ASTM D1238 Melt Flow Rate Determination on Plastics
ASTM D1238 describes the melt flow rate determination (melt mass-flow rate (MFR), melt volume-flow rate (MVR) and flow rate ratio (FRR)) on unfilled or filled thermoplastic melted mass. Additional requirements for measurements on PVC compounds are defined in ASTM D3364.
The latest version of ASTM D1238:2023 Standard Test Method for Melt Flow Rates of Thermoplastics by Extrusion Plastometer, released in February defines the use of force-controlled extrusion plastometers for the determination of melt mass-flow rate (MFR) and melt volume-flow rate (MVR). With this new release, ASTM D1238 opens up new control and automation possibilities, especially when it comes to the preheating phase—significantly simplifying the test process for the user and other lab personnel. The Aflow from ZwickRoell is an extrusion plastometer already prepared to take on these new possibilities.
Test objective Test methods A to D Standard update ASTM D1238:2023 Test equipment ASTM D1238 VS.ISO 1133 ASTM D3364 PVC MFR for PET Downloads
Objective and use of melt flow rate determination ASTM D1238
The determination of flow rates is a quick and easy method to measure rheological properties of polymer melted mass at specified temperatures.
Unlike in a rheometer, the measurement takes place under constant load and thus also under largely constant shear stress. The rate at which the mass is extruded through a standardized die is set according to the viscosity of the polymer melt. The shear rate for this method is usually much lower than in injection molding operations. Nevertheless, the method offers good comparison possibilities, as they are especially needed in quality assurance. Multiple measurements in method D can be used to determine different points on an apparent viscosity curve. These measurements are presented as quotients of the MFR values under different loads.
In the case of polymer melts with homogeneous density distribution, in particular unfilled polymers, it is possible to convert theMVR value (cm³/10 min) into an MFR value (g/10 min) if the melt density at the test temperature is known. By combining methods A and B, the density of a polymer melt can be determined with a good level of accuracy.
ASTM D1238 method A: MFR measurement
Method A to ASTM D1238 for measurement of the MFR value is ideal for individual tests with with relatively low required testing frequency.
- In method A, the extrudate is cut at constant time intervals and its mass is determined with an analytical balance.
- The measurement is performed using the standard die, which is 8 mm high and has a hole diameter of 2.095 mm.
- The initial weight of the polymer to be tested is between 2.5 g and 8.0 g, depending on the expected flow rate.
- The starting point of the measurement lies within a piston position window of 46 ± 2 mm above the die and a preheating time of 7 ± 0.5 min. In the last two minutes before starting the measurement, no additional force may be applied to the piston.
- The time interval of the measurement is also dependent on the flow rate to be measured. It ranges from 6 minutes for low flow rates to 15 seconds for flow rates higher than 25 g/10 min.
- The test result is the extruded mass per unit of time, which is indicated in g/10 min.
- An operator must be present for the entire test sequence, and can therefore only be automated to a limited extent.
- Method A, according to ASTM D1238, covers a measurement range of approximately 0.15 g/10 min up to approximately 50 g/10 min. The limitation is a result of the requirement to cut the extrudate at regular intervals.
ASTM D1238 method B: MVR measurement
- For MVR measurements in method B according to ASTM D1238, the extruded volume of the polymer melt is determined at regular time or travel distance intervals. The measurement can be visually controlled through markings on the piston, or more commonly by using a piston travel distance measurement and time tracking system, which enables precise volume determination, even in the case of fast flowing materials.
- As is the case in method A, a standard die, 8 mm high with a hole diameter of 2.095 mm, is used. The starting point specifications are also identical to method A.
- The test is controlled in a travel-dependent manner. For MFR values up to 10 g/10 min, measurements are performed over a piston travel distance of 6.35 mm. Higher MFR values are measured over a piston stroke of 25.4 mm, equivalent to 1 inch.
- The MVR result is the extruded material volume per unit of time. It is specified in cm³/10 min and is calculated from the distance the piston travels per unit of time.
- In the case of polymer melts with homogeneous density distribution, the melt density can be used to convert the MVR value to an MFR value.
