Testing of Bars and Rods
Bars and rods are long round or square products with cross-sections up to 240 x 320 mm² and are used widely in rolling and forging: for use as base product for wire rod and sections or for transport industry forgings such as connecting rods, crankshafts and steel rails; generator and turbine shafts in energy technology; as end products in bridge building and shipbuilding or in equipment manufacturing and storage tank construction.
The demands on their mechanical characteristics are as varied as their applications: from high tensile for structural materials to ductile for subsequent forming processes.
Tensile tests Hardness tests FATIGUE AND FRACTURE MECHANICS TESTS Concrete-reinforcing steel
Tensile Tests on Bars and Rods
Tensile tests on bars and rods are usually performed according to ISO 6892-1 and ASTM E8, which are internationally recognized and widespread standards. ISO 6892-1 is also a European standard (EN ISO 6892-1) and therefore also applicable in the European Union (for example, as DIN EN ISO 6892-1 in Germany). Specimens are machined from the product and prepared for the tensile test in accordance with the product shape or as specified in the product standards. Sections of products can be used as specimens for testing if the cross-section of the product permits. The required loads can easily exceed 2,500 kN. Various customized ZwickRoell systems up to 5,000 kN are operating successfully. In such cases, special requirements are placed on the specimen grips and clamping. ZwickRoell therefore not only develops new specimen grips, but also new technologies that prevent premature failure of specimens caused by unwanted clamping effects.
Since 2009, ISO 6892-1 and ASTM E8 allow the test speed to be automatically controlled and regulated by the strain rate. The tolerances for strain rate control required by the standards (especially for closed-loop strain rate control) can be easily met with both the makroXtens and laserXtens extensometer.
Testing solutions for tensile tests on bars and rods
ZwickRoell's parallel closing hydraulic specimen grips ensure perfect specimen clamping and positioning throughout the entire test, preventing the specimen from slipping. In most cases, standard-compliant strain measurement is performed using automatic contact or optical (non-contact) extensometers. The ZwickRoell makroXtens is the classic and proven solution for the tests on bars and rods. Through its mechanical design, it combines high resolution and high accuracy with very high robustness. The robust mechanical construction allows it to measure continuous strain up to the point of specimen break. Strain at break can be determined automatically, without the need for tedious specimen markings or manual measurement after specimen remains are collected.
The laserXtens is our innovative solution for strain measurement up to specimen break, and fully meets standard requirements (ISO 6892-1, ASTM E8, as well as ISO 9513, and ASTM E83) for bars and rods. The laserXtens does not require the application of specimen markings; based on the measurement principle, it can use the pattern created by the laser light on the surface as markings. The optical evaluation of this "self-marking" is carried out in such a way that even scale and the occasional flaking of scale do not disturb the markings.
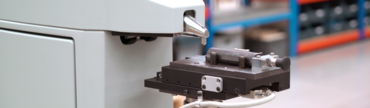
Hardness testing on bars and rods
Hardness tests are performed on bars and rods for characterization of micro-structures (micro hardness testing), to determine the surface hardness, and for rough estimation of strength. A wide variety of methods with very small and large test forces are used. All of the classic methods to Brinell (DIN EN ISO 6506-1), Rockwell, as well as Vickers (DIN EN ISO 6507-1, ASTM E92) and Knoop (DIN EN ISO 4545-1, ASTM E92) are relevant hardness testing methods for these pre-products. The relevant ASTM standards are ASTM E10 (Brinell), ASTM E384 (Vickers and Knoop) and ASTM E18 (Rockwell). In addition, other methods or specifications are used for certain application areas (for example, the European standard EN 2002-7 is used in the aerospace industry).
Because the hardness test is simple, fast, and reliable, it is frequently performed and its results are also compared with other characteristics. For long products the hardenability of the material is often determined by establishing the hardness distribution along a rod following a tempering and quenching test (Jominy test / Jominy end quench test; DIN EN ISO 642 / ASTM A255).
Hardness testers for tests on bars and rods
ZwickRoell’s product portfolio includes hardness testers for every required hardness testing method, including machines for automated Jominy testing.
The ZwickRoell product portfolio offers hardness testers and instruments for every application and test method. ZwickRoell hardness testers and instruments meet the requirements of all common international standards and can also be calibrated to international standards. As a calibration lab, ZwickRoell is accredited for the calibration of hardness testers by the German national accreditation body DAkkS.
Another aspect of hardness testing is the verification and determination of the average global hardness after rolling. Rolling is a thermo-mechanical process, which in addition to setting width and thickness, also determines mechanical properties. Hardness methods that employ higher forces are used to determine the average values of these sometimes coarse structures. Preferred methods are Brinell or Rockwell. For bars and rods, it is not uncommon to use portable hardness testers that can be used on-site on the original part.
Another aspect of hardness testing is examination of the microstructure by performing hardness tests on microstructural components. Due to the small size of the microstructural components, hardness testers with small to very small forces are used—usually stationary microhardness testers with indentation sizes and depths that can be adapted to the dimensions of the microstructural components via the indentation forces.
Fatigue tests on bars and rods
The ways products are used in transport and energy technology place particular demands on the safety of the products and of components made from them. The material properties for durability and very high cycle fatigue, which are determined in fatigue tests, frequently have a safety-relevant impact on the choice of material and design of parts. Specimens are tested under cyclic load conditions and under alternating tension-compression loading. ZwickRoell offers fatigue testing machines with an electromagnetic drive up to 1,000 kN as standard. The largest servohydraulic testing machine currently in use can handle loads up to 5000 kN.
- Robust servo-hydraulic systems, proven in service
- Robust units with electromagnetic resonance drive
- Specimen clamping for all relevant tests
- Control and evaluation technology developed and built/programmed at ZwickRoell
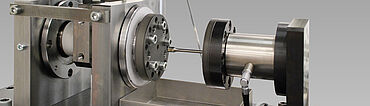
Fatigue tests on bars and rods under torsion load
The behavior of round products under torsion is important in materials testing. For static testing, ZwickRoell supplies drives, which when used in combination with materials testing machines, can apply torque to the specimen and determine the corresponding material properties. It is also possible to superimpose multiple load axes and test the material according to its use. For fatigue testing under high torque alternating load, frequencies up to over 200 Hz can be achieved in using a vibrophore equipped with special test fixtures. Using resonance conditions means that the test is both quick and, due to extremely low power consumption, cost-effective. The advantages when testing with vibrophores include:
- Customized fixtures and devices
- Faster testing
- Higher energy efficiency
- Very low maintenance requirements
Testing of concrete-reinforcing steel
Because concrete has high compressive strength but lower tensile strength, it is reinforced with embedded steel. Reinforcing steels are mainly produced in diameters from approx. 5 mm to approx. 60 mm. The smaller diameters are then further processed into mats or lattices before having concrete poured over them on site.
Testing these ribbed steels poses a particular challenge because, apart from cutting to length, no further mechanical specimen preparation takes place.