Low Cycle Fatigue (LCF) Tests to ISO 12106 / ASTM E606
Low cycle fatigue means fatigue at a low number of cycles.
The low cycle fatigue (LCF) test to ISO 12106 and ASTM E606 is a fatigue test in which a cyclic load is simulated until failure. The test is typically performed using a servohydraulic testing machine.
Materials that are subjected to extreme thermal and mechanical loads can only be designed within the range of their low cycle fatigue, i.e. up to a maximum of 105 load changes. Prime examples include turbine blades and discs used in aircraft engines and stationary turbines for power-generation. In addition the LCF test is used on exhaust gas turbochargers, exhaust manifolds and other similar components. In these components, designed notches (e.g. blade-disc connections) are subjected to strain-induced plastic cyclic deformation, which sooner or later leads to cracking. In a low-cycle fatigue (LCF) test these loads are simulated on a specimen and the number of cycles to crack initiation is determined. The test is normally performed at elevated temperatures. The test frequency is typically between 0.01 and 5 Hz.
Especially required for this are the testing machine and the machine controller. In the transition from elastic to plastic deformation, the stiffness of the specimen changes dramatically and the controller must react very quickly to, for example guarantee a constant strain increase rate. Here, very high stiffness of the testing machine plays an imperative role.
Standards Video Loading Test procedure Cyclic hardening Cyclic softening End of test Testing machines Testing software Other tests
Loading in the Low Cycle Fatigue Test
Loading in low cycle fatigue tests comprises an elastic Ɛa,e and a plastic Ɛa,p strain proportion: Ɛa,t = Ɛa,e + Ɛa,p
While a linear relationship exists between stress and strain in the elastic range (Hooke's law), this relationship is non-linear in the plastic range. This results in a hysteresis loop.
Low cycle fatigue tests to ISO 12106 / ASTM E606 are run at constant amplitude. In addition, hold times can be introduced to examine creep/relaxation processes. A triangular waveform is used as set value, or a trapezoidal wave for hold times.
If specific operating loads are to be simulated, other strain-time sequences are also possible. Thus low cycle fatigue tests are also performed with a superimposed higher-frequency oscillation.
The test frequency is usually lower than / equal to 1 Hz, although this limit is constantly shifting upwards with the result that LCF tests are being performed at up to 10 Hz.
Strain control is used for these LCF tests. Only in special cases is there a change to force-control in the stabilized hysteresis range or for hold times in order to investigate creep tests. For materials characterization, the tests are usually performed at an RƐ ratio of -1.
Low Cycle Fatigue Test Procedure
Following careful installation, the specimen is heated to the test temperature. For this the machine is in force-control mode, with set value of 0 kN. Once the required temperature has been reached, the extensometer is attached. If the extensometer was already on the specimen during the heating phase, allowance must be given for a change in L0. Strain control is now selected and the test started.
The initial cycles are of particular importance as materials may display strongly differing behavior at this point.
However, a stabilized hysteresis is generally established after a number of cycles. There are also many materials which exhibit neither hardening nor softening
End of Test
The end of the test low cycle fatigue is usually defined as a percentage force-reduction of the regression line of the stabilized hysteresis.
Because of this material behavior it is important to record every hysteresis loop at the beginning. In the stabilized range it is sufficient to store, for example every hundredth or thousandth. Often a logarithmic interval is selected and a percentage change in force is additionally defined as a criterion for storing a loop. Towards the end of the test every cycle should once again be recorded.
Our testing software for low cycle fatigue tests
testXpert R testing software is used for the strain-controlled determination of low cycle fatigue strengthon metals to ASTM E606. The set value is generally a triangular waveform with constant amplitude. Sine signals are also possible.
A suitable extensometer is required for strain control. The test is generally performed at elevated temperature.
Due to differing material behavior, softening or hardening, it is important for all hysteresis loops to be recorded at the beginning. The number of loops can be freely defined by the user.
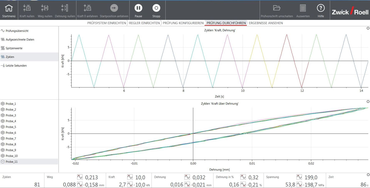