Testing on fuel cells
When testing fuel cells, characterization of the materials and components is important to ensure the efficiency, performance and service life of hydrogen fuel cells for the long term. In terms of service life estimation/quality control, the property changes over time, as well as during assembly, make up the essential test aspects. Specimen preparation, specimen shapes and the test sequence are determined according to standards or individual customer requirements.
Testing of fuel cell components Testing in the assembly process Related products
What is a fuel cell?
Fuel cells convert chemical energy from gaseous hydrogen into electricity, water and heat. They, thereby supply the energy for systems in electronic products such as motor vehicles, or even stationary power plants. When compared to conventional technologies that are used in the energy or automotive industry, fuel cells have significantly higher efficiency, are emission-free and very quiet.
Fuel cells are broken down into different categories based on the electrolytes and electrodes used. Among these, proton exchange membrane fuel cell (PEMFC), especially for the automotive industry (medium and heavy-duty vehicles), are the most promising. Solid oxide fuel cells (SOFC) on the other hand, are mainly used in stationary energy storage.
The main research and development goals for fuel cells include cost efficiency, increased performance and the extension of service life.
A proton exchange membrane fuel cell (PEMFC) consists of a membrane electrode assembly (MEA), comprising a proton exchange membrane (PEM), catalyst layers (CLs), gas diffusion layers (GDLs), bipolar plates and seals.
Testing of fuel cell components
Mechanical properties are important for every component in the fuel cell system. When testing fuel cells, focus is on the following components:
- Proton exchange membrane (PEM),
- Gas diffusion layers (GDL),
- Bipolar plates and seals.
ZwickRoell offers solutions for tensile testing and creep testing with or without different media, adhesion testing, 3-point flexure testing and tear growth testing.
Testing of fuel cell components under mechanical load
The development of mechanical characteristics of components, combined components or the complete load cell after assembly, is critical for an understanding of the cell performance under real life operating conditions. ZwickRoell offers fuel cell testing solutions that help customers understand the influence of the assembly pressure on the change of mechanical characteristics (thickness, electrical properties and air permeability) of the fuel cell components.
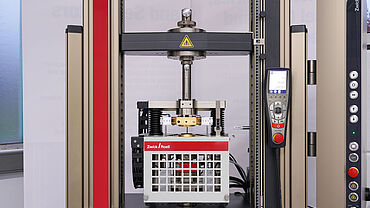
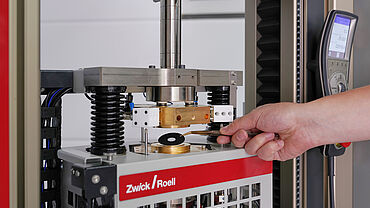
Multifunctional, efficient and precise characterization of gas diffusion layers
When testing gas diffusion layers, characterization of the material is important to ensure its efficiency, performance and service life for the long term. The deformation behavior under compression (TUC), the resistance (RUC) and the permeability (PUC) as a function of pressure are of decisive importance for research and development as well as for quality assurance.
ZwickRoell has therefore developed the Multifunctional Cell Component Analyzer (MCCA). With the use of three high-precision linear displacement meters and a leveling device, pressure can be applied precisely to an area of the gas diffusion layer. This enables accurate measurement of the change in thickness
under realistic compressive conditions. At the same time, the electrical resistance is measured via gold-plated compression platens, and the permeability via the gas introduced, which allows an evaluation to be carried out dependent on the pressure.
All the required test sequences are preconfigured in our testXpert testing software in full compliance with the standards, and they can be adapted to individual requirements. Thanks to the control, data acquisition and visualization of the connected sensors via testXpert, all tests can be displayed transparently and tracked seamlessly.
Benefits of the Multifunctional Cell Component Analyzer:
- Our three-in-one system supports efficient and highly precise measurement of TUC, RUC and PUC in a single test step
- All required test sequences are already preconfigured in the testXpert software program. The test can simply be started with a mouse click.
- Planning reliability based on modularity and retrofitting possibilities
- Unrestricted transparency and seamless traceability
Testing fuel cells in the assembly process
Assembly is a complex process. The interaction of assembly force and working temperature results in an uneven distribution of stress between the components, which leads of a certain degree of deformation. Inefficient and inaccurate assembly processes lead to increased manufacturing costs.
The use of ZwickRoell machines for fuel cell testing helps to
- Optimize the assembly process
- Understand the influences of the interaction between assembly forces and other loads
- Dynamically adjust the assembly load
- Adjust the assembly automation