- A significant advantage of this method is the elimination of mechanical cutting. The entire test sequence can be performed without influence by the operator.
- Method B covers a significantly larger measurement range that, according to ASTM D1238, reaches from 0.5 g/10 min to approximately 1500 g/10 min. High-quality extrusion plastometers, however, are able to measure an even wider range with a high degree of reproducibility.
- Extrusion plastometers with displacement sensor and automatic test weight lifting device allow for a more automated control of the test sequence, which can be easily and conveniently set by entering a target MFR or MVR value.
ASTM D1238 method C: MVR halved die dimensions
Method C to ASTM D1238 is another variant of method B, in which a die with half the height and half the diameter is used.
- The measurement is started after 7 minutes of preheating time and at a piston position of 50 mm above the die. The MVR value is measured over a piston stroke of 25.4 mm.
- This method is used for polyolefin applications, which have an MFR value greater than 75 g/10 min. By using the half dies, the shear strain remains equal in the polymer melt, however the MVR value is reduced by a factor of about 8 and is therefore easier to measure.
ASTM D1238 method D: multiple weight test, FRR
The flow rate ratio, FRR, is the quotient obtained from MFR measurements under two different loads.
- The measurements are usually carried out with a single filling of the extrusion barrel.
- After the preheating phase of 7 minutes, the test sequence is started with the first test weight at a piston position of 46 mm.
- As soon as the first measurement has ended, the test weight is changed and after a short stabilization phase, the next MFR measurement begins.
- Two or more test loads can be measured within one measurement sequence, either in ascending or descending order.
- The Aflow extrusion plastometer from ZwickRoell is commonly used for this test. The instrument allows for convenient test control, measurements in ascending or descending order of the test weights, as well as impact-free change of test loads applied by force control, without the effects of mass acceleration that often occur with deadweight instruments.
New possibilities provided by ASTM D1238:2023
The latest version of the ASTM D1238 standard released in February, 2023 allows the use of already commercially available extrusion plastometers that apply the piston load with a force controlled drive rather than dead weights. These force controlled extrusion plastometers, including the Aflow from ZwickRoell, provide significantly better control possibilities for methods A, B and C for the entire preheating phase, for the measurement process and in the creation of multiple weight tests according to method D.
Test & test equipment requirements
High repeatability and reproducibility
In an ASTM round robin test, force controlled extrusion plastometers were compared with classic dead weight instruments. The force controlled instruments displayed very good conformity of the MFR mean values and performed better in terms of repeatability and reproducibility of the MFR values than the classic dead weight extrusion plastometers.
Complex specification for test control
The determination of melt volume-flow rates (MVR) or melt mass-flow rates (MFR) on different polymers or polymer grades in the testing lab can often prove to be a complicated task for laboratory managers. Not only do they have to know at what weight and temperature each polymer grade must be measured to meet ASTM D1238 compliance, they must also know the required volume of polymer, and control the preheating phase sequence of the test so that the measurement of the melt flow rates starts exactly in the specified window of 7 ± 0.5 minutes of the preheating phase and at a piston height of 46 ± 2 millimeters. In addition, corrections by means of purging, i.e. the application of a larger weight than the test weight, are only permitted up until 2 minutes prior to the beginning of the measurement phase, making these corrections difficult to implement correctly by manual means.
Aflow extrusion plastometer for standard compliant testing to ASTM D1238
Aflow – simply add the material and start
- The general function of force controlled extrusion plastometers, such as the Aflow model from ZwickRoell, is similar to a capillary rheometer and they feature a significantly wider range of control options.
- For example, laboratory personnel may agree to use a test sample weight of 5 g for all MFR values above 1 g/10 min. In many cases, this amount of material can be easily taken from a container by simply using the appropriate measuring scoop size.
- The instrument detects the fill level in the barrel right at the start of the test and can measure the order of magnitude of the melt volume-flow rate of the polymer early in the preheating phase. According to this constantly available information, the instrument continuously calculates the ideal and, according to ASTM D1238 standardized trigger position from which the piston must move freely under test load in order to reach the target window at the start of the test and reacts accordingly. With the flow rate present just before the target window is reached, the Aflow decides how to perform the measurement in accordance with the standard.
