ISO 179-1 | ISO 179-2 Charpy impact and notched impact strength of plastics
The standards ISO 179-1 (non-instrumented impact strength test) and ISO 179-2 (instrumented impact strength test) describe the Charpy impact test for determination of the impact characteristics (impact strength and notched impact strength) of plastics. Impact tests to Charpy are also described in the ASTM D6110 standard.
Impact tests according to the Charpy method are used for the characterization of a plastic material at high strain rates. The abrupt load is applied in a 3-point flexure fixture. In the classic method, the result is presented in terms of the energy absorption of the specimen. Instrumented measurement methods furthermore present force-travel diagrams, provide additional material information, as well as automatic assignment of the break type.
In the context of the standard for single-point data ISO 10350-1, Charpy according to ISO 179-1 is the preferred test method for the measurement of impact strength. The test is ideally performed on unnotched specimens with edgewise impact (1eU). If the specimen does not break in this configuration, the test is performed using notched specimens. The test results are therefore not directly comparable. If specimen break can also not be achieved with notched specimens, the tensile impact method to ISO 8256 is used.
Objective & applications Test / test equipment requirements Video Testing sytems Plastics brochure
Objectives of Charpy impact tests
The Charpy impact and notched impact test to ISO 179-1 and ISO 179-2 provide characteristic values for impact strength at high strain rates in the form of an area-related energy value. The tests are normally performed in normal climate or at low temperatures.
Applications include:
- The comparison of different molding materials
- Creation of material cards, e.g. to ISO 10350-1
- Tolerance monitoring within the scope of goods inwards checks and quality assurance
- Testing of finished parts based on machined specimens
- Measurement of aging effects
- Fracture mechanics testing
In contrast to the Izod test, the Charpy test has a broader range of application and is better suited to test materials displaying interlaminar shear fractures or surface effects.
In addition, the Charpy method offers advantages when testing at low temperatures. Since the specimen supports are further away from the notch, rapid heat transfer to the critical areas of the specimen is avoided, simplifying the cooling process in an external cooling device and subsequent feeding into the testing instrument.
Non-instrumented Charpy impact test ISO 179-1
- Pendulum impact testers, which are specified in detail in the ISO 13802 standard, are used for conventional, non-instrumented Charpy impact tests to ISO 179-1. This supports a strong level of reproducibility of tests performed using different types of test equipment and different laboratories, operators and locations.
- The measurement principle is based on a pendulum hammer with specified energy capacity and drop height, which releases part of its kinetic energy when it penetrates the specimen. As a result, the pendulum hammer does not return to the original drop height after the impact. The measured height difference between drop height and height of rise therefore becomes a measure of the energy absorbed. By determining the drop height, the impact velocity is also defined so that the tests are performed with reproducible strain rates.
- Each pendulum hammer may be used in a range of 10% to 80% of its initial potential energy. If several pendulum hammers meet this condition for testing a material, which is usually the case from the overlapping working ranges of the various pendulum hammers, the pendulum hammer with the greatest initial potential energy is used. This ensures that the reduction in speed during the impact process is minimized.
- The type of measurement implies that all energy losses are attributable to the specimen. It is therefore important to minimize, correct, or completely eliminate all external sources for error. There are strict specifications in ISO 13802, as well as checks that are part of regular calibrations, regarding friction losses that inevitably occur due to air friction and friction at the bearing points of the pendulum hammer. The correction values are measured and assigned to the respective pendulum hammer. Sufficient mass and a vibration-free installation of the pendulum impact tester on a very stable laboratory table, on a worktop bolted into a solid wall, or a masonry platform are essential for the quality of the measurement. Internal vibrations in the instrument are minimized by design. ZwickRoell uses pendulum hammers with double rods made of unidirectional carbon materials, which are very low in mass and at the same time offer optimum stiffness of the pendulum rods.
Instrumented Charpy impact test ISO 179-2
By plotting the force time sequence, a force time diagram with excellent accuracy can be achieved through double integration using high-quality measurement technology. The acquired data can be used in a variety of ways:
- Additional characteristic values that enhance the understanding of material behavior
- Fracture mechanical characteristic values
- Automatic, operator-independent determination of the type of break using the curve progression in the force travel diagram
The measured value curves always show characteristic fluctuations. These are specimen fluctuations with frequencies that are correlated in a defined, functional way to the specimen geometry, the dimensions, and the modulus value of the polymer.
