Servohydraulic load frames
Download- 10 kN - 25 kN (HC)
- 50 kN - 500 kN (HA)
- 50 kN - 2,500 kN (HB)
- Fatigue
- Fracture mechanics
- LCF
- ISO 12106
- ASTM E606
- DIN 50100
- ASTM E399
- ASTM E647
- ASTM E466
Servohydraulic load frames
The load frames of ZwickRoell’s servohydraulic testing machines have been specially designed for specific fatigue testing requirements, which is reflected in their high frame stiffness, among other things. They are used to determine material characteristic values under vibrating loads, including S-N tests (high cycle fatigue tests), LCF tests (low cycle fatigue) or fracture mechanics tests.
Depending on testing requirements and the need for ergonomic working conditions in everyday tests, the testing actuator is mounted either above or below the test area.
A separate hydraulic power pack is required for the servohydraulic load frames. ZwickRoell offers hydraulic power packs with different power levels, allowing the servohydraulic load frames to be adapted to specific customer requirements.
HC series up to 25 kN HA series up to 500 kN HB series up to 2,500 kN
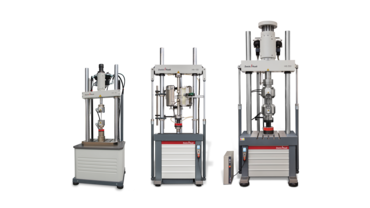
HC series up to 25 kN
While the load frames of the HA and HB series are floor-standing, allowing equipment assembly at an optimum operating height, the servohydraulic load frames of the HC series, both 10 kN and 25 kN, are table-top models. A matching concrete base ensures ergonomic working height.
In the servohydraulic HC table-top load frame, the testing actuator is located above the test area. The hard-chromed T-slot platform in the test area as well as the columns of the test frame are suited for testing under corrosive media.
An optional hydraulic adjustment facilitates the positioning of the upper crosshead.
HA series up to 500 kN
The HA series servohydraulic load frames are available in standard versions (Fmax) 50 kN, 100 kN, 250 kN and 500 kN.
With the testing actuator mounted in the lower crosshead, the HA series represents the typical servohydraulic testing machine used for determining material properties under cyclic loading. It is particularly suitable for tests requiring the use of temperature chambers or high-temperature furnaces.
The upper crosshead is adjustable, with optional hydraulic crosshead clamping and lift cylinders. The testing actuator stroke is 100 mm or 250 mm. The servohydraulic testing machine can be supplied for 210 bar or 280 bar system pressure.
HB series up to 2,500 kN
The HB series servohydraulic load frames are available in standard versions (Fmax) 50 kN, 100 kN, 250 kN, 500 kN, 1,000 kN and 2,500 kN.
In the HB series, the testing actuator is located above the test area. These machines are particularly versatile. The version with integrated T-slotted platform allows flexure tests and component testing to be performed in addition to standard high cycle fatigue tests. The load cell can be mounted on the lower crosshead or directly onto the piston rod, depending on the application.
A wide range of accessories, including hydraulic grips, compression platens, flexure test kits, and more, complete the system.
Videos on servohydraulic load frames
HB-series: Fatigue test
Technical overview
HA series | HB series | HC series | |
---|---|---|---|
![]() | ![]() | ![]() | |
Force levels |
|
|
|
Testing actuator | Lower crosshead | Upper crosshead | Upper crosshead |
Alignment fixture | ✓ | - | ✓ |
Temperature chamber | ✓ | - | - |
High-temperature furnace | ✓ | - | - |
T-slotted platform | - | ✓ | ✓ |
Typical Applications |
|
|
Dynamic nominal force | 50 | 100 | 250 | 500 | kN |
Crosshead clamping | Electro-hydraulic | electro-hydraulic | electro-hydraulic | electro-hydraulic | |
