Video extensometers
Video extensometers are camera-based measuring systems for materials testing. They measure contact-free, which eliminates any influence on the material characteristic values. During the test, one or more cameras capture images of the specimen, which are digitized and forwarded to the testing software. An image-to-image comparison is used to evaluate shifts on the specimen. This requires the marking of an initial gauge length, either by setting manual gauge marks directly on the specimen or, to save time, by virtual gauge marks via the test software.
videoXtens, the video extensometer from ZwickRoell, is available in different versions and configurations. You get the exact video extensometer that meets you requirements in terms of accuracy, function and flexibility.
AdvantagesComposites, plastics and rubberMetalsDynamic applicationsHigh temperatureTextilesUniversities / testing labsAdvanced functionalityFAQsRequest a consultation
Why choose a video extensometer?
- Video extensometers measure contact-free, which eliminates any influence on the material characteristic values.
- The huge range of applications creates a wide scope: Video extensometers can measure not only all types of materials, but also sensitive specimens, mini specimens and specimens with high fracture energy.
Easy to use and efficient
- With mark-free measurement, there is no longer a need to mark your specimens.
- Automated features reduce operator steps.
- Operation, evaluation, and test data storage are all handled through a single software platform: The videoXtens is fully integrated in our testXpert testing software and the measured values are synchronized.
- The videoXtens is low maintenance.
- Every specimen counts, the gauge length is automatically placed around the break.
Rely on the measured values
- The accuracy of the videoXtens is verified during on-site calibration from as little as 10 µm, for which you receive a certificate.
- Accurate measurements at room temperature and in a temperature chamber.As the same videoXtens is used for both measurements, the test results are as comparable as possible.
- At the same time, the width measurement is also highly accurate, non-contact and mark-free.
Measuring Without Gauge Marks
ZwickRoell videoXtens systems can be used on a wide range of materials without the need for specimen gauge marks. This saves time in specimen preparation and eliminates possible influence of the gauge marks on the specimen and the measurement.
The testing software conveniently places virtual gauge marks on the specimen image. The blue contrast light technology transfers the natural roughness of the specimen surface into a high-contrast pattern. The virtual gauge marks mark a small area, the patern within this area is used as a measurement marker and tracked.
No more time-consuming marking or gluing of markers—the effort normally required for specimen preparation is eliminated. And without compromising accuracy.
videoXtens: Simply See More
Simply activate a software option and see more, because the testing software gets more information out of the camera images: Why only set two gauge marks?The video extensometer’s camera(s) capture a large part of the specimen. Thanks to intelligent algorithms, the testing software also uses this area for other evaluations:
- Simultaneous measurement of the change in width
- Define up to 100 measuring points
- Evaluate local strains via 2D digital image correlation
- Automatically set the initial gauge length around the break
- Save images, subsequently shift the initial gauge length and recalculate
These options are purely software add-ons—there is no need to expand the hardware on the video extensometer.
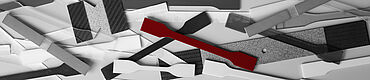
Video extensometer for composites, plastics and rubber
Criteria for plastics and composites testing: Increased accuracy requirements apply to the determination of the tensile modulus, for example ISO 527-1 Annex C. Calibration of the systems at your premises provides you with proof that these requirements have been met. The high accuracy is also achieved with the same extensometer when testing in a temperature chamber, which guarantees comparable test results.
Testing composites: The videoXtens even determines the Poisson's ratio with maximum accuracy—including in a temperature chamber. Non-transparent composite materials such as CFRP are tested with the need for markings. The video extensometer covers a wide range of applications: tensile tests, shear tests, flexure tests, V-notch shear tests with 2D digital image correlation, and more.
Testing elastomers, rubber and film: The videoXtens has a high measuring range for these highly ductile materials. Thanks to the connection to the crosshead, the video extensometer is easy to align and the measuring marks remain centered during the entire test. By attaching an adapter, it is ready for measurement in a temperature chamber without conversion.
