ASTM D3039 Tensile Test on Composites
The tensile test according to ASTM D3039 / ASTM D3039M is used to determine the tensile modulus and Poisson’s ratio elastic characteristic values, as well as the tensile strength of composite materials. This includes continuous fiber-reinforced unidirectional (UD) and multidirectional (MD) composite laminates, where MD laminates can consist of single layers UD laminates, wovens or other textile fiber architectures. Fiber-reinforced plastic composites (FRP) with discontinuous and randomly distributed reinforcing fibers (e.g., sheet molding compounds - SMC) can also be tested.
Also commonly used standards for tensile testing of long or continuous fiber-reinforced plastics are ISO 527-4 (test conditions for isotropic and anisotropic fiber-reinforced plastics) and ISO 527-5 (test conditions for unidirectional fiber-reinforced plastics).
Objective and characteristic values Running a test & test equipment Test conditions Specimens & dimensions Additional information FAQ Downloads
Objective of the test and determined characteristic values to ASTM D3039
Tensile tests on composites according to ASTM D3039 are performed to determine tensile properties in the material development and qualification process, for the determination of characteristic values to be used for the layout and design of composite structures, as well as in quality assurance.
Regardless of the type of fiber reinforcement, the following characteristic results and characteristic values are determined in ASTM D3039:
- Tensile stress: force related to the initial cross section of the specimen
- Axial strain: change in gauge length with reference to the initial gauge length in load direction
- Transverse strain: change in the gauge length with reference to the initial gauge length in transverse direction (only necessary for determination of the Poisson’s ratio)
- Tensile modulus: slope of the stress-strain curve in a specified strain interval in the elastic range. Also called modulus of elasticity or Young’s modulus
- Tensile strength: maximum value of the tensile stress determined in the tensile test
- Strain at break: axial strain when tensile strength is reached
- Poisson’s ratio: negative ratio of transverse strain to axial strain
For fiber-reinforced composites with bi-linear stress-strain behavior, an additional characteristic value can be determined:
- Transition strain: mean value of the axial strain in the transition area. Is usually determined from the axial stress-strain curve
Both the ASTM D3039 and the ISO 527-4/ISO 527-5 standards define test conditions for tensile testing of composites. Despite the similarities in the test methods, the determined characteristic values are not fully comparable, since the specimen shapes and specimen dimensions as well as the characteristic value determination differ in some aspects (e.g., strain interval for the tensile modulus and transition strain mentioned above).
To simplify test performance, testXpert test programs that are pre-configured with all settings according to the ASTM D3039 standard requirements can be used.
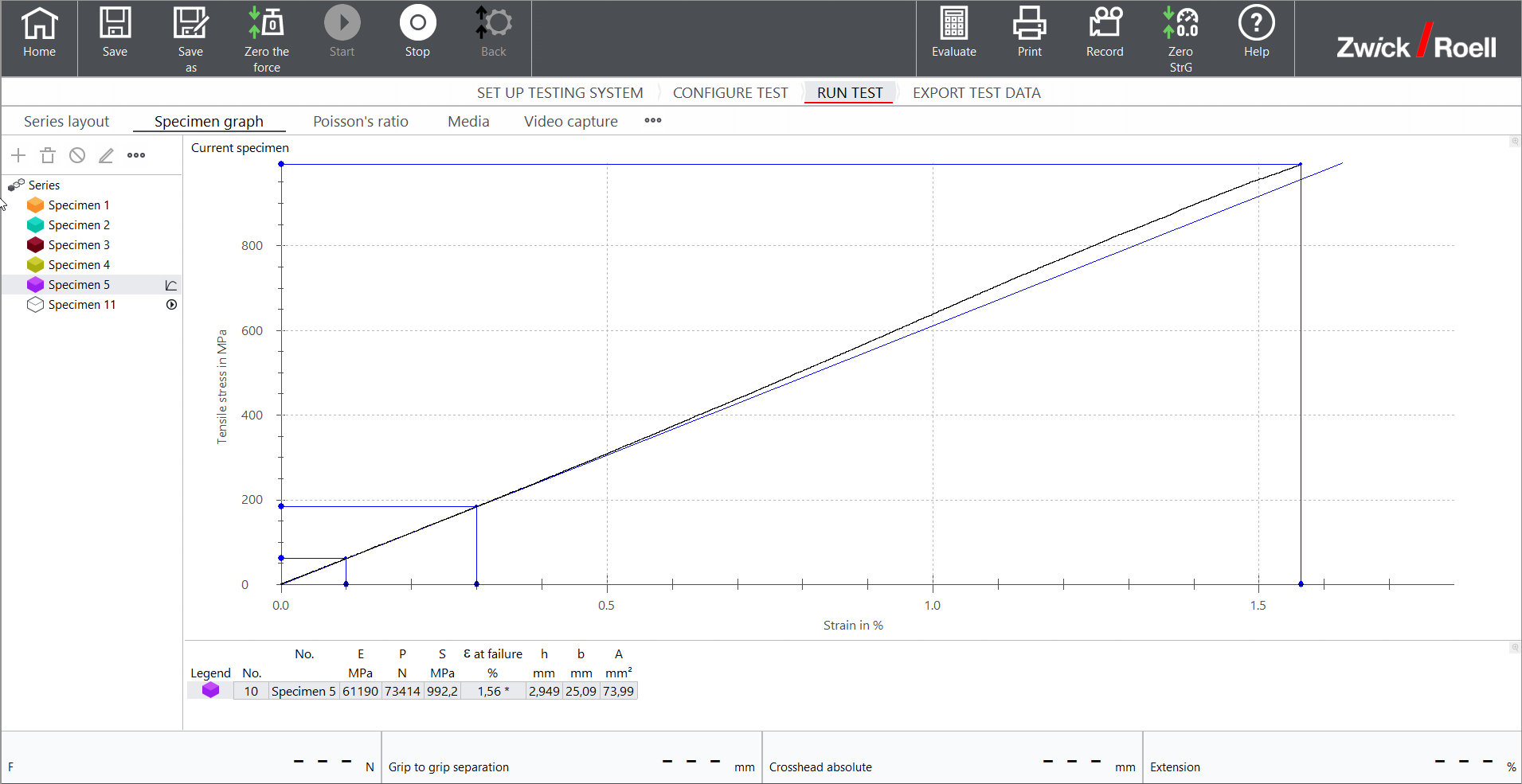
Specimen grips and alignment fixture for reliable test results to ASTM D3039
To perform the tensile test to ASTM D3039, the corresponding tensile specimen is gripped in the specimen grips of a static testing machine. It is recommended to regularly check for correct specimen grip alignment according to ASTM E1012. For Nadcap accredited testing laboratories in the aerospace industry, alignment verification is mandatory.
Mechanical body-over-wedge or hydraulic body-over-wedge grips are ideally suited for this requirement. If proof of alignment is not required, conditionally alignable wedge screw grips can also be used.
