Steering Testing
Steering systems are subject to high dynamic loads during driving – their components must function reliably in order to ensure safety and driving comfort. Steering linkages, steering shafts, and rubber-metal dampers, which play a central role as links between the driver and the chassis, are particularly important. ZwickRoell offers individually adaptable test benches with which mechanical, dynamic, and tribological properties can be tested under realistic conditions, both in development and in series production.
Learn more about testing
Steering linkages Steering shafts Steering columns Rubber-metal dampers Request a consultation Downloads
Testing of steering linkages
The horizontal tensile/compression/torsion testing machine can be used to determine the frictional forces and frictional torques, including the stick-slip effect, inside and outside the test axis of a steering linkage in the installation position:
Separately controlled drive axes:
- 1 Tension / compression test axis (axial) up to 20 kN, adjustable
- 2 Torsion drive up to 100 Nm
- 3 Tension / compression test axis (lateral) up to 1 kN
Different steering linkage designs can be optimally tested with three manually adjustable axes for alignment and enable the implementation of a wide variety of test sequences:
- 4Axial position of the lateral force
- 5Vertical position of passive gripping
- 6 Horizontal position of passive gripping
The three axes are controlled by the testXpert testing software. The universal table with perforated plate helps to secure the fixtures. The testing system has a CE-compliant safety housing.
Steering Shaft Testing
To facilitate automated production of telescopic steering shafts for trucks, ZwickRoell testing machines can be integrated into a fully-automated assembly line.
- A testing machine is used to determine the maximum torsion angle in the middle of the production process, allowing process-oriented analysis of the previous assembly steps. A special angle transducer was developed for the high precision requirements of relative torsion angle measurement.
- A second testing machine is placed at the end of the production line to determine the displacement force of the steering spindle.
Testing of Steering Columns
In order to reliably test steering column height adjustment, the testing system must simulate the height adjustment process realistically. For this, an electromechanical testing actuator is ideal since it can be positioned flexibly in order to axially apply the desired loads to the steering column. In the example shown, height adjustment is activated in several thousand cycles in order to uncover weaknesses that would normally only become apparent over the course of the component's life.
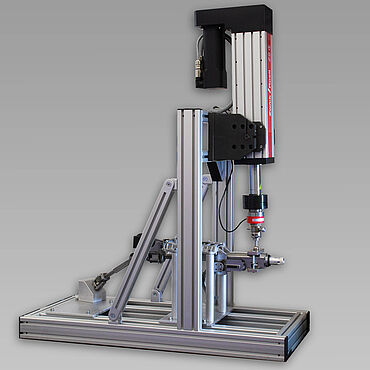
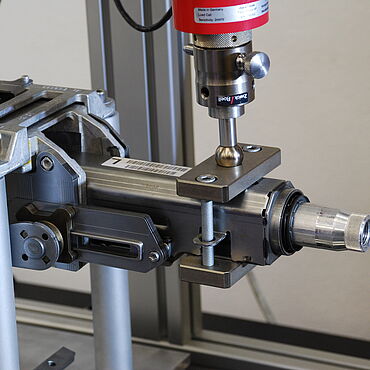
Testing of rubber-metal dampers
A testing system based on a servohydraulic testing machine was developed to determine, among other things, the quasi-static and dynamic stiffness and the loss angle and loss factor of rubber-metal bearings. In addition, the system is equipped with a safety light curtain and supplementary two-handed control. The test result is displayed via a red/green digital tolerance indicator, with an audible prompt via an electronic buzzer, allowing the operator to attend to other tasks during the test. Parameterization of the test sequence, as well as results evaluation and display, are handled by ZwickRoell’s field-proven testXpert testing software.
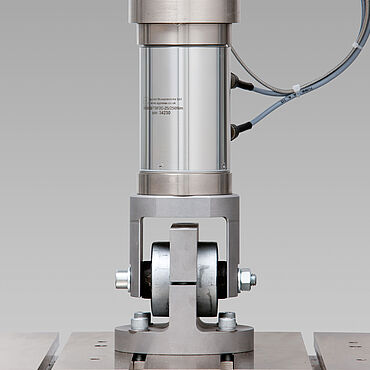
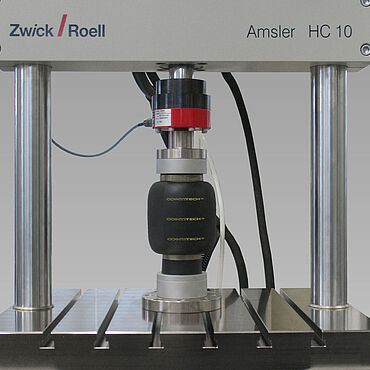
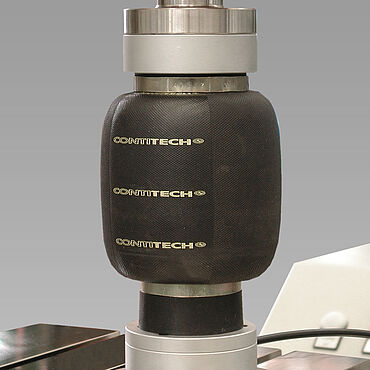