videoXtens (biax) 2-150 HP | videoXtens 1-270 P | |
---|---|---|
Typical applications | Tensile tests, shear tests, flexure tests on plastics and composites, incl. high-accuracy determination of the tensile modulus and Poisson’s ratio. | Tensile tests on film, rubber and elastomers |
Typical standards |
|
|
Measurement range | max. 175 mm | max. 330 mm |
Accuracy class (1 | 0.5 / B1 | 1 / B2 |
Measuring without gauge marks | • | - |
Advanced functions: | ||
2D-DIC | • | • |
Change in width measurement (1 | 0.5 / B1 | 1 / B2 |
Strain distribution | • | • |
Test re-run | • | • |
Flexure test | • | • |
- (1 Accuracy class to ISO 9513 / ASTM E83
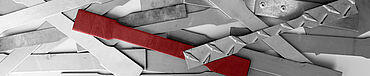
Video extensometer for metals testing
The majority of tensile tests are based on the ISO 6892-1 or ASTM E8/E8M standards. The following criteria are used to select the most effective video extensometer:
- Test method: Open loop or closed loop strain rate control
- Ambient temperature or high temperature
- Static or dynamic application
ZwickRoell videoXtens system score particularly well in metals testing:
- Simple operation: mark-free measurement thanks to blue contrast light technology, automatic setting of the initial gauge length
- Every specimen counts: reliable values through out-of-plane compensation, automatically set gauge length around the break
- Automation: videoXtens L extensometers are optimized for automated systems
videoXtens L 3-205 | videoXtens L 3-320, 4-460, 6-680 | videoXtens 1-120 | videoXtens 3-320 | |
---|---|---|---|---|
Typical applications |
|
|
|
|
Typical standards |
|
|
|
|
Measurement range | max. 240 mm | max. 680 mm | max. 180 mm | max. 350 mm |
Accuracy class (1 | 0.5 / B1 | 0.5 / B1 | 0.5 / B1 | 0.5 / B1 |
Measuring without gauge marks | • | • | • | • |
Can be automated | • | • | - | - |
Advanced functions: | ||||
2D-DIC | • | • | • | • |
Change in width measurement (1 | 0.5 / B1 | 0.5 / B1 | 1 / B2 | 1 / B2 |
Strain distribution | • | • | • | • |
Test re-run | • | • | • | • |
Flexure test | • | • | • | • |
- (1 Accuracy class to ISO 9513 / ASTM E83
Video extensometers for high-temperature testing
Many of the video extensometers can be used in combination with a ZwickRoell temperature chamber for tests up to +360 °C. For tests at even higher temperatures up to +1,400 °C, optical strain measurement faces further challenges. The videoXtens 1-32 HP/TZ was specially designed for non-contact strain measurement at high temperatures.
Applications for the video extensometer for high temperatures:
- Long-term applications, tensile, compression and flexure tests, cyclic applications (< 2 Hz)
- Various materials: metals, refractory materials, ceramics, glass
- Temperature range: ambient temperature up to +1,400 °C
Video extensometer for dynamic applications
Dynamic tests often have low strains at high frequencies. For reliable measurement during these tests, a video extensometer must feature extremely high accuracy.
Thanks to optical strain measurement, our videoXtens dynamic is particularly suitable for sensitive specimens or materials such as composites, which can strongly splinter at break and thus damage contact measurement systems.
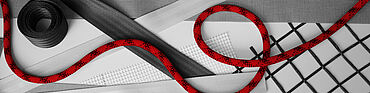
Video extensometers for textiles
When testing textile materials, video extensometers offer clear advantages:
- They are insensitive to breaks of specimens prone to whipping and measure up to the point of break.
- Reliable test results: Measurements using video extensometers are much more accurate than measurements via crosshead travel, because they exclude the influence of material slippage within the specimen grips.
- Video extensometers easily handle lattice structures as well as the wide width of geotextile specimens.
Geotextile specimens, in particular, display complex strain behavior while undergoing a tensile test. For detailed characterization of geotextiles, the videoXtens features a unique function: Instead of evaluating only one gauge length, the software is used to place several gauge lengths in longitudinal or transverse strain direction in different lengths on top of or next to each other. (2D dot matrix software option)
videoXtens 1-270 P | videoXtens 1-120 | videoXtens 3-320 | |
---|---|---|---|
Typical applications |
|
|
|
Typical standards |
|
|
|
Measurement range | max. 330 mm | max. 180 mm | max. 350 mm |
Accuracy class (1 | 1 / B2 | 0.5 / B1 | 0.5 / B1 |
Measuring without gauge marks | - | • | • |
Advanced functions: | |||
2D-DIC | • | • | • |
2D dot matrix | • | • | • |
Test re-run | • | • | • |
Video extensometers with full flexibility for universities or testing laboratories
Universities often look for full flexibility for educational purposes. We would be happy to assemble a videoXtens system for you based on a modular principle: interchangeable lenses, movable axis, additional cameras, separate housing.