An additional significant advantage of the instrumented Charpy impact test to ISO 179-2 is the large measurement range. In contrast to conventional pendulum impact testers, forces are measured instead of energy. Since the measurement electronics allow for precise measurements as low as 1/100 of the nominal force, the lower end of the measurable impact energy is usually determined by the duration of the test and by the natural frequency of the measuring elements. For this reason, it is possible to cover the entire measurement range described in ISO 179-2 with two instrumented pendulum hammers: an instrumented 5 J pendulum for impact velocities of 2.9 m/s and a 50 J pendulum for an impact velocity of 3.5 m/s. Following this method, Izod tests and tensile impact tests are also instrumented.
Video: Pendulum Impact Testers for Plastics Testing
ZwickRoell’s HIT series pendulum impact testers for the plastics industry offer a high-precision, cost effective solution. The pendulum impact testers are available from 5 to 50 joules and not only enable Charpy impact tests to be carried out in accordance with ISO 179-1 / ISO 197-2 and ASTM D6110, but also Izod, Dynstat and tensile impact tests in accordance with ASTM, ISO and DIN.
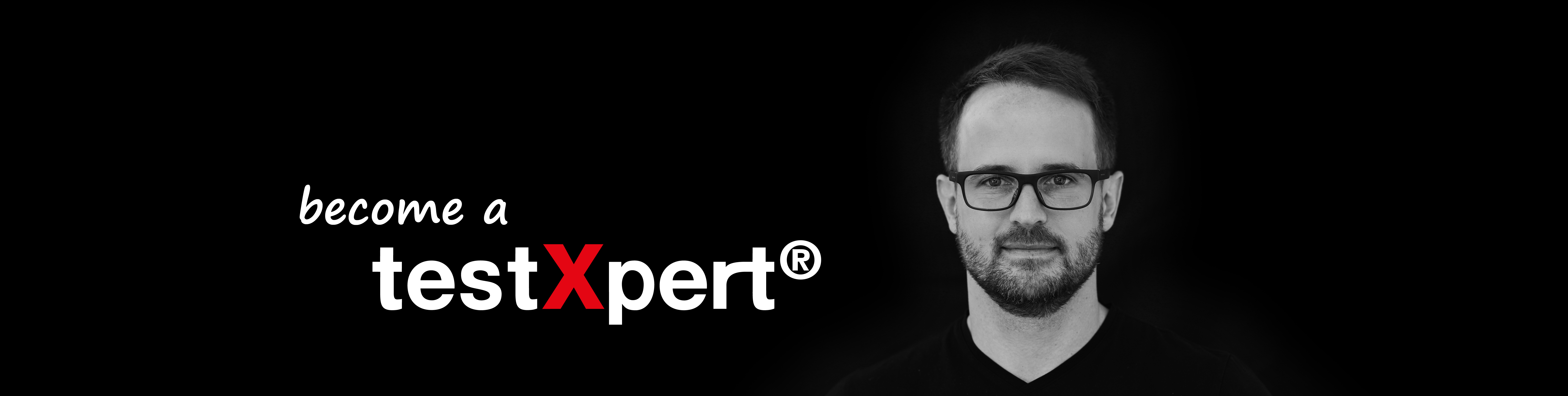
Optimal integration of the test to ISO 179 through our testXpert testing software
One testing software solution for everything: impact strength testing to ISO 179, tensile testing, flexure testing, melt flow testing. And all the data can be evaluated together.
- Numerous import and export possibilities ensure ideal integration of testXpert and ISO 179 impact testing into your processes. The testing software automatically reads data in and out of other systems, for example, your company’s own ERP or LIMS.
- The measurement of specimen dimensions to ISO 179 is integrated: During the measurement, the remaining width, height and width of the specimen are transmitted from the measuring device to testXpert at the touch of a button.
- All characteristic values obtained from the impact strength test to ISO 179, the tensile test, the flexure test and the melt flow test are stored together in one database. The test data is easy to find, evaluate and reproduce—across all applications. Access is easy via web browser from any location that's convenient for you.
- Our Trend Analysis feature provides a statistical process control (SPC) chart that allows you to detect possible deviations from quality specifications in a timely manner.
Automated Charpy impact tests
Automated Charpy impact tests on plastics are particularly useful when testing a large number of specimens.
The robot removes a single specimen and places it in the temperature chamber. Once the required temperature has been reached, the robot places the specimen in the pendulum impact tester, where it is gripped, and the automated Charpy impact test is performed.
To meet the ISO 180 (Izod), ASTM D256 (Izod) and ISO 179 (Charpy) standards, ZwickRoell offers three pendulum impact testers.