ISO 1133 melt flow index testing plastics
Extrusion plastometers provide standard values for the melt flow index (MFR) and volume flow index (MVR) of filled and unfilled thermoplastics according to ISO 1133-1and ISO 1133-2, ASTM D1238 and other similar standards.
The ISO 1133-1 standard establishes the general test method for determination of melt mass-flow rates (MFR) and melt volume-flow rates (MVR) of thermoplastics. Part 2 of ISO 1133 (ISO 1133-2) describes the method for materials that are sensitive to time- or temperature-dependent history and/or humidity.
ISO 1133-1 test method ISO 1133-2 Videos Test and test equipment requirements Extrusion plastometers Request consultation
ISO 1133-2 Testing Moisture-Sensitive and Time Dependent Polymer Melts
Special precautions must be taken for tests performed on these materials (for example, PBT, PET, or PA). First, these materials must be sufficiently dried and must be dry when poured into the extrusion barrel. An optional nitrogen blanket at the extrusion barrel prevents direct contact by the material with the ambient air. The test is run in defined time sequences and they are recorded by the software. The extrusion plastometers must meet specific conditions for this purpose in terms of spatial and temporal temperature distribution in the extrusion barrel.
Intrinsic viscosity: Correlation of IV measurements for the MFR value for linear PET
The molecular weight of polyethylene terephthalate (PET) is usually described in terms of intrinsic viscosity. This is the IV value in dl/g. The longer the polymer chains, the higher this characteristic value. This makes it possible to demonstrate molecular chains and how they can occur when moisture that is too high during the melting process.
The disadvantages of this method are that recyclers of PET in particular, are often not equipped to handle corrosive or toxic solvents. Furthermore, the fact that the test lasts a long time poses a practical problem. Therefore, measurement of the melt mass flow rate (MFR) has been used since the early 1990s in this area as well.
Using testXpert III to control the Mflow and Aflow extrusion plastometers makes it possible to determine the correlation between IV values and the MFR by means of pre-measurements, which can then be applied to following measurements.
Videos showing the determination of MFR and MVR to ISO 1133
ISO 1133 with Aflow extrusion plastometer
Test requirements / test equipment to ISO 1133
The flow property of a thermoplastic material is characterize by its melt flow index. Depending on the test method, either the mass per unit time (MFR measurement) or volume per unit time (MVR measurement) is determined. ZwickRoell offers various melt flow index testers for the determination of melt flow rates. Our portfolio includes the manually operated, compact Cflow instrument, the modular Mflow with traditional weights, and the Aflow, a fully automated all around testing solution with electromechanical force control. The latter was developed for particularly high specimen volumes and is designed for the determination of volume and mass flow rates according to methods A, B, C and D. Supports all common standards and methods to ISO 1133 and ASTM D1238 and ASTM D3364.
One of the key functions of the Mflow and Aflow is the detection of possible air pockets in the plastic melted mass, which temporarily increase the piston speed and lead to incorrect flow rates. With high-resolution travel and time measurement of the ZwickRoell instruments, changes in piston speed are automatically detected. This gives you the option to exclude certain measuring sections to avoid errors in the flow rate calculation. The user is also supported by the APC (adaptive process control) function, which measures the speed of the piston shortly before the actual measurement begins. Based on this data, the system then selects the best control options—travel distance or time based control—and thus sets the optimal measuring interval for the MVR value to be expected.
The intuitive and workflow oriented touch operation allows the user to easily switch between the instrument and the PC. The melting process and the material behavior during the measurement can be observed live directly on the instrument and through the ZwickRoell testXpert testing software.
Test sequence according to MFR or MVR value specification with testing instruments from ZwickRoell
Specify the set values. The instrument takes care of the rest!
- Instead of the usual, parameter-based programming of the preheating phase and measurement, the complete test sequence for the Mflow and Aflow series extrusion plastometers can be defined by specifying a melt index value.
- Based on this specified value, a specimen weight between 3 g and 8 g is used. To simplify daily laboratory operations, it is also normally possible to work with a weighed-in amount of 5 g, which allows you to measure a wide MFR range.
- During the preheating phase, the instrument is optimally controlled based on the available equipment. With the automatic weight lifting unit, the test weight can be reduced in phases. A retaining latch or automatic die plug provide further control options for low-viscosity polymers.
- With the flow rate available shortly before the start of the measurement phase, the instrument applies its APC (adaptive process control) function to decide how the measurement must be performed in accordance with the standard.
- The parameters to be entered by the user are therefore limited to the test temperature, the test weight, the specified MVR or MFR value, and possibly an indication of the melt density of the respective polymer.
APC function – always the right test sequence in accordance with ISO 1133-1 or ISO 1133-2
When measuring flow rates, measurement intervals must be set so that the measurement times are as great as possible, and in the case of MVR measurement, the measurement travel is as great as possible. This makes the method highly accurate. When outside of the optimal range, the number of measurement errors increases rapidly.