Or, if you are faced with frequently changing applications and want to be prepared for possible future needs, the videoXtens system offers you a high level of flexibility. For example, the videoXtens 3-320, an all-round system, is a preferred testing laboratory option for a variety of different applications.
Please feel free to contact us for more information.
With ZwickRoell video extensometers and our testXpert testing software, you can start testing immediately: Standards are mapped in our standard test programs in such a way that only selection parameters need to be determined. After switching to another application, the test conditions are saved and restored identically the next time they are accessed. This guarantees fast and easy switching between applications.

Advanced functionality: Simply activate and see more
The testXpert testing software gets even more out of the camera images. Why only set two gauge marks? The video extensometer’s camera(s) capture a large part of the specimen. The testing software also uses this area for other evaluations, from change in width and automatic break detection to 2D digital image correlation.
Change in width measurement / transverse strain measurement
This option is used for biaxial measurements: One or more transverse strain measurements are recorded at the same time as the longitudinal strain measurement, for example the change in width directly at the edge of the specimen, contact-free and without gauge marks. The number of measuring points can be freely selected. The values are automatically averaged, but can also be evaluated individually.
The extension is available as a software-only option or as a hardware extension:
- The software option can be easily extended and meets accuracy class 1 (ISO 9513) for most videoXtens systems.
- For the transverse strain hardware option, an additional camera is integrated directly into the housing of the videoXtens. This camera is specially designed for the change in width and achieves much more accurate measurement values, for example accuracy class 0.5 (ISO 9513).
Strain distribution: every specimen counts
A break outside the gauge length causes costs and additional time for specimen preparation and retesting. This can be prevented with the strain distribution option.
During the test, the testing software automatically places the gauge length symmetrically around the break point.
The workaround offered by ISO 6892-1 in Annex I to validate breaks outside the gauge length is also activated effortlessly by our software; calculation and validation according to standard specifications run automatically and in real time. No need to manually measure and recalculate the specimen as was the case before.
Test Re-Run: re-calculate instead of re-testing
The test re-run function can be used to virtually repeat and recalculate the test with a modified initial gauge length. You save time on specimen preparation and testing and can run different evaluations on one and the same specimen.
During the test, the testing software records the image series. You can later use these to change the size and position of the initial gauge length as required. One click starts the recalculation and all characteristic values are recalculated on the basis of the new gauge length. Each recalculation is displayed separately, making comparisons simple and clear.
2D Digital Image Correlation (DIC)
2D digital image correlation visualizes deformations and strain over the entire visible specimen surface. This software option considerably expands the analysis options of the videoXtens. Activation is very simple, you only need a software license. The live strain measurement and subsequent 2D DIC analysis are performed with the same videoXtens and using the same marker.
A wide range of analysis tools provide different types of information: Gauge lengths, measuring points, virtual strain gauges, cutting lines, vector maps and more. Here you will find detailed information about 2D DIC.
2D dot matrix
Up to 100 measuring points can be set and measured in any arrangement or in the form of a grid. In this way, local strains and inhomogeneities of a specimen under load are determined. X and Y coordinates as well as the distances between dots are available as measured values.
The measured values can be easily exported or displayed as channels directly in testXpert. The prerequisite is that all measuring points are applied to a flat specimen surface, as this is a two-dimensional measurement. Typical applications includes tests on components or multiaxial tensile tests.
Flexure test: deflection measurement
The videoXtens offers different options to measure deflection. A measuring plunger is often placed under the specimen for comparability with measurements using sensors or transducers. The measurement displacement during the test is measured by videoXtens using stick-on gauge marks.
Alternatively, it is also possible to measure directly on the specimen edge: either by applying a mark to the flexure specimen or by using a backlight behind the specimen, which makes the lower edge of the specimen visible and measurable for the videoXtens. In addition to the deflection in the test axis, the polynomial approximation of the curvature can also be determined.
Video extensometer FAQs
Video extensometers are camera-based measuring systems for materials testing. During the test, one or more cameras capture images of the specimen, which are digitized and forwarded to the testing software. An image-to-image comparison is used to evaluate shifts on the specimen. For strain measurement with a video extensometer, an initial gauge length must be defined. The initial gauge length is identified by manual or virtual gauge marks.