- For the operator this means that they simply have to fill 5 g of material into the extrusion barrel, start the test and rely on the fact that the test is running according to standard and with optimal test parameters. The laboratory manager no longer needs a list with the necessary parameter settings for each polymer grade and can rest assured that operators have run the test correctly. The auditor benefits as well. They no longer have to question how the lab ensures that every measurement on every polymer grade has been performed correctly.
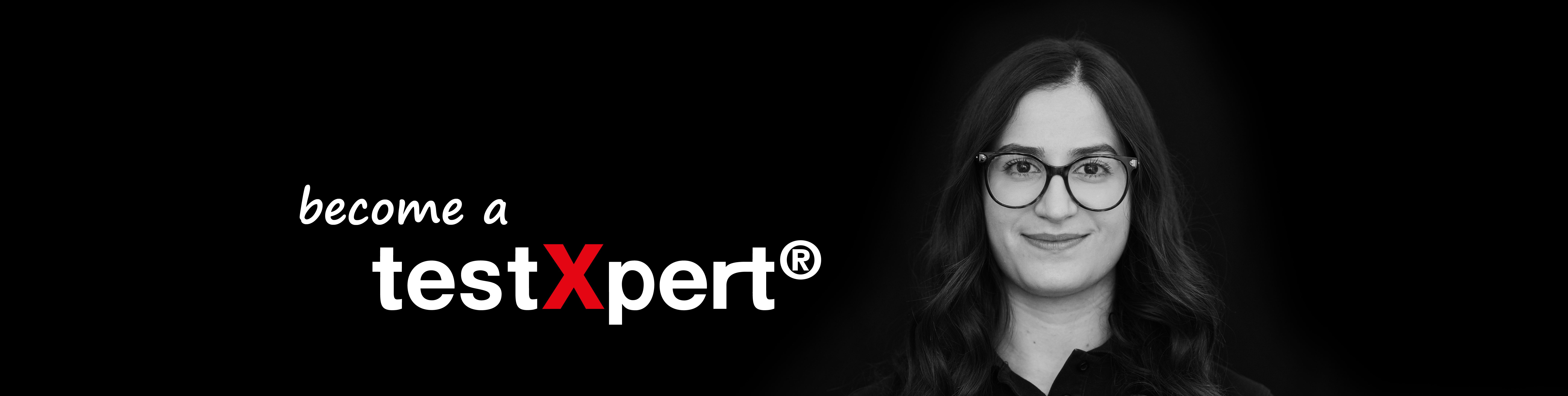
Simple testing according to ASTM D1238 with testXpert
The testXpert testing software makes melt flow testing to ASTM D1238 simple, despite the many parameters specified by the standard.
- The standard test program according to ASTM D1238 includes the specifications defined by the standard. It allows you to test at 100% standard compliance without having to worry about anything.
- testXpert guides you through the test, step by step, making onboarding of new employees fast and easy. With our user management feature you only see the tasks are that relevant to your responsibilities.
- The analytical balance automatically transmits the weight of the individual sections to testXpert without error.
- With the Test Data Management feature included in testXpert Analytics, you have the ability to evaluate cross-application values. Contrast the flow rates, MVR and MFR according to ASTM D1238 with other values, for example tensile modulus, flexural modulus, tensile strength or notched impact strength.
- The simple longterm evaluation option of our Trend Analysis feature recognizes deviations in the quality specifications and supports you in optimizing your processes.
ASTM D1238 vs. ISO 1133
The methods for melt flow index testing to ASTM D1238 and ISO 1133 on thermoplastics are equivalent but not identical, as they differ in some respects, especially in terms of test procedure:
- For some polymers, test temperatures and test weights are specified differently in ASTM D1238 and ISO
- The recommended volume of polymer to be used is slightly different. According to ASTM D1238, it is 5 g.
