E-Motor Testing
As electrification progresses and the associated technological developments continue, the efficiency and performance of electric motors are also constantly being improved. New technological approaches are also leading to new requirements in the field of e-motor testing. ZwickRoell offers a range of solutions to ensure that e-motors meet the highest standards of performance and efficiency. The focus is on innovative technologies such as hairpin or winding technology (rectangular copper wires insulated with a polymer coating) and electrical steel sheet testing, both of which make a decisive contribution to the efficiency and performance of e-motors.
With innovative testing solutions for precise material characterization and monitoring of the entire production process, ZwickRoell can make a decisive contribution to the optimization of e-motors.
Hairpin tests Electrical steel sheet testing Request a consultation
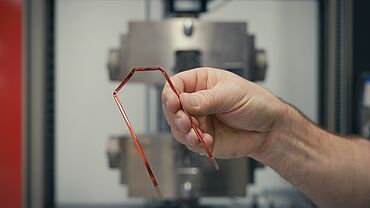
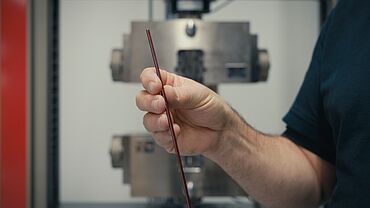
What exactly is hairpin technology?
Hairpin technology is a modern winding technique that uses rectangular, insulated copper wires, also known as “hairpins” due to their shape. This technology replaces traditional copper coils and helps to significantly increase the efficiency of e-motors and at the same time reduce the installation space by significantly improving volume utilization. To achieve this, the hairpins are processed in very complex winding and bending processes. In order for the production processes to run robustly and deliver good results, both the material behavior and the influence of the process parameters must be thoroughly understood. Suitable testing solutions are required for precisely this purpose.
Hairpin testing - new testing requirements
To ensure a stable stator production process, a precise understanding of mechanical properties is essential—not only to maintain consistent quality, but more importantly, to prevent bringing production processes to a standstill due to material inconsistencies. In addition to the material characteristics, the influences of the production parameters must also be analyzed and understood.
ZwickRoell offers a broad testing portfolio specifically for the characterization of rectangular coated copper wires for a comprehensive understanding of materials and processes and thus makes a decisive contribution to the further development of hairpin technology and hairpin stator production processes. This includes:
- High-precision determination of the elastic material behavior, which can deviate from the base material due to the coating and is of great importance for the production process due to springback
- Plastic material behavior of the hairpins up to break during the tensile test
- Bending behavior to check the flexural modulus and springback
- Simulation of the production process using torsion tests
- Precise analysis of the friction coefficient of the coating
Tensile test on hairpins
The thin polymer insulation has a direct influence on the formability of the copper wire, also with regard to springback after the bending process, which in turn influences the dimensional accuracy and can lead to problems in production. In addition, the insulation also has its own requirements: it must not show any cracks even with large deformation. It must be processable and it must be as thin as possible.
- Understanding elasticity is therefore crucial. In order to precisely determine the elastic range of the insulated wire in the tensile test, ZwickRoell has a two-sided extensometer with very high resolution, which is able to measure the modulus of elasticity separately on both sides of the specimen. This ensures high-precision test results.
- To determine the plastic deformation up to break, the strain of the specimen is recorded using a macroXtens extensometer.
Flexure test on hairpins
In a conventional 3-point flexure test with extensometer, the bending behavior can be characterized. On the one hand to determine a flexural modulus, but on the other hand also to check the springback. This test can be used for quality control as well as for the validation of simulation models.
Torsion tests for simulating the hairpin production process
To simulate the production process, ZwickRoell has a torsion testing system with which a torsion of the hairpin can be simulated at real production speed using a modularly adjustable bending/torsion tool.
- The test tool allows flexible adjustments to the hairpin geometry as well as the setting of different bending radii and enables the setting of different bending speeds and even the measurement of the springback angle via the testXpert testing software connection to the machine.