Crosshead adjustment | Electro-hydraulic | electro-hydraulic | electro-hydraulic | electro-hydraulic | |
A - max. height of test frame | 2750 (3250)1 | 2750 (3250)1 | 3040 (3540)1 | 3430 (3930)1 | mm |
AK – tilted dimension for erecting | 2820 (3320)1 | mm | |||
B – max. width of test frame | 1079 | 1079 | 1179 | 1525 | mm |
C – max. depth of test frame | 780 | 780 | 790 | 1390 | mm |
D1 – column spacing | 565 | 565 | 670 | 800 | mm |
E – column diameter | 80 | 80 | 100 | 120 | mm |
F – height of top edge of lower crosshead2 | 1010 | mm | |||
G – max. height of test area3 | 1450 (1950)1 | mm | |||
H – max. height of work test area4 | 1372 (1872)1 | mm | |||
J – crosshead adjustment path | 1000 (1250)1 | mm | |||
Weight5 | 920 (970)1 | kg | |||
Frame stiffness with crosshead separation 1000 mm | 673 | 673 | 967 | 2100 | kN/mm |
Suitable for actuators with maximum stroke | 250 | 150 | 150 | 100 | mm |
Item No. | |||||
Standard height | 039825 | ||||
Extra high + 500 mm | 073968 | ||||
Item Number | |||||
Standard height | 025238 | 924810 | 935267 | ||
Extra-high + 500 mm | 935832 | 073969 | 073970 | ||
AK - tilted dimension for installation | 2820 (3320)1 | 3195 (3695)1 | 3650 (4125)1 | ||
F - height of top edge of lower crosshead2 | 1010 | 1030 | 1020 | ||
G – max. test area height3 | 1450 (1950)1 | 1750 (2250)1 | 2000 (2500)1 | ||
H – max. working test area height4 | 1372 (1872)1 | 1659 (2159)1 | 1900 (2400)1 | ||
J – crosshead displacement range | 1000 (1250)1 | 1150 (1400)1 | 1250 (1400)1 | ||
Weight6 | 920 (970)1 | 1520 (1600)1 | 3600 (3720)1 |
- Variant with height increased by 500mm
- With vibration-damping feet
- Distance between upper and lower crossheads
- Distance between piston flange and upper crosshead with piston retracted
- Weight without actuator, load cell, or any tools
- Weight without actuator, load cell or any fixtures
Dynamic nominal force | 50 | 100 | 250 | 500 | kN |
Crosshead clamping | electro-hydraulic | electro-hydraulic | Electro-hydraulic | electro-hydraulic | |
Crosshead adjustment | electro-hydraulic | electro-hydraulic | Electro-hydraulic | electro-hydraulic | |
AG100 – max. test frame height with 100mm stroke actuator | 3175 (3675)1 | 3259 (3759)1 | 3523 (4023)1 | 4045 (4545)1 | mm |
AG250 – max. test frame height with 250 mm stroke actuator | 3475 (3975)1 | 3559 (4059)1 | 3823 (4323)1 | 4345 (4845)1 | mm |
AG400 – max. test frame height with 400 mm stroke actuator | - | 3859 (4359)1 | 4123 (4623)1 | 4635 (5135)1 | |
A – max. column height | 2690 (3190)1 | 2690 (3190)1 | 2900 (3400)1 | 3250 (3750)1 | mm |
AK – tilted dimension for erecting | 2820 (3320)1 | 2820 (3320)1 | 3060 (3560)1 | 3500 (3980)1 | mm |
B – max. width of test frame | 1079 | 1079 | 1197 | 1525 | mm |
C – max. depth of test frame | 780 (1020)2 | 780 (1020)2 | 1130 (1130)3 | 1130 (1370)2 | mm |
D1 – column spacing | 565 | 565 | 670 | 800 | mm |
E – column diameter | 80 | 80 | 100 | 120 | mm |
F – height of top edge of lower crosshead4 | 950 | 950 | 890 | 900 | mm |
G – max. height of test area5 | 1510 (2010)1 | 1510 (2010)1 | 1705 (2205)1 | 2120 (2620)1 | mm |
H – max. height of work test area6 | 1434 (1934)1 | 1434 (1934)1 | 1614 (2114)1 | 2020 (2520)1 | mm |
J – crosshead adjustment path | 1000 (1250)1 | 1000 (1250)1 | 1150 (1400)1 | 1250 (1400)1 | mm |
Weight without T-slotted platform7 | 899 (945)1 | 895 (941)1 | 1361 (1430)1 | 3660 (3780)1 | kg |
Weight with T-slotted platform7 | 1137 (1182)1 | 1133 (1178)1 | 2082 (2232)1 | 4860 (4980)1 | kg |
Frame stiffness with crosshead separation 1000 mm8 | 730 | 730 | 988 | 1529 | kN/mm |
Frame stiffness with crosshead separation 1000 mm3 | 870 | 870 | 1332 | 1848 | kN/mm |