- In ASTM D1238, the duration of the preheating phase (time from when the polymer is added to the start of the test) is standardized at 7±0.5 minutes with very strict tolerance; in ISO 1133-1 it is specified to at least 5 minutes, but can also be significantly longer.
- The starting point of the test, according to ASTM D1238, is at a piston position of 46±2 mm above the die, and in the ISO standards from 50 mm.
- While ASTM D1238 specifies a narrowly tolerated time sequence of testing for all polymer types, tests of polymers that are sensitive with respect to time- or temperature-dependent history and/or moisture are described in the separate ISO 1133-2 standard.
- While ASTM D1238 specifies very precisely over what piston travel distance or at which section interval measurements are to be made at which MFR value or MVR value, ISO 1133-1 leaves it largely up to the operator to determine suitable section or measurement intervals for the test.
ASTM D3364: MFR and MVR measurement on PVC
ASTM D3364 – measurements on PVC with unstable flow rates
- The method is an expansion of ASTM D1238 and is used to measure the MFR value and the instability of PVC compounds.
- In the standard configuration, measurements are performed at a temperature of 175 °C and a load of 20 kg. For hard PVC, it may be beneficial to use larger test loads up to approximately 50 kg. Semi-hard or soft PVC is also measured at 150 °C / 50 kg.
- The die is 25.43 mm (1 inch) long, and like the standard die, has a hole diameter of 2.095 mm and a cone-shaped inlet.
- Compared to the standard die, this die produces an approximately 10-fold reduction in MVR.
- The filling volume is 2.15 g and must be precisely adhered to.
- MFR values are calculated in mg/min and the instability of the melt material in %.
- With this test method to ASTM D3364, instabilities caused by temperature effects, shear with breakage of polymer bonds or due to rheological effects such as uneven distribution in viscosity or molecular weight can be detected.
Test requirements for MFR measurements on PET
Special test precautions must be taken for MFR measurements on PET:
- First, the PET must be sufficiently dried and poured into the extrusion barrel in the dry state.
- An optional nitrogen blanket at the extrusion barrel prevents direct contact by the material with the ambient air.
- In accordance with ASTM D1238, the test is run in precisely defined time sequences that are recorded by our testXpert testing software.
Intrinsic viscosity: Correlation of IV measurements for the MFR value for linear PET
The molecular weight of polyethylene terephthalate (PET) is usually described in terms of intrinsic viscosity. This is the IV value in dl/g. The longer the polymer chains, the higher this characteristic value. This makes it possible to demonstrate molecular chains and how they can occur when moisture that is too high during the melting process.
The disadvantages of this method are that recyclers of PET in particular, are often not equipped to handle corrosive or toxic solvents. Furthermore, the fact that the test lasts a long time poses a practical problem. Therefore, measurement of the melt mass-flow rate (MFR) with subsequent conversion by correlation has already been established in this field since the early 1990s.
When controlling the Mflow and Aflow extrusion plastometers via the testXpert testing software, the correlation between IV value and the MFR can be determined by appropriate preliminary measurements and then applied to subsequent measurements.
Frequently asked questions regarding ASTM D1238
ASTM D1238 describes the melt flow rate determination (melt mass-flow rate (MFR), melt volume-flow rate (MVR) and flow rate ratio (FRR)) on unfilled or filled thermoplastic melted mass.
The latest version of ASTM D1238, released in February, 2023, supports the use of force-controlled extrusion plastometers as an expansion of the traditional, weight-loaded instruments for the determination of MFR and MVR values. With this ASTM D1238 update, the standard opens up new control possibilities, in particular when it comes to the preheating phase of the test sequence. The test sequence can be automated over a wide MVR range, which to a great extent relieves personnel from the task of entering the correct test parameters. This makes work in the lab more efficient and ensures reproducibility of your tests when using different instruments at different locations, operated by different users.
The ASTM D1238 and ISO 1133 standards differ in some aspects of the test procedure, including:
- Test temperature and test weight
- Recommended volume of polymer
- Duration of the preheat phase
- Starting point of the test
- Determination of the extrudate and measurement intervals