- This allows several parameters of the process to be viewed and analyzed separately. The combination with the mechanical characterization allows correlations to be made, with the help of which processes can be better understood and thus quality can be further improved.
Dynamic load tests on e-motor electrical steel sheets
Electrical steel sheets are highly specialized steel sheets that are used in the production of e-motors to conduct the magnetic flux and thus increase the efficiency of the motor. Their mechanical and magnetic properties are crucial for the performance of the motor, especially at high speeds and under dynamic loads, such as those found in electric vehicles.
In the steel industry, the development of new, innovative electrical steel sheets is currently a major trend topic. New materials always bring with them new forming and processing phenomena that need to be precisely understood and characterized.
Electrical steel sheet testing is essential in order to characterize not only their general mechanical properties but also their magnetic behavior and fatigue strength. Defective or poor magnetic properties can significantly impair the efficiency of the motor and lead to unnecessary energy losses. As a rule, electrical steel sheets are manufactured in a stamping process and the resulting hardened edge of the sheet can lead to edge cracks, i.e. premature failure, and also influence the magnetic flux. Good characterization of the sheets is therefore necessary.
Dynamic load tests: Electrical steel sheets are subjected to dynamic loads to test their fatigue strength and response under real operating conditions. For this purpose, ZwickRoell offers servohydraulic compact testing systems, which—thanks to the testing actuators mounted in the lower crosshead—are particularly well-suited for use at elevated temperatures.
Static materials testing of electrical steel sheets for e-motors
To ensure the mechanical functionality of electrical steel sheets in e-motors during processing and operation, conventional static test methods such as the tensile test in accordance with ISO 6892-1 and ASTM E8 play an important role in determining material parameters including the modulus of elasticity, yield strength, tensile strength and strain at break. They provide fundamental information about the mechanical behavior of the material under quasi-static load and are essential for material selection and quality assurance of materials, for example for stators and rotors in e-motors.
Electrical steel sheets are often very thin (usually between 50 and 100 micrometers) and very coarse-grained. This can lead to very complex deformation and failure behavior.
- DIN 50154, which specifies the tensile test on thin specimens with a nominal thickness of less than 200 µm, is therefore well suited as an alternative test method to ISO 6892. The static test values alone are often not sufficient to predict the local failure behavior in forming processes. Both standard test methods are already offered as test programs in ZwickRoell’s testXpert testing software so that all important test parameters are already preset.
- Sheet metal testing helps to investigate the fracture behavior in realistic forming processes (e.g. deep drawing) and provides information about the formability and the tendency to crack formation.
- In a hole expansion test, the edge crack sensitivity of the electrical steel sheets can be analyzed. ZwickRoell offers AI-supported optical detection of the failure and thus ensures highly user-independent and reproducible results.
Scientific study on electrical steel sheets
Multifunctional analysis of mechanical and magnetic properties of electrical steel sheets
The German Research Foundation (DFG) funded a research project involving many universities, in which ZwickRoell systems were used in several studies. Research demonstrated that a stamping process can be used to intentionally introduce residual stresses into the electrical steel sheet. These residual stresses influence the magnetic flux in the sheet metal and can therefore increase efficiency. Using a tool developed as part of the research project, the magnetic material behavior could be measured in-situ in a tensile test.
See image; compare with DFG reserach report “Increased Efficiency of Electrical Steel by Targeted Residual Stress” Page 206, section 12.4

ABOUT THE AUTHOR:
Head of Global Industry Management
- Responsible for the strategic development of testing solutions in the mobility and battery sector at ZwickRoell
- Specialist for mechanical materials and component testing in the automotive industry
- Several years of research experience at the Chair of Forming Technology and Foundry Engineering (utg) at the Technical University of Munich
- Directed numerous bilateral research projects with leading automotive manufacturers
- Scientific focus: Characterization of sheet metal materials and in-situ diffraction experiments
- 2023 Doctoral Thesis on the topic: Elastic-plastic characterization of high-strength steels