Qualitätskontrolle von Hydro-Motorlagern
Hydro-Motorlager kombinieren die akustische Isolationsfunktion eines herkömmlichen Gummilagers mit ausgewogener Dämpfungsleistung. Die Hauptgummifeder eines Hydrolagers hat eine obere und eine untere Kammer. Die Kammern sind über eine Reihe von Kanälen verbunden und durch ein Gummiventil getrennt. Die Hauptfeder wird mit Hydrauliköl gefüllt, das als sekundärer Dämpfer agiert. Bei Anregung oder Schockeinwirkung öffnet sich das Gummiventil und der Entlastungskanal wird geschlossen, so dass der Glykolfluss zwischen den beiden Kammern umgelenkt wird und die Steifigkeit des Lagers sich ändert.
Um die Anforderung seiner Kunden besser erfüllen zu können, hat ein führender Hersteller aus dem Bereich der Automobil-Schwingungstechnik sein Prüfverfahren auf eine neue Technologie umgestellt. Bis dahin wurden die Qualitätskontrollen des Unternehmens in dessen F&E-Niederlassung mit einer herkömmlichen servohydraulischen Prüfmaschine durchgeführt. Angesichts der hohen Betriebs- und Wartungskosten und Infrastrukturkosten, suchte das Unternehmen eine kostengünstigere Prüflösung und hat sich daher für eine elektro-dynamische Prüfmaschine von ZwickRoell entschieden.
Die Qualitätsanforderungen des OEM-Kunden gaben dem Motorlager-Hersteller vor, die viskoelastischen Eigenschaften seiner Motorlager unter Verwendung eines Prüfprotokolls zur dynamisch-mechanischen Analyse (DMA) zu überprüfen. Das Protokoll umfasste eine statische Druckvorprüfung zur Definition der zulässigen statischen Steifigkeit, gefolgt von einer dreiphasigen dynamischen Prüfung bis zu 100 Hz. Die für die viskoelastische Leistung des Motorlagers akzeptablen Toleranzwerte wurden innerhalb der Grenzwerte der dynamischen Steifigkeit und des Verlustwinkels definiert.
Der Hersteller erkannte die Probleme bei der Sicherstellung der Prüfsteuerung und -stabilität bei höheren Frequenzen. Besonders viskoelastische Komponenten stellen Herausforderungen für die Materialprüfung, da Kraft und Weg phasenverschoben sind. Bei Tests im Rahmen der Wegregelung führen zunehmende Frequenzen für einen bestimmten Weg zu einer Erhöhung der Kraftamplitude. Es ist daher ein schnelles Erreichen und eine stetige Kontrolle der erforderlichen Spitzenwerte erforderlich.
Das Unternehmen wandte sich an ZwickRoell für eine ölfreie Prüflösung. Nach vorbereitenden Tests kam man zu der Entscheidung, dass die Installation einer elektro-dynamischen Linearmotorprüfmaschine (LTM, Linear-drive Testing Machine) den größten Mehrwert für die Bedürfnisse und anspruchsvollen Prüfungsanforderungen des Kunden bot. Das vollständige ZwickRoell Prüfpaket umfasste eine 5-kN-LTM mit maßgeschneiderten Komponentengriffen sowie die testControl ll- und testXpert R Sequencer-Software. Die LTM verfügt über einen zentralisierten internen Inkrementalgeber, der direkt auf der Kraftachse positioniert ist, um sicherzustellen, dass absolut präzise Prüfkolbenmessungen innerhalb eines Bereichs von +/-2 µm erzielt werden. Dies garantiert bei der Verwendung als Regelgröße in Kombination mit den 10-kHz-Regelungs- und Datenerfassungsraten genaueste Messergebnisse der testControl II Steuerungseinheit.
Die LTM benötigt nur Stromzufuhr für den Betrieb. Im Unterschied zu einer servohydraulischen Lösung sind weder Wasser, Öl noch Hydraulik-Schlauchleitungen erforderlich. Der Elektromotor nimmt nur so viel Strom auf, wie für die Durchführung der jeweiligen Prüfung benötigt wird. Dies führt zu erheblichen Kosteneinsparungen, insbesondere bei hohen Prüffrequenzen. Langfristig hat die LTM nur minimale Wartungsanforderungen, da das System über ein verschleißfreies Prüfkolben- und Bremssystem verfügt.
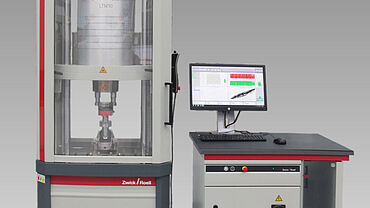