Glue marks or pen marks exemplify manual gauge marks. It is much easier to use virtual gauge marks, which are defined via the testing software. The prerequisite is a pattern on the specimen surface. An area on the specimen surface is defined with the virtual gauge mark. The pattern within this defined area is tracked during the test,
The pattern on the specimen surface can be applied using a spray. Or even easier: the natural surface structure of the specimens can be used. The blue contrast light technology transforms the natural surface structure into a high-contrast pattern. This eliminates the need for any specimen markings.This is why this is also referred to as mark-free measurement with video extensometers.
Since video extensometers measure without making contact, you need markings in order to set an initial gauge length. Based on this, the change in displacement is measured and the strain calculated. This is often still done by marking the specimen: by adding dots, sticking on markers or other marking options that are part of the specimen preparation process.
Faster and easier is the mark-free measurement based on blue contrast light technology at ZwickRoell. Here, virtual marks are placed on the specimen image using software. Efforts required for specimen preparation are eliminated.
Mark-free measurement by the videoXtens is based on blue contrast light technology: Many materials, such as metals and components, have a naturally rough surface. With the blue contrast light technology, the roughness is transferred into the software as a high-contrast pattern, allowing the software to easily place virtual gauge marks on the specimen. This eliminates the effort required to manually apply gauge marks for specimen preparation.
And without compromising accuracy.
Video extensometers can test any material up to the point of break. This includes sensitive materials that would be pre-stressed by the knife edges of contacting extensometers, such as metal foils, plastic films, thin wires, fibers and biomaterials. Or materials that damage contact extensometers due to their high fracture energy, such as brittle breaking metals, splintering composites, splitting strands or whipping ropes.
The videoXtens systems offer additional functions solely through software extensions, which are simply activated as a license. As the entire specimen or at least a large part of it is viewed via the camera(s), these images can also be used for other evaluations. For example for
- the measurement of transverse strains or changes in width,
- for setting up to 100 measuring points (2D point matrix),
- the determination of local strains or visualization using entire strain maps (2D DIC)
- for automatic fracture detection,
- for automatic setting of the gauge length around the break,
- for the recalculation of a test under different conditions (size and position of the initial gauge length) using images recorded during the test.
There are no known disadvantages with video extensometers. But that does not mean that they are always the best possible option. A less expensive clip-on extensometer may be recommended for low test volumes and a small variety of applications. Our product range therefore includes various systems and functionalities. We would be happy to discuss the options with you, as well as the advantages and disadvantages of the various systems, tailored precisely to your situation. This will help you find the most efficient extensometer for your needs.
Please feel free to contact us for more information.
The ZwickRoell video extensometer includes many automated functions that alleviate tasks for the operator:
- Automatic gauge-mark recognition and recording of the initial gauge length L0.
- Easy alignment in relation to the specimen due to automatic centering.
- Different specimen thicknesses are automatically compensated. The testing software also compensates for the testing of shear specimens with offset surfaces.
- The system is wear-free and the housing protects it from dust and dirt, making the videoXtens very low maintenance.
- The housing of the videoXtens is tamper-proof.
The testing machine attachment of most videoXtens systems includes a connection to the crosshead. This means that the video extensometer travels at half crosshead speed. This means that the test procedure automatically remains centered in the field of view and the measuring range is optimally utilized, i.e. longer measurement travel is possible. And: there are no blind spots caused by large specimen holders that could obscure the view of the measuring points.
In addition to the increased measurement travel distance, the system also offers increased measurement accuracy.
- Intelligent algorithms based on many years of development experience.
- Selective high-quality components, industrial-grade cameras and high-quality, low-distortion lenses.
- The video extensometers and testing systems are developed and manufactured by ZwickRoell, in-house. This is something we will not compromise on.
- Exact synchronization of all measurement channels.
- Mounting of video extensometers using stable, low-vibration support arms.
- Housing to protect against dirt and dust and inadvertent misalignment of the components.
- Specially developed lighting provides continuous high-quality contrast ratios on the specimen, even with varying environmental conditions.
Measurement of videoXtens systems in combination with a ZwickRoell temperature chamber is unbeatably accurate. Example: The videoXtens 2-150 HP meets the strict requirements for determining the tensile modulus in accordance with ISO 527-1 Annex C, even under temperature conditions. Why this is the case:
- ZwickRoell video extensometers and temperature chambers have been adapted to perform optimally with each other. Temperature control
and air distribution in the temperature chamber are optimized in such a way that the videoXtens resolution is only minimally affected, even at different temperature conditions. - The entire system is closed: videoXtens is connected to the temperature chamber through a tunnel. Influences due to air turbulence are thereby also minimized outside of the temperature chamber.