Item No. | |||||
Standard height | 077533 | 924779 | 040159 | 079720 | |
Standard height with T-slotted plate | 077370 | 079752 | 040158 | 079728 | |
Extra high + 500 mm | 750972 | 077534 | 079755 | 079721 | |
Extra high +500 mm with T-slotted platform | 077535 | 079753 | 079756 | 079733 |
- Variant with height increased by 500mm
- Variant with t-slotted platform
- Version with T-slotted platform
- With vibration-damping feet
- Distance between upper and lower crossheads
- Distance between piston flange and upper crosshead with piston retracted
- Weight without actuator, load cell, or any tools
- Standard table plate
Test area height | Standard | Extended by 250 mm | Extended by 500 mm | |
Dynamic nominal force | 25 | 25 | 25 | kN |
A – max. height of test frame | 1325 | 1825 | mm | |
AG100 – max. test-frame height with 100mm-stroke actuator | 1865 | 2365 | mm | |
AG250 – max. test-frame height with 250mm-stroke actuator | 2165 | 2665 | mm | |
B – max. width of test frame | 660 | 660 | 660 | mm |
C – max. depth of test frame | 450 | 450 | 450 | mm |
D1 – distance between columns | 460 | 460 | 460 | mm |
E – column diameter | 65 | 65 | 65 | mm |
F – height of top edge of lower crosshead | 75 | 75 | 75 | mm |
G – max. test area height1 | 1070 | 1570 | mm | |
H – max. working test area height2 | 310 to 1010 | 810 to 1510 | mm | |
J – crosshead adjustment path3 | 700 | 700 | mm | |
K – weight4 | 300 | 330 | kg | |
Frame stiffness at 1000mm crosshead separation | 300 | 300 | 300 | kN/mm |
Clamping/ adjustment: manual/manual | 1037238 | 1037238 | 1037469 | |
Clamping/ adjustment: manual/hydraulic | 1036930 | 1036931 | 1037473 | |
A - max. height of test frame | 1575 | |||
AG100 – max. height of test frame with 100 mm stroke actuator | 2115 | |||
AG250 – max. height of test frame with 250 mm stroke actuator | 2415 | |||
G – max. height of test area1 | 1320 | |||
H – max. height of work test area5 | 560 ... 1260 | |||
J – crosshead adjustment path6 | 700 | |||
K – weight7 | 315 | |||
Clamping/Adjustment: manual/manual | 1037462 |
- Distance between upper and lower crossheads
- Distance between piston flange and base crosshead with piston retracted
- For frames with hydraulic adjustment only
- Weight without actuator, load cell, or any fixtures
- Distance between piston flange and lower crosshead with piston retracted
- Only for frames with hydraulic adjustment
- Weight without actuator, load cell, or any tools
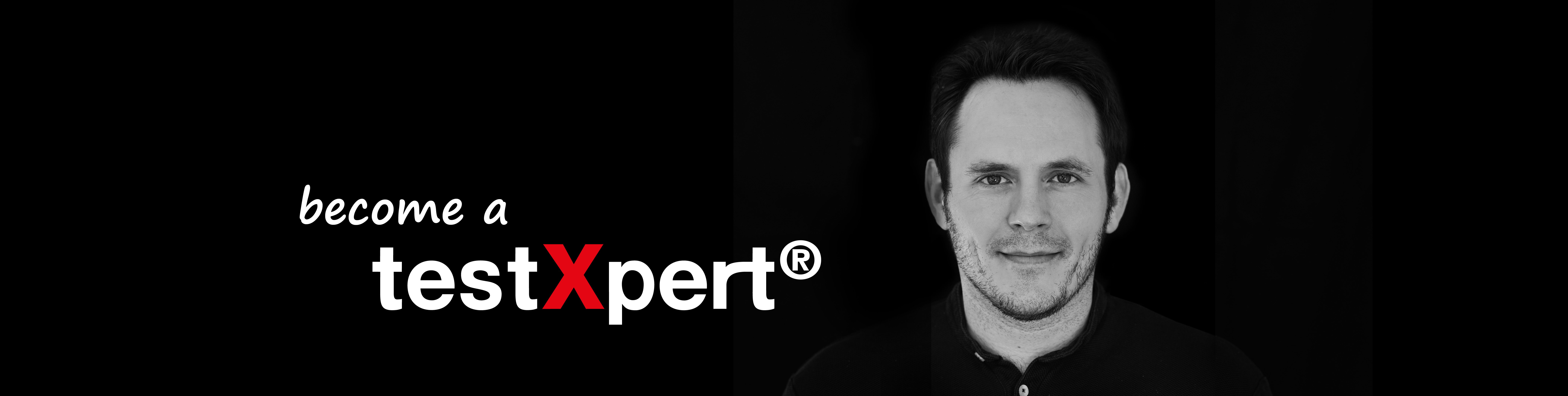
testXpert R – our software for dynamic testing
testXpert R is used with servohydraulic testing machines, vibrophores and electrodynamic testing machines. The testing software offers the right test programs for fatigue tests, fracture mechanics, low cycle fatigue (LCF). A graphical block editor is available for free test configurations, where up to 100 blocks can be parameterized.
Downloads
- Product Information: HA series servohydraulic testing machine PDF 398 KB
- Product Information: Hydraulic Distribution Unit PDF 396 KB
- Product Information: HB series servohydraulic testing machine PDF 378 KB
- Product Information: HC series servohydraulic testing machine PDF 293 KB
- Product Information: Hydrostatic single testing actuator 10-50 kN PDF 540 KB
- Product Information: Hydrostatic single testing actuator 100-1000 kN PDF 480 KB
- Product Information: 20 l/min. hydraulic power pack PDF 567 KB
- Product Information: 40 l/min. hydraulic power pack PDF 567 KB
- Product Information: 80 l/min. hydraulic power pack PDF 598 KB
- Product Information: 170 l/min. hydraulic power pack PDF 391 KB
- Product Brochure: Dynamic and Fatigue Testing Systems PDF 5 MB