Modular testing system for composites
Larger testing laboratories with correspondingly high test volume use different testing machines for the very diverse composite testing methods, and can thereby minimize conversion efforts. The individual testing machines can be adjusted to the force range required for the various types of tests. If throughput rates are not high or consistent enough that an investment in multiple testing machines makes sense, an alternative option is to equip a single testing machine so that you can perform as many test methods as possible with the least amount of machine conversion effort.
ZwickRoell developed a modular design, which is available as a 100 kN or 250 kN testing machine covering 21 test methods and approximately 120 test standards (ISO, EN, ASTM, as well as Airbus AITM and Boeing BSS), and which allows for comprehensive characterization of fiber-reinforced composite materials at ambient temperature or for tests at low or high temperatures ranging from -80 °C to +360 °C.
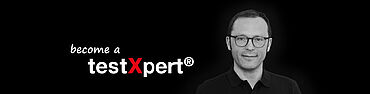
testXpert testing software: guaranteed reliable testing to ASTM 3039
Efficient testing and reliable test results to ASTM D3039 are easy to achieve with our testXpert testing software:
- Save yourself the time needed to work through the standards: our standard test program meets ASTM D3039, guaranteed. All required characteristic values and parameters specified in ASTM D3039 are already pre-configured in the test program.
- Connecting peripheral devices increases your level of efficiency even further: the specimen dimensions are sent directly from the micrometer to the testing software, saving you time and preventing input errors.
- The temperature chamber is also conveniently integrated in the testing software: check and control the temperature in the chamber, set temperature ramps and see the values that have been maintained retrospectively, with traceability.
Tensile testing machines for ASTM 3039
For tensile tests to ASTM D3039 with standard specimens and for many other standardized test methods for fiber-reinforced plastics, use of a 100 kN testing machine is often sufficient. With the 100 kN machine configuration shown on the right, the use of mechanical body-over-wedge grips makes it easy to switch between different test arrangements and test fixtures. Because the specimen grips are easy to remove, the entire work area of the testing machine can also be used for non-standard tests. The support legs enable individual and ergonomic adjustment of the work area height.
If testing is performed exclusively on glass fiber-reinforced plastics (GFRP), a static machine with a maximum force of 50 kN is normally sufficient.
Extensometers for strain measurement to ASTM D3039
For correct determination of the elastic characteristic values and strain at break, it is necessary to measure strain directly on the specimen. To determine the Young's modulus and strain at break, measurement of the axial strain is sufficient. To additionally determine Poisson’s ratio, a biaxial strain measurement system is required, which also allows you to measure transverse strain. For the strain measurement you can use strain gauges, sensor-arm measuring systems such as clip-on extensometers (limitation: not up to specimen break) or automatic sensor arm extensometers (makroXtens, multiXtens) as well as non-contact optical systems (videoXtens).
ASTM D3039 test conditions
Test speed
ASTM D3039 states two options for setting the test speed.
One is by setting a constant strain rate of 0.01 min-1 (nominal value). And alternatively, the test can be performed at a constant speed of 2mm/min (nominal value).
