: benefit from reliable test results and maximum testing efficiency.
- Flexible integration: testXpert is the optimal solution for all of your applications and processes—simply put, a more effective workflow.
- Future-proof design: testing software for the entire life cycle, ready for your future test tasks!