The Mflow and Aflow series extrusion plastometers are equipped with an APC (adaptive process control) function. This function measures the speed of the piston shortly before actual measurement begins. Using this information, the preferred type of control—either travel or time control—is selected and set to the optimal measurement interval for the expected MVR value. Time-consuming pretests are no longer necessary and the process required for programming tests is reduced to setting a few test parameters that apply to all materials to be tested.
Aflow extrusion plastometer – simply add the material and start the test!
- The general function of force controlled extrusion plastometers, such as the Aflow model from ZwickRoell, is similar to a capillary rheometer and they feature a significantly wider range of control options.
- For example, laboratory personnel may agree to use a test sample weight of 5 g for all MFR values above 0.1 g/10 min. In many cases, this amount of material can be easily taken from a container by simply using the appropriate measuring scoop size.
- The instrument detects the fill level in the barrel right at the start of the test and can estimate the order of magnitude of the melt volume-flow rate of the polymer early in the preheating phase. Based on this information, the instrument continuously calculates the ideal actuation position—in compliance with ISO 1133-1 or 1133-2—from which the piston must move freely under test load until the measurement starts. With the flow rate present just before the measurement window is reached, the Aflow decides how to perform the measurement in accordance with the standard.
- For the operator this means that they simply have to fill 5 g of material into the extrusion barrel, start the test and rely on the fact that the test is running according to standard and with optimal test parameters. The laboratory manager no longer needs a list with the necessary parameter settings for each polymer grade and can rest assured that operators have run the test correctly. The auditor benefits as well. They no longer have to question how the lab ensures that every measurement on every polymer grade has been performed correctly.
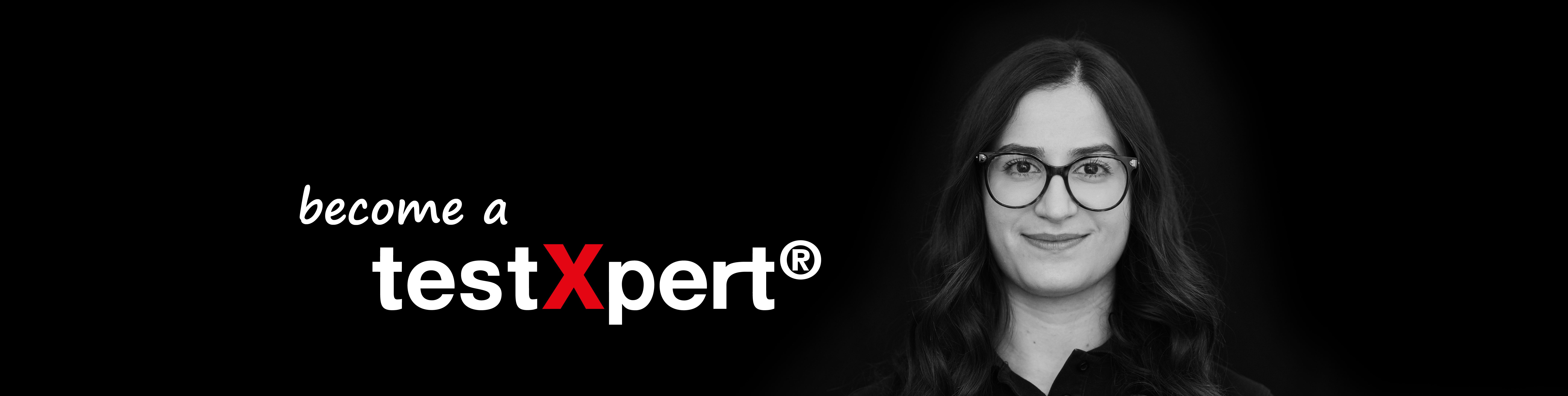
Simple testing according to ISO 1133 with testXpert
The testXpert testing software makes melt flow testing to ISO 1133 simple, despite the many parameters specified by the standard.
- The standard test program according to ISO 1133 includes the specifications defined by the standard. It allows you to test at 100% standard compliance without having to worry about anything.
- testXpert guides you through the test, step by step, making onboarding of new employees fast and easy. With our user management feature you only see the tasks are that relevant to your responsibilities.
- The analytical balance automatically transmits the weight of the individual sections to testXpert without error.
- With the Test Data Management feature included in testXpert Analytics, you have the ability to evaluate cross-application values. Contrast the melt flow index and volume flow index according to ISO 1133 with other values, for example tensile modulus, flexural modulus, tensile strength or notched impact strength.
- The simple longterm evaluation option of our Trend Analysis feature recognizes deviations in the quality specifications and supports you in optimizing your processes.