Testing of Metal Pipes
Pipes transport granulated materials, liquids, and gases, both aggressive and neutral in nature. They are used in wide variety of environments, including nuclear power stations, in and above the ground for transporting oil and natural gas, in engines for fuel delivery and exhaust gases, and in the chemical industry for producing raw materials. They are therefore manufactured from a diverse range of materials and alloys, using various production processes.
Tensile tests Hardness testing Compression tests Drop weight tests TESTING UNDER THE INFLUENCE OF HYDROGEN
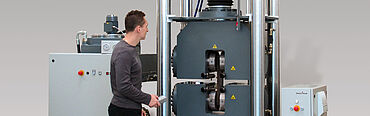
Tensile tests on metal pipes
The methods used to test tensile specimens taken from or consisting of pipes vary according to the product form. Small, thin pipes are crushed at the ends for a sufficient length and then pulled, while cores are used in larger diameter pipes to prevent pre-damage through crushing. With larger pipes, standardized specimens are produced from material removed from the wall of the pipe. It is possible that specimens (taken longitudinally) may display the curve of the pipe radius; for reliable, pre-damage-free testing this radius should be compensated for with suitably shaped counterpieces. ZwickRoell offers tensile testing machines from 500 N to 2,500 kN with the right specimen grips.
Hardness test on metal pipes
Hardness tests on metal pipe and large pipe are mainly carried out under two aspects: testing of weld seams and determination of the basic hardness of the pipe Depending on the application, hardness tests are performed to ISO 6506-1 (Brinell), ISO 6507-1 (Vickers), ISO 6508-1 (Rockwell) as well as ASTM E10 (Brinell), ASTM E384 (Vickers and Knoop) and ASTM E18 (Rockwell).
Testing and determining the hardness average value of the pipe wall
One aspect of hardness testing is the testing and determination of the hardness average value of the pipe wall after manufacture. Pipes are manufactured using a wide variety of methods, among them rolling processes. Since rolling is a thermo-mechanical process with which mechanical characteristics, along with the pipe wall thickness and diameter of the pipes, can be tested, hardness testing is used for fast determination of mechanical-technological properties.
Determining the grain structure of metallographic constituents with hardness tests
Another aspect of hardness testing is the determination of the grain structure by performing hardness tests on metallographic constituents. Due to the small size of the microstructural components, hardness testers with small to very small forces are used—usually stationary microhardness testers with indentation sizes and depths that can be adapted to the dimensions of the microstructural components via the indentation forces.
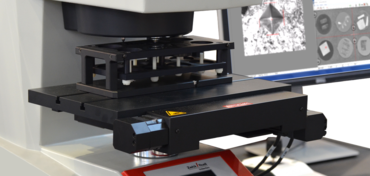
Testing of weld seams
The ZwickRoell product portfolio offers hardness testing machines and instruments for all test methods. ZwickRoell hardness testing machines and instruments meet the requirements of all common international standards and can also be calibrated to international standards. As a calibration lab, ZwickRoell is accredited for the calibration of hardness testers by the German national accreditation body DAkkS.
Compression test on metal pipes
Crush tests are carried out on pipes to test their strength and ductility. These characteristics can be of considerable significance in situations where the integrity of pipework must not be affected by earthquakes, especially when pipes are laid directly in the ground. The test areas of the ZwickRoell materials testing machine can be set up in accordance with pipe diameters to make handling of specimens both simple and time-saving.
Drop weight tests on metal pipes
For large oil and gas pipelines, specimens taken from the pipe wall are subjected to a drop weight test according to API 5L. Specimens with the height of the original wall thickness and widths of several centimeters are abruptly loaded via a falling weight with a striking edge. The energy (weight and release height) is set so that the specimen breaks, allowing the fracture surface to be assessed visually. ZwickRoell produces drop weight testers up to 100,000 J for this type of test.
Testing of metal pipes under the influence of hydrogen
Metal pipes are used for the transport and storage of hydrogen. Under the direct influence of hydrogen, metallic materials become brittle and lose their strength.
The effects of hydrogen influences on metals are investigated through a variety of tests. These tests can be performed in a compressed hydrogen environment or a cryogenic environment.