- Valid specimen failure
For the documentation of specimen failure, ASTM D3039 provides a 3-letter code that uniquely defines the failure mode and position along the gripped specimen. Failure is considered invalid when the break occurs in the jaws, in the transition area or within a distance equal to one specimen width from the jaws. However, straight 0° UD tensile tests often show a high-energy, explosive failure in which the entire free (ungripped) area of the specimen shatters. This failure is therefore usually classified as a valid failure.
Temperature range
Since the mechanical properties of fiber-reinforced plastics can be largely temperature dependent, in addition to tensile tests at ambient temperature, tests are also performed at low and elevated temperatures. Here, the testing machine can be equipped with a temperature chamber for a temperature range of -80 °C to 360 °C.
Specimens and dimensions in accordance with ASTM D3039
Specimen type / laminate | Schematic diagram of the specimen shape (simplified, not to scale) | Note on the use of adhesively bonded tabs |
---|---|---|
0° UD laminate | ![]() |
|
90° UD laminate | ![]() |
|
Multidirectional UD and woven laminates, discontinuous fiber-reinforced laminates with random fiber orientation (e.g. SMC) | ![]() | For multidirectional UD or woven laminates, or for specimens made of discontinuous fiber-reinforced laminates with random fiber orientation, the use of abrasive cloth instead of bonded force application elements is often sufficient |
- Bonded force application elements (adhesively bonded tabs) are not required, but are strongly recommended for UD laminates, to prevent invalid jaw breaks (break at or in the jaws).
- Glass fiber reinforced plastic (GFRP) laminate with a fiber orientation of ±45° with respect to the load direction in the tensile specimen has proven to be a suitable tab material.
- The specifications in ASTM D3039 for the specimen geometry of the respective laminate types are recommendations and allow results to be compared between laboratories. Deviations in specimen dimensions are permitted provided that general recommendations for specimen geometry provided by the standard are observed.
- When using either sensor arm or non-contact strain measurement systems, the gauge length L0 should be between 10 and 50 mm.
Additional information on ASTM D3039
- With the ASTM D3039 standard, both the International System of Units (SI) as well as the inch-pound (Imperial) system of units can be used for test parameters and specimen dimensions. However, it is important to avoid a mix of the two unit systems, as this can lead to non-standard compliant results.
- To determine tensile properties at the single-layer level, multilayer composites are produced in which each individual layer is oriented in the same way. This especially applies to 0° or 90° UD laminates. In the case of correspondingly oriented multilayer woven composites, mechanical characteristic values are also referenced in terms of warp and weft direction.
- In addition to performing tensile tests for material development, material qualification and quality assurance purposes, the characteristic values determined at the single-layer level are also used in the design of composite structures for analytical calculation methods. Using the classical laminate theory, for example, the elastic properties of a multidirectional multilayer composite can be calculated from the characteristic values of the respective individual layers. The strength values at the single-layer level are used, among other things, for the calculation of failure criteria such as maximum stress, Hashin, Puck or LaRC.
- Since the mechanical properties of a multilayer composite depend on the orientation of the respective individual layers, every multilayer composite with different individual-layer orientations presents different mechanical tensile properties. The mechanical material properties of fiber-reinforced plastics therefore only come to light during the manufacturing process of the laminate. The manufacturing process itself has a significant influence on the resulting characteristic values. The influence of the manufacturing process on the mechanical properties of a fiber-reinforced plastic (FRP) laminate is therefore often validated by mechanical testing.
Frequently asked questions about composite testing to ASTM D3039
ASTM D638 is the standard test method for the determination of tensile properties of unreinforced and reinforced plastics using dumbbell specimens. When continuous fibers or discontinuous fibers with a modulus of >20 GPa are used for reinforcement, ASTM D638 refers to the ASTM D3039 standard test method for determination of the tensile properties of polymer matrix composites. Rectangular specimens are used for ASTM D3039. Tensile tests on carbon or glass fiber reinforced plastics (CFRP, GFRP) with continuous fibers in particular, achieve significantly higher test forces compared to tensile tests on unreinforced or short fiber reinforced plastics, which requires the use of a suitable testing machine.
ASTM D3039 is a standard test method for determination of the tensile properties of fiber-reinforced composites. The high-modulus reinforcing fibers can be continuous fibers or discontinuous fibers with random fiber orientation. The recommended dimensions of the rectangular specimen in ASTM D3039 depend on the type of composite laminate to be tested (e.g., 0° unidirectional, 90° unidirectional, multidirectional or randomly discontinuous).
The specimen thickness for ASTM D3039 depends on the type of laminate for which the tensile properties are to be determined. ASTM D3039 recommends a specimen thickness of 1 mm for 0° unidirectional (UD) and 2 mm for 90° UD tensile tests. For multidirectional laminates or for laminates with randomly discontinuous fiber orientation, the recommended thickness is 2.5 mm. Corresponding recommendations in terms of overall length, width, tab length and tab thickness for the specimens are also made.